Chapter 112 Mobile-Bearing Total Knee Arthroplasty
Indications for total knee arthroplasty (TKA) have expanded as prosthetic designs, implant materials, and surgical techniques have improved. Although early total knee designs were generally reserved for older and sedentary patients with debilitating pain and loss of function, excellent clinical results with 10- to 15-year outcomes have encouraged many surgeons to consider performing TKA on younger patients, who have higher activity demands.10–12,15,20,55,58 Patient expectations for increased function and longer survivorship following TKA continue to drive advances in both surgical technique and component design. Integrating established and successful TKA design concepts with the current kinematic and biomechanical discoveries will continue to answer the public’s demand for improvements in TKA stability, function, component longevity, and patient satisfaction. One successful design concept that has evolved over the last 3 decades to meet the increased demands is the development of the mobile-bearing TKA. The careful integration of clinical and laboratory studies has led to advances in development of mobile-bearing TKA systems.
Design Rationale of Mobile-Bearing Total Knee Arthroplasty
Early TKAs were performed prior to comprehensive understanding of the importance of alignment and soft tissue balancing. First-generation instruments were used that lacked alignment guides or size-specific cutting blocks. Early clinical TKA failures often resulted from malalignment, instability, and the use of implants with excessive prosthetic constraint. Although increased constraint provided by hinged or extremely conforming unlinked TKA systems improved the stability of TKA, the torsional, coronal, and sagittal stresses normally shared by the surrounding soft tissue–stabilizing structures were transferred through the implant to the fixation interface,5 resulting in premature TKA failure secondary to aseptic component loosening.* Biomechanical studies have also shown that highly conforming fixed-bearing TKA designs are intolerant of higher rotational and anteroposterior translational kinematic motion patterns that are commonly encountered after TKA, with increased polyethylene wear frequently observed.17,27,41,43,65 Subsurface polyethylene stresses experienced in situations of malalignment have also been shown to be significantly higher in highly conforming fixed-bearing TKA systems than in less conforming fixed-bearing or highly conforming mobile-bearing TKA designs.17,43,65
Although these low-conformity TKA designs significantly reduced stresses transmitted to the fixation interface, this also decreased the contact area between the femoral component and polyethylene-bearing surface. The lower the conformity at the articulating countersurfaces, the less the contact area between these surfaces. Decreased articular congruity increases detrimental subsurface contact stresses experienced by the polyethylene and also increases the amount of cross-shear stresses, which risks accelerated polyethylene wear. The use of round-on-flat and flat-on-flat bearings produces point and line loading conditions at the articular interface, respectively, with an overall reduction in contact area through which polyethylene loads are distributed. Because the contact stress experienced at the polyethylene surface is inversely proportional to the degree of conformity between the femoral condyles and tibial polyethylene insert, reduction of contact area with low-conformity designs led to accelerated polyethylene wear and subsequent premature TKA failure.42,60
Fluoroscopic kinematic evaluations of round-on-flat and flat-on-flat articulations have also demonstrated an increased incidence of paradoxical anterior femoral translation during deep flexion, instead of controlled posterior femoral rollback, and reverse axial rotation patterns. These abnormal kinematic patterns are likely secondary to a reduction in articular conformity with resulting instability.* This paradoxical motion produces detrimental cyclical tensile shear stresses at the articulating surface, further increasing the risk of accelerated polyethylene wear.5,14
Strategies to reduce polyethylene wear include the use of thicker polyethylene bearings,5,6 improvements in polyethylene locking mechanisms of modular tibial components to reduce potential backside wear,29,56,66 the use of improved sterilization techniques,† returning to the use of TKA designs with increased articular surface conformity, and the use of mobile-bearing TKA systems.10–12,15,48,53
As noted, an important component design concept for reducing contact stresses at the articulating surface and effectively reducing polyethylene wear is increasing the articular conformity. The higher the conformity of the articular surfaces, the lower the amount of cross-shear stresses, the greater the articular surface contact area, the less the subsurface polyethylene contact stress per unit area, and subsequently the less polyethylene wear seen. Analyses of contact area versus contact stress have demonstrated a dramatic reduction of contact stress as the contact area is increased. Because of the logarithmic relationship between contact area and stress, increasing the contact area beyond 350 to 400 mm2 reduces contact stresses further but to a substantially lesser degree57 (Fig. 112-1). Conformity can be achieved in multiple planes. In contrast to total hip arthroplasty, in which conformity may be achieved in all planes, the focus in TKA is primarily on achieving sagittal and coronal plane conformity. It has been demonstrated that increasing coronal plane conformity is the most critical plane to reduce peak polyethylene stresses, particularly in the presence of femoral condylar liftoff.5,27,41,59
Biomechanical Advantages of a Mobile-Bearing Total Knee Arthroplasty
The increased sagittal plane conformity typically present in most mobile-bearing TKA designs provides the opportunity of improved control of anteroposterior translation, with reduced paradoxical anterior femoral translation, particularly when tested during gait.26,64 The increased coronal plane conformity typically present in mobile-bearing TKA also increases the contact area and lessens the increased contact stresses that are present if femoral condylar liftoff occurs.5,27,41,59 This has been observed using TekScan analysis.61 During testing of a flat-on-flat design in good alignment with equal loading of each condyle, peak polyethylene stresses reach approximately 16 MPa. When the same design is loaded in 3 degrees of varus malalignment, shifting the load to one condyle, as occurs with femoral condylar liftoff, the peak stresses dramatically increase to 38 MPa, far exceeding the yield strength of polyethylene (20 to 22 MPa). Similar testing performed with a TKA design with increased coronal conformity has demonstrated peak polyethylene stresses increasing only to 16 MPa with varus loading conditions (Fig. 112-2). Numerous studies have shown that the increased conformity in mobile-bearing designs substantially increases contact area and reduces contact stresses, which should reduce the rate of polyethylene wear.14,33,49,61,65
Greenwald and Heim33 have demonstrated contact areas of mobile-bearing TKA during gait range from approximately 400 to 800 mm2 which minimizes contact stresses to 14 MPa or less (Fig. 112-3). This magnitude of contact area is substantially greater than what is typically seen in most fixed-bearing TKA designs (200 to 250 mm2; Fig. 112-4) Other finite element evaluations have similarly demonstrated reduced polyethylene contact stresses as a direct result of increased contact area, further supporting the observations of Greenwald and Heim.7,47,50 The advantage of this increase in contact area is reflected in knee simulator wear studies of fixed- versus mobile-bearing TKA. McNulty and colleagues45 and McEwen and associates,44 in separate laboratory evaluations, both demonstrated significantly diminished polyethylene wear rates with highly conforming rotating platform designs when compared with similarly designed fixed-bearing systems. In the McNulty study, a 94% wear reduction was observed when analyzing a highly conforming rotating platform design versus a similar fixed-bearing TKA design, whereas the McEwen study noted over a fourfold reduction in wear with testing of a rotating platform TKA (Fig. 112-5).
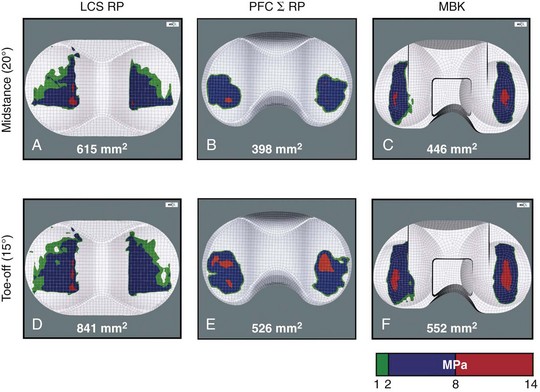
Figure 112-3 Contact area and stress analysis demonstrating high polyethylene contact areas (mm2) and low peak stresses (MPa) of three mobile-bearing TKA designs.33
(From Greenwald AS, Heim CS: Mobile-bearing knee systems: ultra-high molecular weight polyethylene wear and design issues. Instr Course Lect 54:195–205, 2005.)
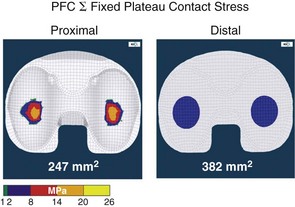
Figure 112-4 Contact area and stress analysis demonstrating a lower polyethylene contact area (mm2) and higher peak stress (MPa) in a fixed-bearing TKA design.33
(From Greenwald AS, Heim CS: Mobile-bearing knee systems: ultra-high molecular weight polyethylene wear and design issues. Instr Course Lect 54:195–205, 2005.)
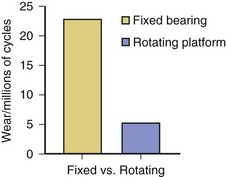
(From Mobile Bearing Total Knee Arthroplasty, Medscape: [http://www.medscape.com/viewprogram/3133, 2004].)
Most rotating platform systems use a flat tibial tray–polyethylene countersurface that allows freedom of the polyethylene insert to rotate around a central post on a highly polished, cobalt-chrome surface with a very low surface roughness. In vivo fluoroscopic kinematic studies conducted with two commonly implanted rotating platform designs (LCS RP and PFC Sigma RP, DePuy, Warsaw, Ind) have confirmed that polyethylene bearing rotation predictably occurred in all subjects tested.25,40 To evaluate the polyethylene-bearing position, four metallic beads were inserted at known positions into each bearing by the implant manufacturer, because the polyethylene would otherwise be transparent during fluoroscopy. Computer-assisted design (CAD) models were then created for the polyethylene inserts with the four strategically placed beads. Using a CAD model-fitting algorithm, the orientation of the femoral component and tibial tray were initially determined. The polyethylene insert was then made transparent and only the four beads were visible in the CAD model. The best fit with the CAD model of the four metallic beads onto the four beads visible in the fluoroscopic image was then determined using the same automated computer model-fitting process (Fig. 112-6). Once the process determined the best-fit match, the polyethylene insert could be visualized and axial rotation measurements of the rotating platform bearing relative to the femoral component and tibial tray were determined. These analyses have demonstrated that most axial rotation in these rotating platform designs occurs at the polyethylene bearing–tibial tray interface as the polyethylene bearing “follows” the rotation of the femoral component.28
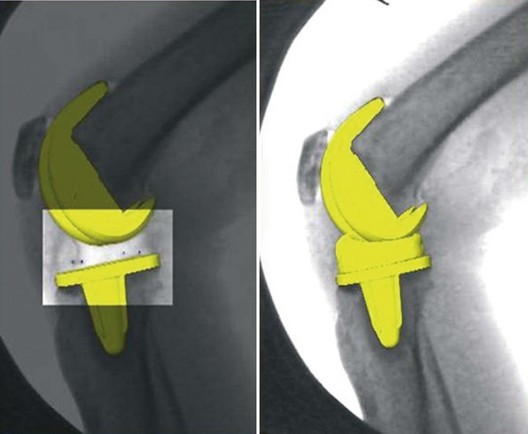
(From Mobile Bearing Total Knee Arthroplasty, Medscape: [http://www.medscape.com/viewprogram/3133, 2004].)
All rotating platform knee designs, however, are not the same kinematically. Garling and coworkers32 performed a similar fluoroscopic kinematic evaluation of 10 rheumatoid patients implanted with a different rotating platform TKA (NexGen LPS mobile, Zimmer, Warsaw, Ind) and found that the femoral component underwent greater axial rotation than the mobile polyethylene-bearing insert, suggesting that the femoral component was sliding on the top of the insert. They concluded that this finding was possibly attributed to the limited articular conformity in this design, an anterior pivot point for the rotating platform, insert impingement, or fibrous tissue caught between the insert and tibial tray. Therefore, the kinematic finding of polyethylene-bearing rotation in conjunction with the femoral component is a design-specific condition.
Rotation of the rotating platform polyethylene insert with the femoral component, independent of the rotation of the firmly fixed tibial tray, creates the potential for self-alignment of the polyethylene bearing with the femoral component. Self-alignment is advantageous for optimizing the kinematics of the prosthesis, reducing cross-shear stresses experienced by the polyethylene bearing surface, and maintaining acceptable stresses on posterior cruciate–substituting tibial posts. This self-aligning behavior with a highly conforming design has been shown to maintain large, centrally located surface contact areas at the femorotibial articulation during flexion-extension and axial rotation of the knee,65 which is much more difficult to achieve in fixed-bearing TKA designs.
An additional advantage of the self-aligning feature of rotating platform TKA systems is facilitation of central patellar tracking. In a fixed-bearing TKA, if substantial malrotation of the tibial component relative to the femoral component is present (especially tibial component internal rotation), the tibial tubercle can become lateralized, enhancing the risk of patellar subluxation. A rotating platform design, through bearing rotation, typically provides for greater self-correction of the component malalignment, allowing better centralization of the extensor mechanism. We have reviewed 1318 consecutive primary TKA performed by the senior author (DAD) over a 6-year period.68 All subjects were implanted using a single posterior-stabilized knee design (Sigma Press-Fit Condylar, DePuy). The femoral and patellar components were identical and the tibial component type was a mobile-bearing rotating platform tibial design or a fixed-bearing tibial design (all-polyethylene or modular metal-backed tibial component). The selection of a fixed- versus mobile-bearing TKA was primarily based on patient age, with subjects younger than 70 years receiving a mobile-bearing TKA. Mobile-bearing TKA devices were implanted in 940 cases (71.3%; 940 of 1318) and fixed-bearing knees were implanted in 378 cases (28.7%; 378 of 1318). The overall prevalence of lateral release was 7.9% (104 of 1318 knees). The incidence of lateral release in the fixed-bearing group (14.3%; 54 of 378) was found to be significantly higher (P < .0001) than in the mobile-bearing group (5.3%; 50 of 940).
The magnitude of axial rotation occurring during deep flexion activities is an important factor in knee implant design. An in vivo fluoroscopic evaluation of over 1000 TKAs incorporating 33 different fixed- and mobile-bearing TKA designs has demonstrated that most TKAs will experience less than 10 degrees of axial rotation with normal postoperative activities.24 However, in this large multicenter analysis, a number of subjects experienced normal or reverse axial rotational magnitudes greater than 20 degrees during these same activities. which are beyond the rotational boundaries of most fixed-bearing TKA designs. Therefore, mobile-bearing TKA designs that provide more freedom of rotation should reduce rotational polyethylene impingement, with the potential for reduction of polyethylene wear. In addition, studies examining the contribution of posterior cruciate–substituting (PS) polyethylene post wear to TKA failure have shown that excessive axial rotation in PS fixed-bearing designs can predispose to premature polyethylene wear and compromise the integrity of the central post.54 This occurs because of lateral and medial post impingement with attempted excessive rotation of a fixed square tibial polyethylene post in a fixed femoral intercondylar housing. The freedom of rotation present in rotating platform designs allow them to adapt to a greater range of axial rotation without creation of rotational impingement and wear on posterior cruciate–stabilizing posts.
The additional polyethylene-metal interface at the undersurface of the polyethylene bearing has raised concerns about the generation of additional polyethylene particles and accelerated polyethylene wear. With fixed-bearing TKA systems, backside polyethylene motion against a rough tibial tray that is not designed to accommodate motion has shown significant polyethylene wear and subsequent periprosthetic osteolysis.29,56,66 In rotating platform systems, a rotating yet flat polyethylene bearing is matched against a highly polished, cobalt-chromium surface with extremely low surface roughness. To date, backside polyethylene wear has not emerged as a clinically significant issue in rotating platform designs. Retrieval studies that have physically examined the backside bearing surface of rotating platform polyethylene inserts have reported only limited evidence of significant undersurface wear.35,36
One explanation for the lack of clinically significant backside polyethylene wear is the decoupling of multidirectional motions occurring at the articular interfaces with rotating platform TKA designs.44,46 In fixed-bearing systems, all rotational, translational, and flexion-extension motion patterns are experienced at a single (superior) articular surface. Therefore, the superior aspect of a fixed-bearing polyethylene insert experiences multidirectional motion pathways. In a rotating platform design that allows no anteroposterior translation, the inferior, or tibial tray–polyethylene countersurface, is designed to experience purely rotational (reciprocal-unidirectional) motion patterns. In mobile-bearing designs in which the polyethylene bearing tracks with the femoral component,25,40 the superior articular surface (femoral component–polyethylene interface) primarily experiences flexion-extension (reciprocal-unidirectional) motion because rotation is occurring on the inferior aspect of the bearing. Pooley and Tabor52 have reported that when high-density polyethylene is subjected to unidirectional sliding, the molecules tend to align along the direction of sliding, resulting in lowering of the coefficient of friction, potentially reducing wear of the material. Conversely, when the material is exposed to multidirectional wear pathways, increased cross-shear stresses are created that accelerate polyethylene wear. Additional laboratory studies have shown that the multidirectional shear stresses typically experienced at the single polyethylene interface in fixed-bearing systems may contribute to the generation of 4 to 10 times the polyethylene wear experienced at the unidirectional interfaces in rotating platform designs.39,48 Therefore, the use of rotating platform TKA designs can reduce polyethylene wear by decoupling multidirectional motions to more monodirectional motion patterns at two differing interfaces, thus reducing cross-shear stresses and wear occurring at both interfaces (Fig. 112-7).
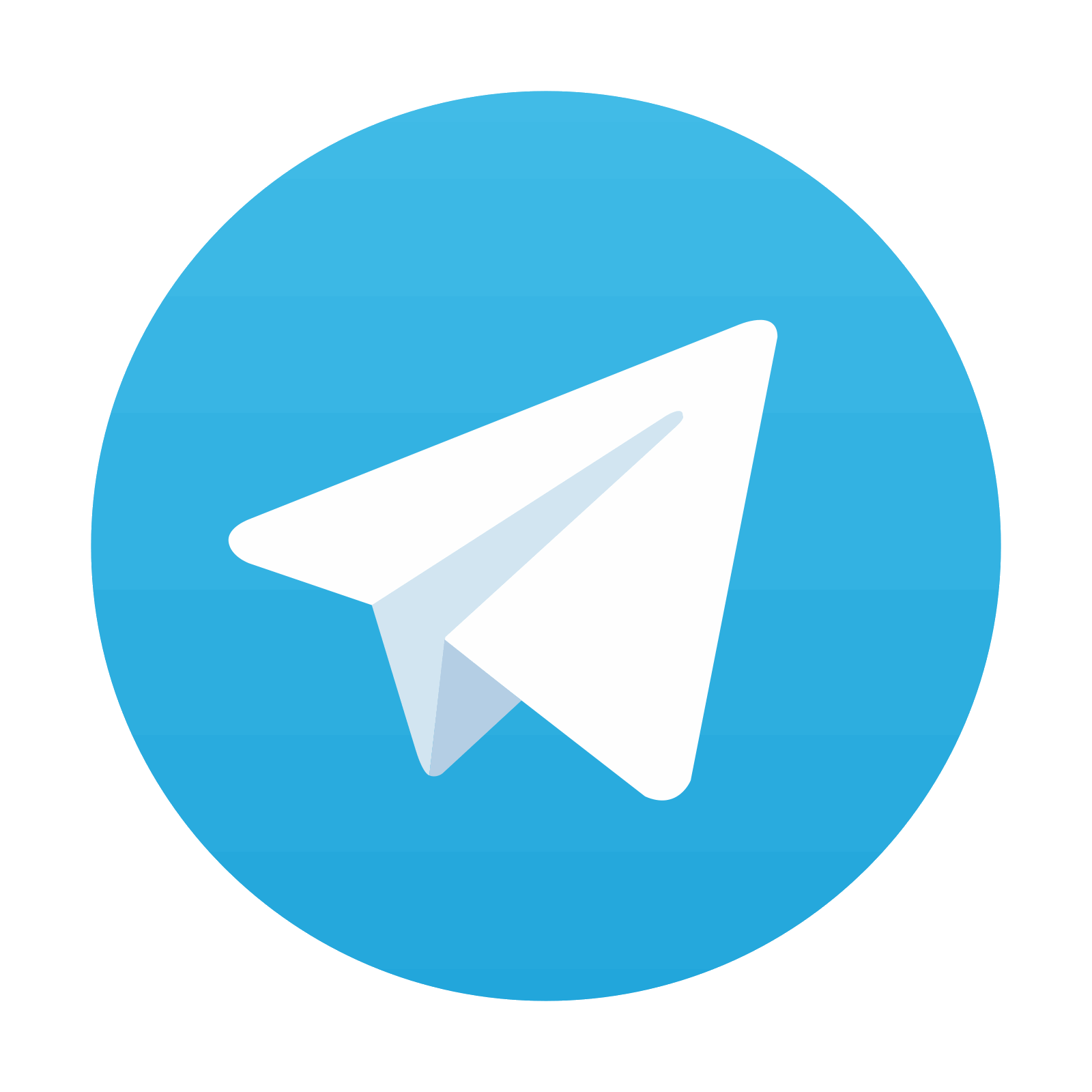
Stay updated, free articles. Join our Telegram channel
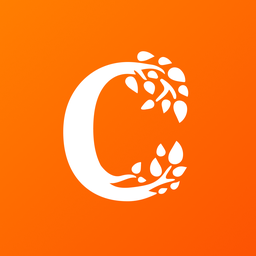
Full access? Get Clinical Tree
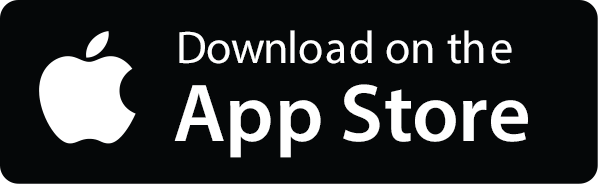
