Fig. 11.1
Removed femoral, tibial, and patellar components after aseptic loosening due to polyethylene wear (Courtesy of Gijs van Hellemondt)
In the study by Sharkey et al. [6], most of the 79 % revisions for aseptic loosening involved components in which only the tibial surface but not the keel was cemented. This was confirmed by Bert and Kelly [12], who reported a revision rate of 6.2 % for surface-cemented components within 3.2 years after surgery. Both authors recommended avoiding this particular cementing technique.
More aseptic loosening of the tibial component is observed in patients in whom only the tibial surface, but not the keel, was cemented.
By improving the quality of PE (melting process, compression moulding and sterilisation in oxygen-free inert environments), the PE wear in the early phase of TKR diminished dramatically [13]. It has to be noted that the shelf time with ageing of the sterilised PE still plays a role in increased wear rates [14]. Further improvements for longevity are expected by using highly cross-linked PE [15], although the effect on TKR is not yet clear [16, 17]. The second generation of highly cross-linked PE consists of mechanical [18] or sequential [19] annealing or diffusion of vitamin E [20]. Smoother surfaces for the femoral component, such as ceramics, may further reduce wear rate.
Polyethylene wear may differ in different TKR designs. In classical fixed-bearing designs, the rather flat PE surface articulates with the convex femoral component, leading to wear resulting from high peak loads in the small contact areas. In contrast, the mobile bearing concept increases the congruency between the PE and femoral components and reduces wear by reduction of peak load due to higher conformity. However, mobile bearings create wear on the undersurface between the PE and the polished tibial component [2]. The amount of wear may be reduced by limitation of gliding and rotation of the polyethylene. In addition, wear is created between the post and PE to guide the above-mentioned limited motion.
Major improvements in PE wear are expected due to high cross-linking and vitamin E impregnation.
11.2 Polyethylene Fracture
Fracture of the PE is a rare condition and seems to be more frequent in unicondylar knee arthroplasty [21, 22] than TKR (Fig. 11.2). However, in meniscal bearing TKR with two independent mobile bearings, this specific complication is still well known. Pegg et al. [22] associated fractures of the PE in mobile bearing unicondylar prosthesis with impingement and high wear in older models due to high oxidation of the PE. A further factor was the posterior marker wire, which was eliminated in later models. The fracture incidence was 3.2 % for phase 1, 0.74 % for phase 2, 0.35 % for phase 3 and 0 % for phase 3 without the posterior marker wire.
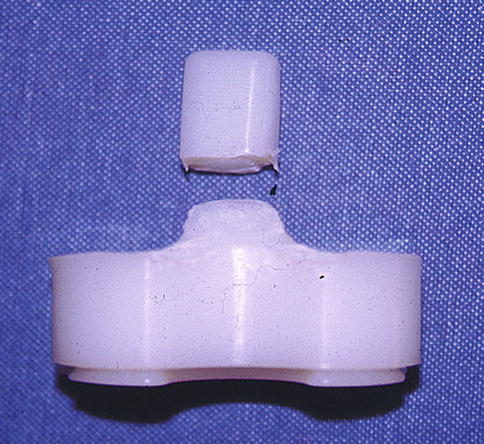
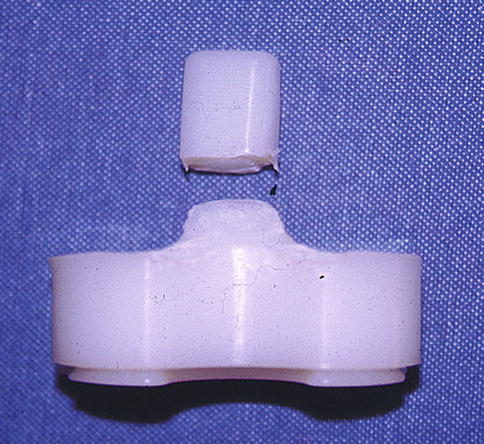
Fig. 11.2
Fracture of the polyethylene peg in TKR (Courtesy of Gijs van Hellemondt)
PE fracture is rare, mostly in unicondylar knee replacement (UKR) or meniscal bearing TKR.
11.3 Failure of Metal Components
This complication is uncommon today as material properties and stress loading are well known. Failure of a metal component can still be seen when the supporting bone is missing in the stage of advanced aseptic loosening [23–26]. Fractures of the femoral component can occur when there is insufficient bony ingrowth of cementless implants [26, 27]. In the case of Saito et al. [27], the bilateral fracture of femoral components was associated with higher activity levels and increased body weight. Smiszanský et al. [28] reported a case of a tibial stem fracture, probably due to progressive osteolysis of the proximal tibia. Springorum et al. [29] reported a case of a fatigue fracture of the hinge pin in a constrained TKR with persisting valgus deformity of 16°.
Cook and Thomas [30] reported a series of four porous-coated cementless TKR components of different manufacturers that fractured 12–48 months after surgery. The reason was, in all cases, a weakened component due to the porous coating process. Two cases involved the tibial tray, one a femoral and one a metal-backed patellar component. From 2000 to 2002, a total of 274 incidents were reported to the surveillance and registration system for medical products in Germany concerning TKR and total hip arthroplasty [21]. At that time, approximately 50,000 primary TKR were implanted annually; 42.6 % of these occurred within 1 and 87.9 % within 5 years after the index surgery. Only 20.4 % were caused by an error in the manufacturing process. In 88.4 %, implant failure was the reason for revision surgery. Fractures of the PE occurred in 2, femoral component in 7 and tibial component in 11 cases, respectively. Manzotti et al. [31] reported a high fracture rate of 4.9 % of implants in 121 revised unicompartmental knee arthroplasties. In this investigation, the femoral components fractured early after the index surgery and the tibial components later. The femoral ones involved older designs and were always located near a peg, whereas the tibial fractures occurred on the posterior part of the component. Nevertheless, the overall reported failure rate for implants due to production errors seems to be quite low.
Due to advances in material properties, failure of metal components is rare. Only a few cases are reported, which are due to extensive aseptic loosening.
11.4 Wear of Metal Components
Wear of metal components only plays a role in cases with extensive PE wear leading to direct contact of femoral (Fig. 11.3) and tibial (Fig. 11.4) metal components (Fig. 11.5). In TKR, the combination of different alloys is not rare. In some femoral TKR components, titanium shafts are connected to chrome cobalt (CrCo) components, at least in revision systems. Some systems use CrCo screws to fix the PE to the tibial tray in aluminium titanium (AlTi) alloy. Barrett et al. [32] presented at the closed EKA (European Knee Associates) meeting of November 2012, held in Oxford, preliminary results of five TKRs before revision because of PE wear or aseptic loosening. In every case, chrome and cobalt ions were dramatically increased in synovial fluid and blood serum. The conclusion was that increased metal ions could be an indicator for a failing TKR because of wear, not only of the PE but also for the metallic components. The rise in the cobalt level could be observed not only in cases with fatigue articulation wear but also in one case with wear of a CoCr alloy screw fixing the PE to an AlTi alloy tibial tray. These preliminary results are part of an ongoing study involving all revision TKRs in Southampton.
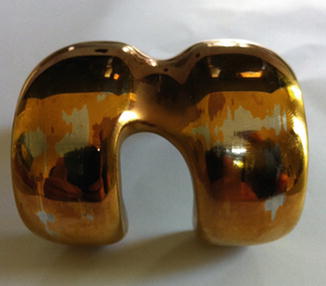
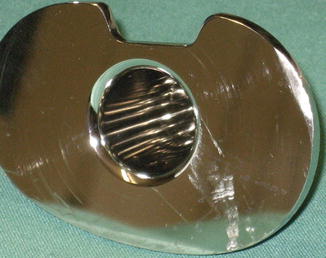
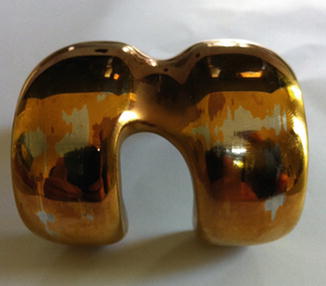
Fig. 11.3
Metal wear of the femoral TKR component (Courtesy of Gijs van Hellemondt)
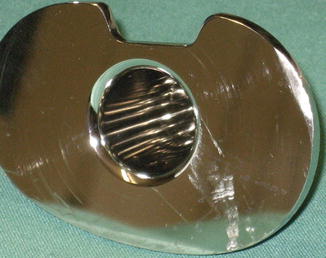
Fig. 11.4
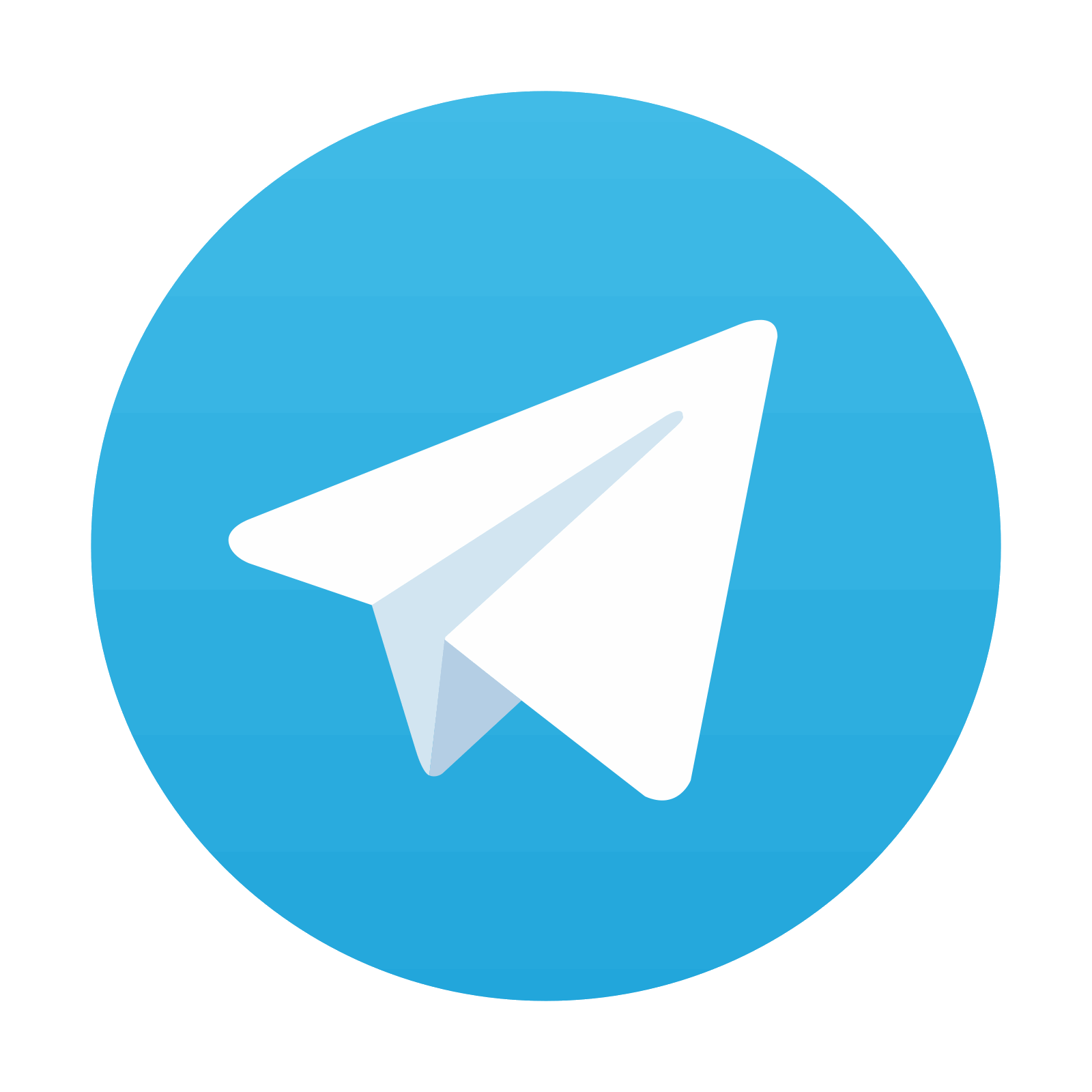
Metal wear of the tibial TKR component
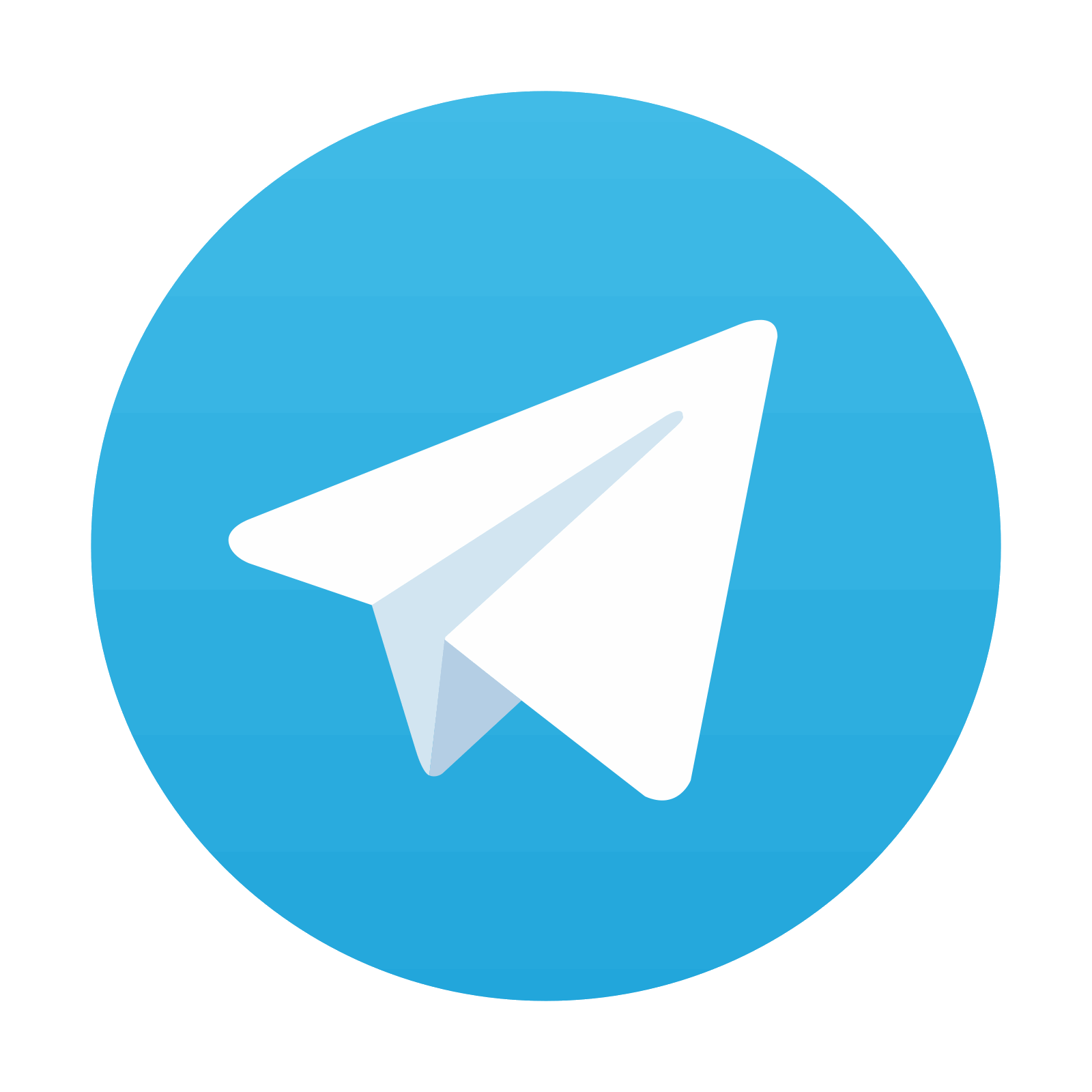
Stay updated, free articles. Join our Telegram channel
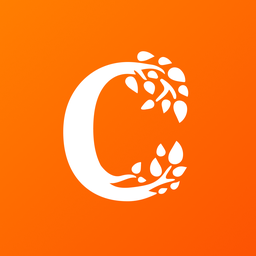
Full access? Get Clinical Tree
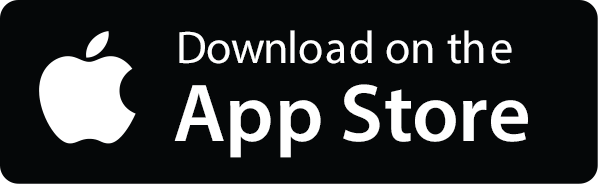

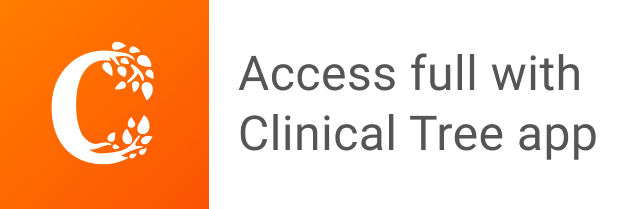