15 The Headless Compression Screw
Several different devices are available for fixation of small bony fragments, such as those encountered in fractures and nonunions of the scaphoid. These devices aim to
Stabilize the fragments
Provide interfragmentary compression
Be both technically easy and quick to insert
Be suitable for both open and percutaneous insertion
Cause minimal trauma during insertion
Rarely require removal
Be competitively priced
The Headless Compression Screw (HCS) (Synthes, West Chester, PA), has been designed to satisfy all of these requirements. It differs from other currently available devices in that it allows the surgeon to adjust the amount of interfragmentary compression.
▪ Basic Science
Over the past 5 decades, animal and clinical studies from the AO/ASIF group have demonstrated that interfragmentary compression facilitates fracture healing. In a bone such as the scaphoid, secondary bone healing through callus formation will not occur because the scaphoid is covered almost entirely by articular cartilage and hence lacks periosteum. If a scaphoid fracture is going to heal, it must therefore do so by primary bone healing.
On the other hand, anecdotal evidence would suggest that some surgeons remain concerned about applying too much interfragmentary compression, believing that this can both squeeze out any vascularity from the fracture edges and/or cause fracture instability, collapse, and malunion.
The HCS has been designed to provide all the positive benefits of previous implants, while adding the potentially significant benefit of allowing the surgeon to accurately control how much compression is applied at the fracture site.
▪ Implant Design
The HCS is available in shaft diameters of 3.0 mm, 2.4 mm, and 1.5 mm. All except the 1.5 mm screws are cannulated.

Externally ( Fig. 15.1 ) the screw resembles a Herbert screw, but there are crucial differences.
The leading threads (tip) cut a thread profile in both fragments as the self-drilling, self-tapping implant is inserted ( Fig. 15.2 ). The pitch in the two larger-diameter screws (3.0 and 2.4 mm) is 1.2 mm in both the head and the tip, but the head features a double thread; each thread’s starting point is at 180 degrees to that of the other. As the thread on the head enters the near fragment, the double-frequency pitch not only allows smooth insertion of the implant into the bone (since a new thread profile does not need to be cut), but it increases the stability of the implant in the near fragment as it cuts an extra new thread exactly in between the existing threads.

The implant is available with a short-tip thread (4 to 10 mm, depending on total screw length) and a long-tip thread (5 to 16 mm). It is critical that all the threads of the screw tip have crossed the fracture line into the far fragment before compression is achieved.
▪ Instrumentation Design
Guide Wire
The guide wire required for implants of this size has a diameter of 1.1 mm. Stainless steel guide wires of that diameter often bend on insertion—particularly in the hard bone usually found in young male scaphoids. To resolve this difficulty, the 1.1 mm guide wires with threaded tip are manufactured from a different grade of stainless steel to that used in implants. The “stiffer” stainless steel used in guide wires has a bending strength 1.5 times that of implant stainless steel (similar to spring steel), and maintains its path better than standard stainless steel wire, ensuring much more accurate placement of the guide wire.
Compression Sleeve
The unique and critical part of the design of this system is its ability to give the surgeon complete control over how much compression is obtained at the fracture site. A compression sleeve delivers this feature.
The compression sleeve has an internal thread at its tip, which matches the threads of the head of the HCS. On selection of the most appropriate length of implant for a particular case, that screw is then attached to the compression sleeve, so that the screw and sleeve become one item ( Fig. 15.3 ).
As the screw is introduced into the predrilled bone track, the screw–sleeve construct is rotated by hand to advance the screw into bone ( Figs. 15.4A,B ). The leading threads of the screw cross the fracture site and advance into the far fragment.
When the tip of the compression sleeve abuts the cortical bone of the near fragment, further rotation of the screw–sleeve construct will continue to advance the screw into the far fragment. As it does so, the screw pulls the far fragment toward the near fragment and compression is achieved ( Fig. 15.4C ).

The surgeon can adjust the amount of compression by varying the number of turns of the screw–sleeve construct. The surgeon will judge the optimum amount of compression by directly visualizing the fracture (or graft–bone interface) and by the feel of increasing torque resistance.

The tip of the compression sleeve leaves a 4.65 mm compression footprint on the articular cartilage, which is similar to other headless screws. Releasing the screw from the compression sleeve at this point would lose most of the compressive force.
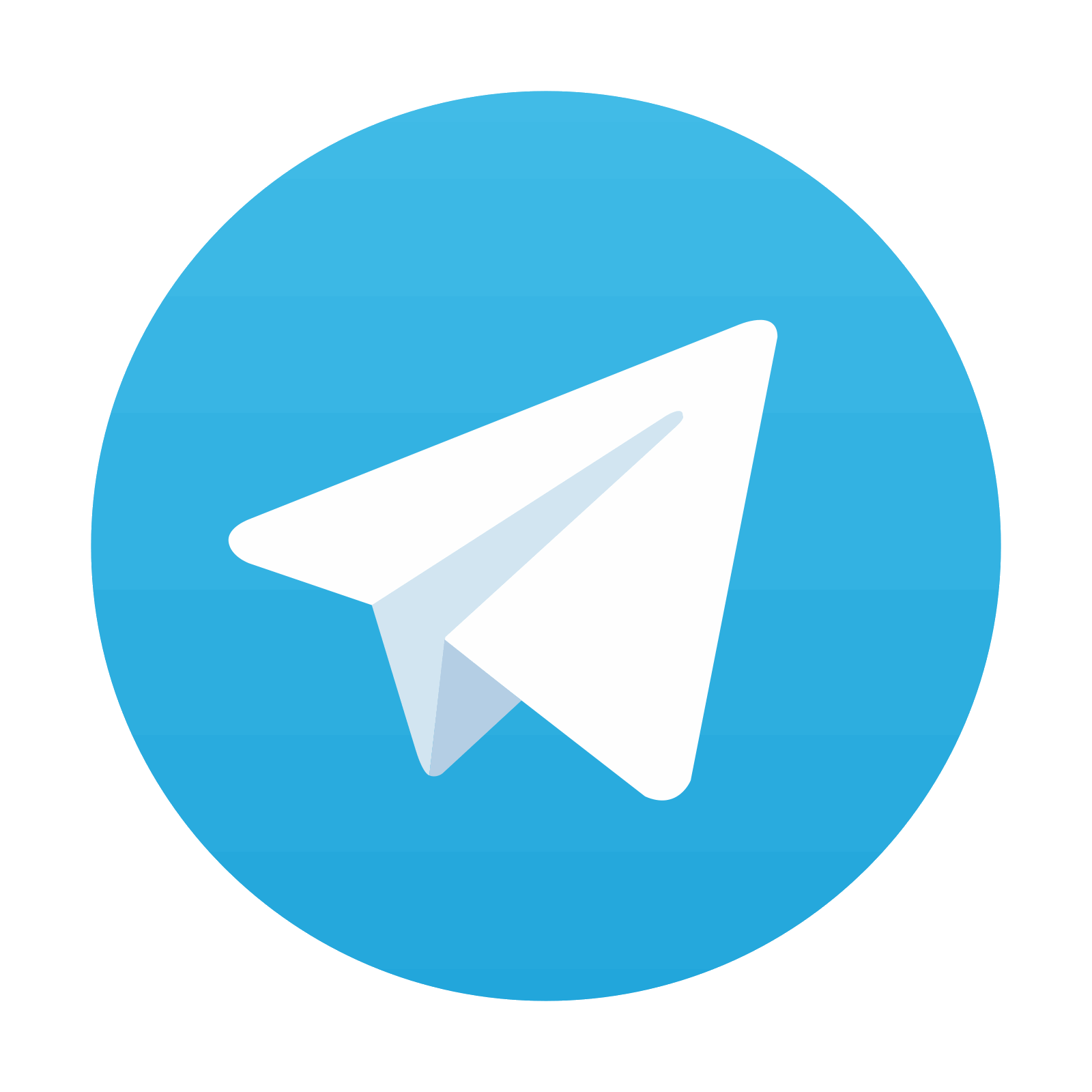
Stay updated, free articles. Join our Telegram channel
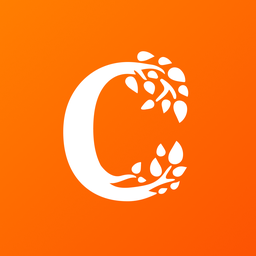
Full access? Get Clinical Tree
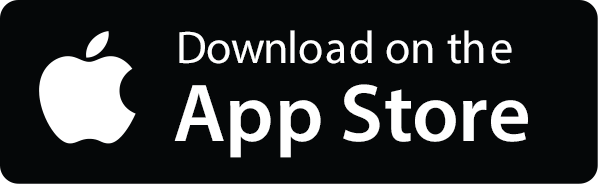

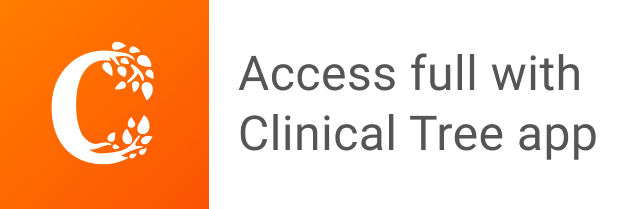