Fig. 2.1
Tendon hierarchical structure. Collagen molecules are assembled into progressively larger bundles, until the level of the tendon itself is reached. Reproduced with permission from Reuther KE, Gray CF, Soslowsky LJ: Form and Function of Tendon and Ligament, in O’Keefe RJ, Jacobs JJ, Chu CR, Einhorn TA (eds): Orthopaedic Basic Science, 4th edition. Rosemont, IL, American Academy of Orthopaedic Surgeons, 2013

Fig. 2.2
Polarized light microscopy of crimp in a mouse supraspinatus tendon. (a) Collagen fibrils with crimp without an applied load. (b) Collagen fibrils uncrimped while under an applied tensile load. Reproduced with permission from Miller, KS, Connizo, BK, Feeney, F, Soslowsky, LJ: Characterizing local collagen fiber re-alignment and crimp behavior throughout mechanical testing in a mature mouse supraspinatus tendon model. J Biomech 2012; 45(12)
2.3 Mechanics
Tendon’s longitudinal and fibrillar structure results in anisotropic and nonlinear properties. Anisotropy refers to a material having directionally dependent properties. In the tendon, this results in mechanical properties that are up to 1000 times higher during tensile testing along the longitudinal versus transverse axes (Lake et al. 2010). In addition to anisotrophic properties, tendons also display nonlinear characteristics under an applied force, which results in an initial increase in stiffness as more force is applied. The nonlinear characteristics of the tendon result in two distinct regions in a load-elongation curve, termed the toe and linear regions (Fig. 2.3). The toe region of the load-elongation curve describes the behavior of tendons at low deformation, where the collagen fibril crimp is straightened. As deformation increases through the toe region into the linear region, crimp disappears and the collagen fascicle itself stretches (Dale et al. 1972; Diamant et al. 1972; Atkinson et al. 1999). As deformation continues to increase through the linear region, the tendon accumulates irreversible damage and eventually ruptures. The anisotropic and nonlinear properties of tendons are further explained by other properties, such as viscoelasticity.


Fig. 2.3
Stress-strain curve demonstrating the toe and linear regions
Viscoelasticity is the ability for materials to display both elastic and viscous behavior. One component of a viscoelastic material is viscosity, a measure of resistance to deformation. Although it has been traditionally used to characterize fluids, it can also describe other materials, such as rubber, glass, and biopolymers. Elasticity is the ability of a material to return to its original shape after forces that cause deformation are removed. The elasticity of a material can be described in the context of structural or material properties. Stiffness is a structural property that defines the extent to which a material resists deformation from an applied force. Stiffness is derived from the slope of the load-elongation curve (Fig. 2.4a). In contrast with structural properties, material properties are normalized properties, taking into account tissue size or shape. Material properties are calculated using stress and strain. Stress is the intensity of the load or force normalized by the cross-sectional area. Strain is a relative measure of deformation, a change in length divided by the original length. These parameters are used to calculate Young’s modulus, a material property that describes elasticity and is defined as the slope of the stress-strain curve (Fig. 2.4b). Both load-elongation and stress-strain curves are generated through mechanical testing. Mechanical testing protocols can be adapted to measure different types of properties, including viscoelastic properties.


Fig. 2.4
(a) Tendon load-elongation curve. Various material properties can be derived from this curve. (b) Tendon stress-strain curve. This curve normalizes properties to each individual tendon’s parameters, including length and area. Reproduced with permission from Woo SL, Debski RE, Withrow JD, Janushek MA: Biomechanics of knee ligaments. Am J Sports Med 1999; 27(4):533–543. (c) Creep test where load is held constant and amount of tendon deformation is measured. (d) Stress relaxation test where deformation is held constant and stress is measured. Both the creep test and stress relaxation test demonstrate viscoelastic behavior of tendon in response to load
Dynamic mechanical analysis is one methodology used to assess tendon viscoelastic properties. This analysis is performed by applying an oscillatory stress and measuring the strain response. A phase lag is a delay between the applied stress and resulting strain response. Phase lags may be measured to describe the viscous or elastic behavior of a material. In purely elastic materials, there is no phase lag; the strain response occurs simultaneously with the applied stress (Fig. 2.5a). In purely viscous materials, strain lags stress by 90° or one quarter cycle behind the stress applied (Fig. 2.5b). The phase lag for any material will always be between 0º and 90º, making purely elastic and purely viscous materials both the upper- and lower-bounds for phase lag, respectively. Additionally, viscoelasticity of tendons can also be characterized via hysteresis. Hysteresis represents the amount of energy dissipated as a result of internal friction during mechanical loading and unloading. Like all materials, tendon dissipates energy throughout loading and unloading cycles. Thus, hysteresis can be derived from the area between loading and unloading load-elongation curves during mechanical testing (Fig. 2.6).



Fig. 2.5
Stress and strain response curves that represent a perfectly elastic material (a), with 0° phase lag between stress and strain, and a perfectly viscous material (b), with a 90° phase lag between stress and strain

Fig. 2.6
A graph showing the loading and unloading curves of an idealized rubber band, with the area between the curves, highlighted by red lines, representing hysteresis
The viscoelastic properties of tendon also lead to phenomena known as creep and stress relaxation. Creep is an increase in deformation of a material under a constantly applied load. Initially, elongation under a constant load occurs quickly, however, this response slows with time (Fig. 2.4c). Cyclic creep occurs during cyclic dynamic testing, where each consecutive load cycle generally causes an increase in the amount of deformation. In contrast with creep, stress relaxation holds strain constant. Stress relaxation in tendon is demonstrated when a measured load in a tendon decreases over time with a constant strain (Fig. 2.4d). This load initially decreases under a constant strain quickly, but the rate of change decreases over time as it approaches equilibrium. Cyclic stress relaxation also generally occurs when a tendon is exposed to cycling dynamic testing, requiring a decreased force to reach a constant strain over time.
2.4 Mechanical Testing Methods
There are many parameters that affect the results of mechanical testing. In order to standardize measurements for comparison, cyclic preconditioning is commonly performed before mechanical testing. Preconditioning is performed at low loads to stretch the tendon without causing irreversible damage. After applying a preconditioning protocol, a steady state is reached where no further changes occur unless the protocol is altered (Fung 1993; Miller et al. 2012). After preconditioning, many mechanical testing methods such as ramp to failure, dynamic cyclic, and fatigue testing can be used to assess tendon mechanical properties.
Ramp to failure testing is the most common form of mechanical testing used to assess tendons. One purpose of this method is to find the maximum force and displacement a sample can endure before failure. It is typically performed by applying a constantly increasing displacement on the sample until failure. In addition, this test is also used to determine the stiffness and modulus of both the toe and linear regions and the transition point between these regions. It is not uncommon for ramp to failure testing to be performed in series with dynamic testing. This is because the low strains used in dynamic testing to measure creep and stress relaxation do not alter the tendon’s integrity, making it is possible to combine these tests together (Fig. 2.7).


Fig. 2.7
An example of a tendon viscoelastic testing protocol. The test begins with preconditioning, followed by a stress relaxation and a series of frequency sweeps. Multiple stress relaxations can be performed at higher strains, followed by more frequency sweeps. The test ends with a ramp to failure test
Many different parameters set during dynamic cyclic testing affect tendon response due to the viscoelastic nature of the tissue. The dynamic modulus derived from cyclic dynamic testing is defined as the stress amplitude divided by the strain amplitude. Thus, the dynamic modulus measurement is affected by testing parameters, based on the strains and frequencies that are selected. These moduli describe how tendons behave depending on rate of loading and loading history. As previously discussed, creep and stress relaxation can also be used to characterize the viscoelastic behavior of tendons. Creep and stress relaxation are affected by the magnitude of force or strain, respectively. A more comprehensive method of evaluating creep and stress relaxation is to perform dynamic testing using various magnitudes of force. Examining these properties across a range of values provides a deeper insight into the viscoelastic characteristics of the sample.
Fatigue testing is another type of cyclic testing which consists of cycling within a defined range of force or displacement, and recording the number of cycles until failure. During this testing, tendons have three phases marked by changes in stiffness (Freedman et al. 2014). Initially, the tendon increases in stiffness, reaches a maximum, and finally descreases in stiffness, demonstrating a triphasic behavior pattern. This decrease in stiffness is attributed to an accumulation of sub-rupture damage, which results in increases in deformation and decreases in stiffness prior to failure. This testing is useful for characterization of tendons that undergo repetitive loads, such as the Achilles tendon and other tendons that function in locomotion (Fung et al. 2009, 2010; Wren et al. 2003).
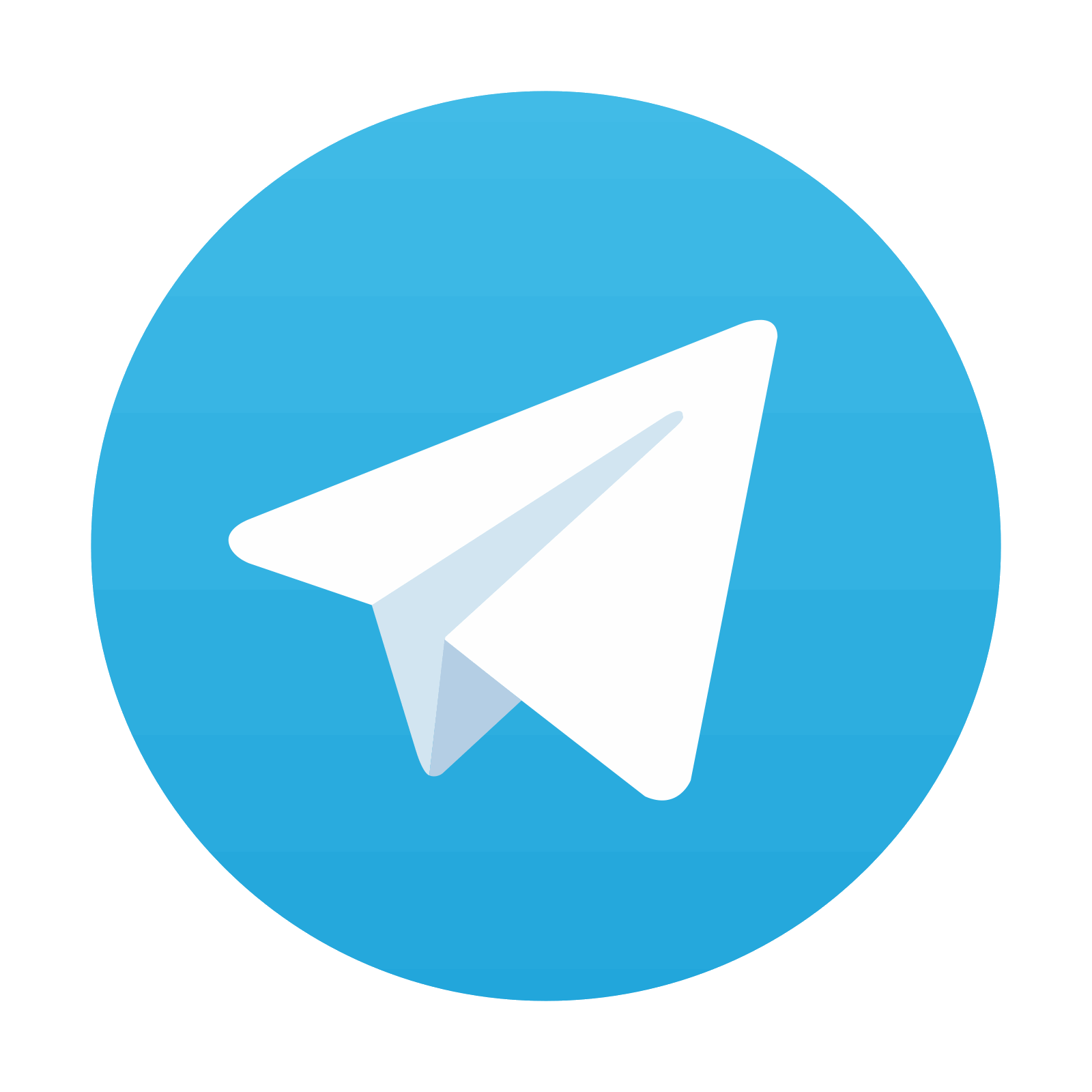
Stay updated, free articles. Join our Telegram channel
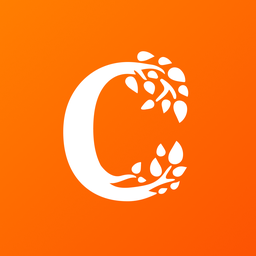
Full access? Get Clinical Tree
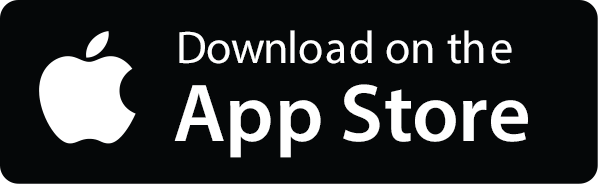
