Polyethylene
Michael Aynardi
David Pedowitz
INTRODUCTION
For more than five decades, polyethylene has been one of the most common bearing surface materials used in joint arthroplasty. Although total hip and knee replacements have enjoyed excellent long-term clinical outcomes, the initial experience with total ankle arthroplasty (TAA) was not as successful and had unacceptable failure rates.1 It is likely that the decreased survivorship was the result of a lack of understanding of the complexity of the ankle joint as well as inferior implant designs and surgical techniques.2,3
With regard to the bearing surface, the ankle joint is not a simple hinge or ball and socket; rather, it has complex biomechanics, including translational as well as rotational components, which occur about a changing instant center of rotation.4 One of the most striking features of the ankle, however, is that its contact area is only 350 mm2. The hip and knee have contact areas of 1,100 and 1,200 mm2, respectively. With a three times smaller contact area with identical loads as the hip and knee, the ankle experiences substantially higher contact forces.5
An improved understanding of these factors has played an important role in the development of newer-generation total ankle replacements (TARs), with improved survivorship as a result of better biomechanics and decreased rates of wear. The purpose of this chapter is to provide an understanding of polyethylene, its various properties, potential complications, implant design, and the future of research as it relates to TAR.
POLYETHYLENE
DEFINITION
Polyethylene is a plastic formed from the polymerization of ethylene (C2H4) into long hydrocarbon chains (Fig. 20.1). The polymers organize into long folded chains that form into a sheet-like area known as the crystalline lamellae, which is surrounded by amorphous disorganized regions. The orientation and organization of polyethylene are dependent upon several factors, including its molecular weight and how it is processed. Although there are many forms of polyethylene that are commercially available, nearly all orthopedic implants utilize highly cross-linked polyethylene, which refers to the covalent bonds between the ethylene chains. The high molecular weight of the highly cross-linked polyethylene results in increased toughness, better abrasive wear, and an increase in impact strength compared to those of lesser weight. These enhanced mechanical properties, however, come at a cost: highly cross-linked polyethylene is more brittle.
HISTORY
For the first 30 years that polyethylene was used in joint replacement, there were little changes in its processing and composition. Processing at that point consisted of polyethylene blocks carved into the appropriate shapes, which were then sterilized in air. Two major changes in manufacturing have occurred in the last 15 years, which have substantially improved the durability of this plastic. The first was the sterilization of the product in an inert atmosphere instead of air, which has led to a reduction in free radical formation, which can degrade the polyethylene while it is being stored. The second was the development of second-generation ultra-high-molecular-weight polyethylene (UHMWPE) components, which are highly cross-linked and thermally treated.6,7 and 8 These improvements have substantially reduced wear rates and thus improve implant longevity.
STERILIZATION AND PROCESSING
Polyethylene is fabricated in one of three methods: computeraided manufacturing (CAM) extrusion, compression molding, or direct molding. In CAM extrusion, the polyethylene is extruded through a die under heat and pressure to form a cylindrical bar. This bar is then machined and processed into the final shape. With compression molding, the polyethylene is molded into one large sheet, then cut and divided into smaller pieces prior to machining. Finally, direct molding takes polyethylene and molds it directly into the finished product. All three forms of processing are utilized by various manufacturers. Sterilization of polyethylene is most commonly performed via exposure to gamma radiation. When sterilized by gamma radiation (2.5 to 4.0 Mrad) in air, free radicals are generated and oxidative degradation occurs. This results in increased wear rates, delamination, and fracture of the polyethylene. When gamma irradiation is performed in an inert atmosphere, the number of free radicals is decreased. Furthermore, exposure of the polyethylene to increased doses of radiation (between 5 and 10 Mrad) results in greater cross-linking. As a result, sterilization via gamma irradiation in an inert atmosphere results in polyethylene with improved resistance to adhesive and abrasive wear but with decreased mechanical properties as a result of the higher cross-linking. Additional postirradiation processing includes melting and annealing to reduce oxidation. During melting, the polyethylene is changed from its crystalline state to a partial amorphous state, which can reduce wear properties and help eliminate free radicals, though fatigue cracking has been reported. During annealing, the polyethylene is heated below the melting point and crystallinity is retained; however, annealing leaves a greater number of free radicals and may lead to early oxidation over time. Although melting may reduce oxidation, its clinical significance is yet to be determined.9,10
SECOND-GENERATION UHMWPE
Concerns regarding wear rates and oxidation eventually led to improvements in processing and the implementation of second-generation UHMWPE.8 Techniques utilized to reduce free radical formation during annealing with second-generation UHMWPE include incorporation of vitamin E, sequential irradiation and annealing, and mechanical deformation.11
Interestingly, these new techniques avoid melting during processing and result in improved cross-linking.
The theory behind sequential irradiation and annealing is that single high doses of irradiation create excellent cross-linking but prevent elimination of free radicals during annealing. Instead of using one large single dose of radiation, manufacturers now fractionate the radiation into more than one step while retaining the same cumulative dose. In this manner, they retain the same amount of cross-linking while reducing the amount of free radicals formed in the final product.8 Another method is the use of vitamin E, which is impregnated into the material in order to protect it against oxidation, which would obviate the necessity to melt the product. Yet, irradiation seems to reduce the number of vitamin E molecules and research has not yet defined its long-term effects. Finally, mechanical deformation below the polyethylene’s melting point occurs after irradiation. This alters the structure of the product where the free radicals are trapped, allowing them to be released. This is then followed by annealing to recover its initial structure.12,13,14,15 and 16 Currently, there are a multitude of manufacturers of polyethylene components, which are processed in a variety of combinations9; there is no strong evidence in the literature to support one particular implant over another at this time.
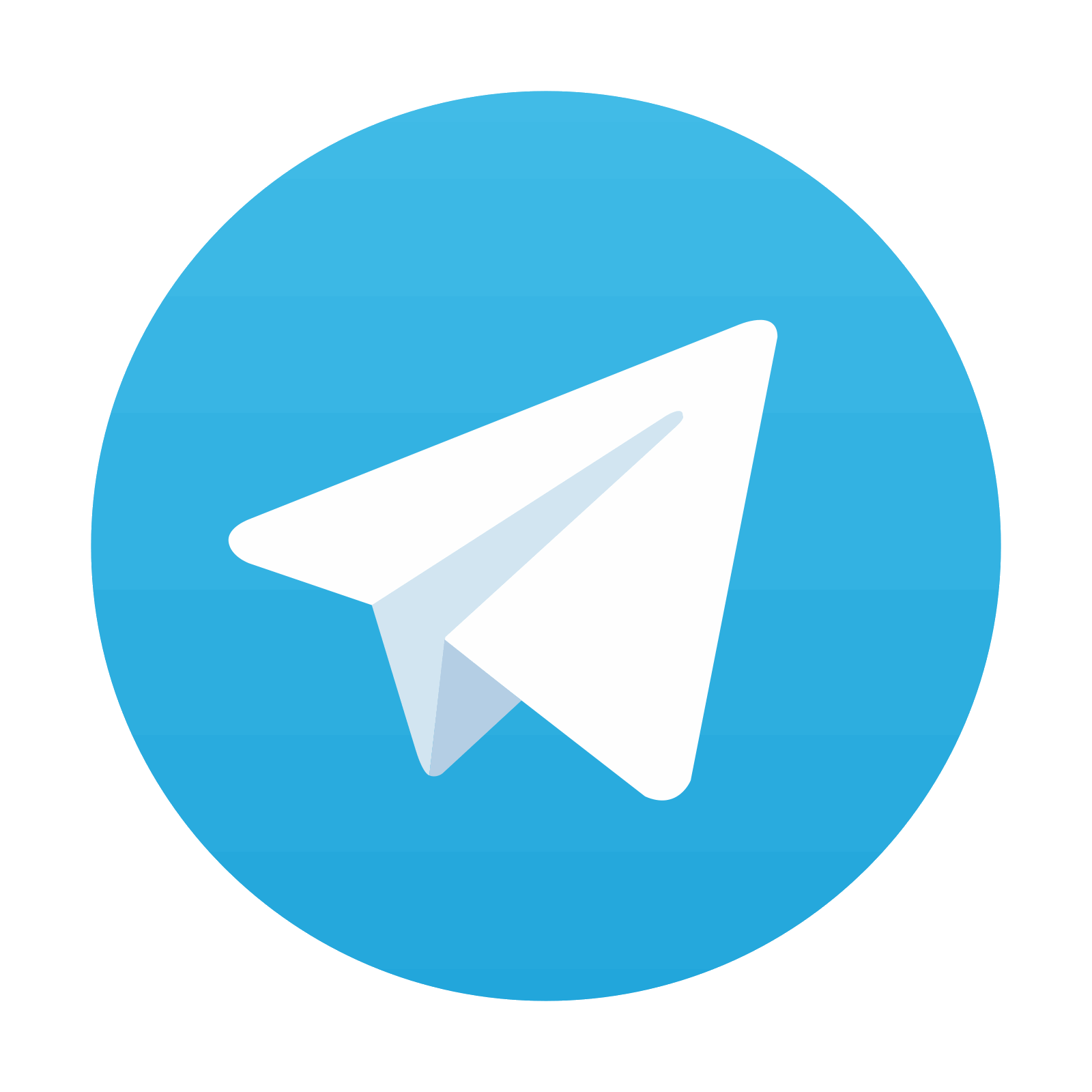
Stay updated, free articles. Join our Telegram channel
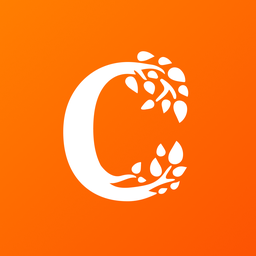
Full access? Get Clinical Tree
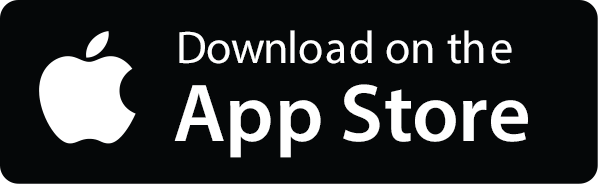
