CHAPTER 1 Evolution of Shoulder Arthroplasty
FIRST SHOULDER ARTHROPLASTY
Although Jules Emile Péan is credited with performing the first shoulder arthroplasty, it was probably Themistocles Gluck who first recognized prosthetic replacement as a potential treatment option in the shoulder.1 Gluck, a Romanian who studied in Germany in the second half of the 19th century, pioneered joint replacement for the treatment of tuberculosis infection. Gluck reported on his design of an ivory shoulder replacement but never documented its use in a living human subject.
The first recorded shoulder arthroplasty was performed in 1893 by Péan, a Parisian surgeon who replaced the shoulder of a patient suffering from tuberculous arthropathy who had refused amputation.2 Péan implanted a shoulder prosthesis designed and constructed by J. Porter Michaels, a Parisian dentist; the prosthesis consisted of a rubber humeral head that had been boiled in paraffin to harden it and was attached to a platinum shaft via a metal wire. A second metal wire attached the implant to the glenoid. The patient initially “did well” after the surgery before ultimately requiring removal of the prosthesis for recurrence of infection 2 years later.
FIRST-GENERATION SHOULDER ARTHROPLASTY
The first shoulder arthroplasty using a prosthesis with an anatomic design was performed in 1950 by Frederick Krueger.3 Krueger used a Vitallium implant created by molding proximal humeri obtained from cadavers. He successfully implanted this prosthesis in a young patient with osteonecrosis of the humeral head. The modern era of shoulder arthroplasty, however, was pioneered by Dr. Charles Neer. Neer originally performed hemiarthroplasty to treat complex proximal humeral fractures starting in 1953.4 Nearly 20 years later he would report on the use of shoulder replacement for the treatment of glenohumeral arthritis.5 Neer originally used a monoblock implant; however, variations in humeral head size among patients led to the concept of modularity, which allowed the use of variable humeral head diameters in shoulder arthroplasty. Monoblock implants are now commonly referred to as first-generation shoulder arthroplasty.
THIRD-GENERATION SHOULDER ARTHROPLASTY
In the late 1980s Boileau and Walch hypothesized that variations in anatomy prevented current first- and second-generation shoulder arthroplasty stems from achieving optimal fit within the proximal humerus.6 They undertook an anatomic study of the proximal humerus that yielded some important conclusions. They discovered that the proximal humerus could be modeled by using a sphere and cylinder. A portion of the sphere represents the articular surface of the proximal humerus. The diameter of the humeral head articular surface was found to be highly variable, as was the thickness of the humeral head. Thickness and diameter were found to have a fixed relationship and correlated with one another linearly. They further found the inclination of the anatomic neck of the humerus relative to the humeral diaphysis to be highly variable. Humeral retroversion, defined by the relationship of the humeral anatomic neck to the transepicondylar axis of the elbow, was found to vary by more than 50 degrees. Finally, the sphere (humeral head) was discovered to be offset, usually posteriorly and medially, from the cylinder (humeral diaphysis). These relationships are summarized in Table 1-1.
Table 1-1 ANATOMIC VARIABILITY OF THE PROXIMAL HUMERUS
Rights were not granted to include this data in electronic media. Please refer to the printed book. |
Several laboratory studies have demonstrated the clinical relevance of advances in design imposed by third-generation humeral implants. Harryman and colleagues demonstrated how placing too thick a humeral component had detrimental effects on glenohumeral motion,7 whereas Jobe and Iannotti found a decrease in the arc of available glenohumeral motion when using too thin a humeral head component.8 In an eloquent computer model, Pearl and Kurutz demonstrated the necessity of being able to vary the humeral head diameter, humeral head offset, and neck inclination angle of a humeral prosthesis to replicate the patient’s native anatomy (Fig. 1-1).9
GLENOID RESURFACING
Neer first reported on the use of a glenoid component in unconstrained shoulder arthroplasty for the treatment of glenohumeral arthritis in 1974.5 Neer’s original implant was a keeled cemented rectangular component (the same anterior-to-posterior diameter superiorly and inferiorly) with a radius of curvature matching the humeral head component.
Advances in glenoid resurfacing have occurred in component design and implantation techniques. Different component designs commonly used include cemented polyethylene keeled convex-back designs, cemented polyethylene keeled flat-back designs, cemented polyethylene pegged convex-back designs, and metal-backed designs. Convex-back designs have been shown experimentally to resist sheer forces better than flat-back designs do, and this has translated into fewer radiolucent lines around the glenoid component in the clinical scenario.10–12 The larger debate exists over whether to use a keeled or a pegged component. Laboratory studies have demonstrated less micromotion with pegged implants.13 Clinical studies, however, have reported both the superiority of pegs and the superiority of keels.14,15 Because radiographic comparison of these two types of implant is difficult, this debate remains unsolved at present. The original metal-backed designs consisted of a metal base plate secured with a screw-type mechanism and a modular polyethylene liner. The thickness of the metal often required that the polyethylene insert be very thin to avoid placing excessive tension on the gleno humeral soft tissues. This thinness resulted in poor wear characteristics of the polyethylene and caused implant failure.16 Many early metal-backed designs have been abandoned; however, implantation of a glenoid component without the use of cement is still appealing, especially in revision surgery, which may involve compromised glenoid bone stock. Research is ongoing in the development of new and improved metal-backed glenoid designs.
One of the most recent and significant advances in glenoid component design is recognition of the significance of glenohumeral prosthetic mismatch. Mismatch is defined as the difference in radius of curvature between the humeral head and glenoid component. Congruent articulations (mismatch = 0) allow optimal surface contact, minimize the risk of surface wear of the glenoid component, and contribute to increased joint stability. However, with these advantages comes a lack of obligate translation (translation between the articular surfaces that normally occurs with shoulder mobility and is absorbed by elastic deformation of the articular cartilage and the glenoid labrum). Lack of obligate translation may lead to loosening of the glenoid component by increasing the stress developed at the implant fixation site. Alternatively, noncongruent articulations (larger glenoid than humeral radius of curvature) allow obligate translation between the humeral head and the glenoid, thereby potentially decreasing the stress observed at the glenoid implant fixation site. Glenoid component wear and joint stability remain a concern in noncongruent articulations. Laboratory investigations have yielded some insight into appropriate mismatch in shoulder arthroplasty, including studies demonstrating that a 4-mm mismatch is necessary to best replicate normal shoulder mobility, and studies showing that mismatch in excess of 10 mm risks fracture of the polyethylene component.17,18 The clinical relevance of these laboratory studies was not clear, however, until Walch and coworkers reported on the influence of glenohumeral prosthetic mismatch on radiolucent lines occurring around the glenoid component.19 This study found that fewer radiolucent lines occurred at minimum 2-year follow-up when a radial mismatch of at least 6 mm was used during performance of total shoulder arthroplasty. An upper limit of mismatch was not established, however, thus prompting ongoing studies to discover the ideal glenohumeral prosthetic mismatch.
Another aspect of glenoid resurfacing that has evolved is the implantation technique of glenoid components. Neer originally recommended preparation of a keel slot with a curette to remove a large amount of bone and create a large cement mantle.5 More recently, Gazielly and colleagues introduced the bone compaction technique for implantation of keeled glenoid components.20 Radiolucent lines around glenoid components appear on the initial postoperative radiographs in many cases and have been attributed to technical deficiencies.21 The compaction technique of bone preparation addresses radiolucent lines in three ways. First, compaction of cancellous bone in the glenoid provides a more stable base for the glenoid component than does bone removal via curettage. Second, a compacted bone slot that has the same dimensions as the component keel allows a primary “press-fit” fixation that should help prevent micromotion of the component as the cement polymerizes. Third, the compaction technique uses a smaller amount of cement, which may decrease thermal necrosis of the adjacent glenoid bone. Clinically, a comparison of the curettage technique with the compaction technique has shown superiority of the compaction technique in minimizing radiolucent lines on immediate and 2-year postoperative radiographs.22
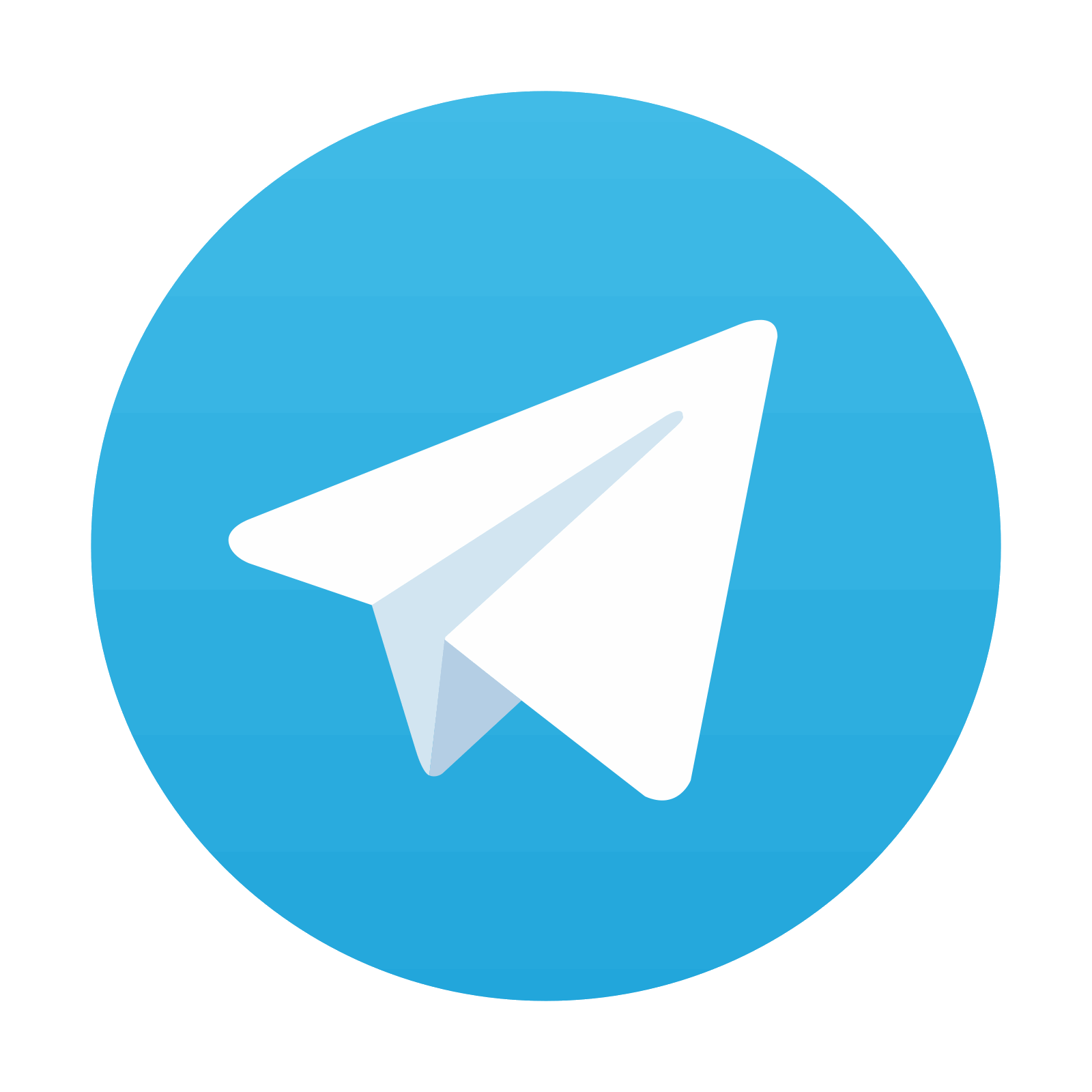
Stay updated, free articles. Join our Telegram channel
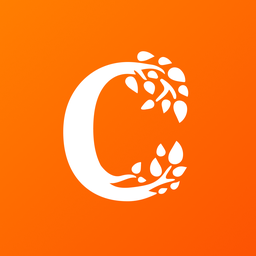
Full access? Get Clinical Tree
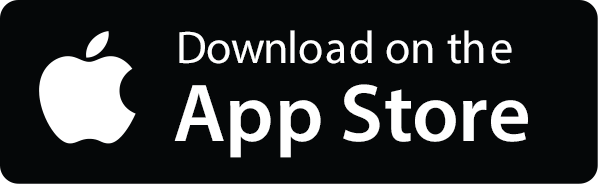
