3 Good Laboratory Practice and Quality Control
The need to follow good laboratory practice (GLP) when conducting preclinical safety and efficacy tests and studies was fostered in recent years by those authorities guiding and deciding upon medical device release for human use. To fulfill this requirement, medical device industry strongly adopted GLP procedures when conducting such safety and efficacy tests and studies.
Having experienced the benefits of GLP, industry now occasionally feels a quality awareness discrepancy when cooperating in basic or applied research with outside institutions, which have not yet installed the main pillars of GLP.
It has become evident that even when performing research studies or testing outside the direct scope of preclinical safety and efficacy tests and studies, following certain GLP rules is a prerequisite for high-quality output. It is thus the purpose of this chapter to introduce the key elements of GLP and quality control as based on international standards and guidance documents. Using the experience from a mechanically profiled testing laboratory in medical device industry (trauma implants), it gives examples of how the normative requirements may be translated in organizational and procedural terms.
3.1 Definitions
GLP is a quality system concerned with the organizational process and the conditions under which nonclinical health and environmental safety studies are planned, performed, monitored, recorded, archived, and reported. 1, 2
3.2 Scope of Good Laboratory Practice
GLP shall be applied for nonclinical safety and efficacy studies that support or are intended to support marketing permits and claims for medical devices for human use.1
However, it has to be emphasized that even in those cases where GLP is not mandatory, at least following its main guidelines is suggested: Neglecting them puts quality of work and results at risk; conclusions drawn on incorrect results may be wrong and thus subsequent work steps (like design optimization of a newly developed product based on non-GLP prototype testing) may waste valuable resources. GLP thus also helps to do it right the first time.
3.3 Key Elements of Good Laboratory Practice
There are two main groups of requirements to be addressed when implementing GLP 3:
Management requirements
Technical requirements This section will define and explain those requirements in detail.
3.3.1 Management Requirements Organization
The laboratory shall be or refer to a legal entity that can be held responsible and accountable for its work. A legal entity may be an association, corporation, partnership, proprietorship, trust, or individual that has legal standing in the eyes of law.
The laboratory has to have managerial, technical, and quality personnel, which needs the authority and resources necessary to properly carry out their duties. The laboratory needs to have a technical management installed that has overall responsibility for technical operations and provision of resources. In addition, a quality manager needs to be established who has direct access to the leadership level. All personnel must be held free of any influences that may adversely affect the quality of their work.
The organization including responsibilities, authorities, and interrelation of all personnel needs to be properly defined and described. The management needs to provide and enable adequate supervision of all staff, including trainees, by persons familiar and trained in methods and procedures. Fig. 3.1 shows a sample of an organizational chart that fulfills the requirements set forth per ISO 17025.3

Management System
The laboratory leadership shall establish a management system that is appropriate for the work scope of the laboratory. The management system may be documented in policies, programs, procedures, instructions, and charts that are necessary to operate the laboratory in a controlled and effective manner and to assure the quality of test results.
A core element of the management system is the quality management handbook, which includes the commitment to good professional practice and quality testing, the statement of the laboratory′s standard work scope, and the quality-related purpose of the management system. The quality management handbook shall be available and communicated and trained to all laboratory personnel.
Management Reviews
The management system along with the technical and quality activities shall be periodically reviewed by the leadership team to ensure continuing suitability and effectiveness of policies and procedures, and to introduce necessary changes and improvements.
Input sources for the management review may be policies, procedures, quarterly or monthly business reports prepared from laboratory personnel, audit reports, corrective action and preventive action (CAPA) summary reports, any external bodies’ assessments, results of inter-laboratory comparisons, and customer feedback and complaints.
Review outcome should result in a clear action list for improvement including objectives, action planning, and timelines for completion.
The management review is a key component of the continuous improvement process the laboratory shall constantly strive for. This applies to its whole body of policies, procedures, and activities on management and quality as well as the technical side. The typical cycle for improvement is shown in Fig. 3.2. 4

Document Control
The laboratory management needs to establish procedures to control all documents that form part of its management system: Besides the aforementioned policies, programs, and procedures, these may be standards, drawings, software, equipment manuals, etc. The document control should include guidelines for filing, archiving, approval, and issue control.
Control of Records
It is recommended that procedures be established for identification, indexing, collection, archiving, maintenance, and disposal of quality and technical records. This also applies to any electronically stored data. The system must ensure that all information on a test or study potentially influencing quality of results is easily accessible and retrievable (e.g., when the need to repeat a study arises or questions on the validity and correct data analysis are raised in, for example, statistics).
Complaints, Control of Nonconforming Testing Work
The laboratory must have policies and procedures for how to deal with nonconformances. Those must ensure responsibilities, authorities, and regulated steps to take in order to implement containment measures, evaluate the significance of any nonconforming work, execute corrections, take corrective actions, verify their efficacy, decide on and execute customer notification, and work recall if needed.
In order to address this requirement, it is recommended a CAPA system be installed under quality management. Such a system focuses on the investigation of root causes of nonconformities in order to prevent their recurrence (corrective action) or to prevent occurrence (preventive action).
Internal Audits
The laboratory shall periodically perform internal audits to check compliance of any management and technical activities versus policies, procedures, standards, and regulations.
It is the responsibility of the laboratory quality manager to plan and organize those audits as required. Major deviations shall be treated per the laboratory CAPA system and audit reports should be a major input to the management reviews periodically performed.
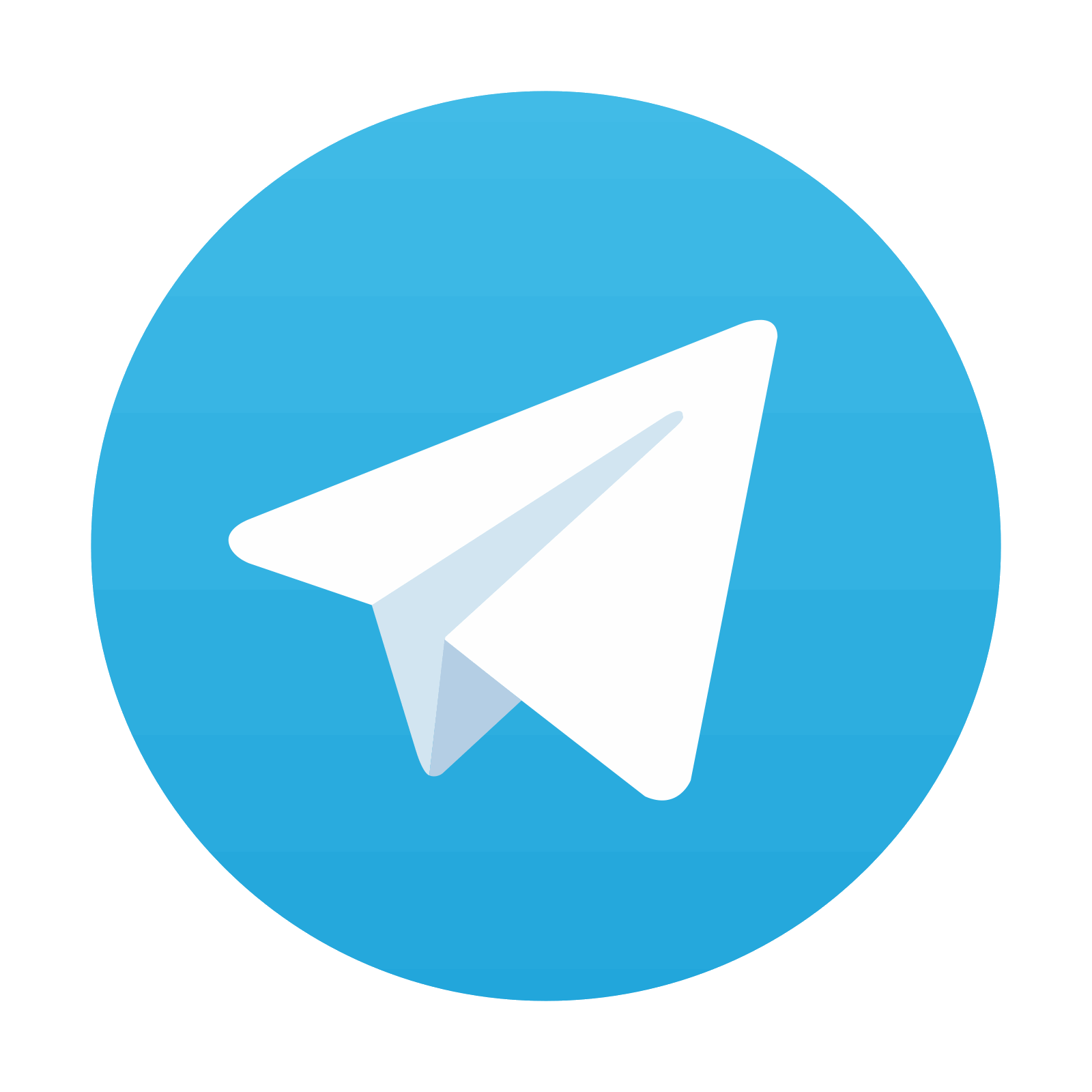
Stay updated, free articles. Join our Telegram channel
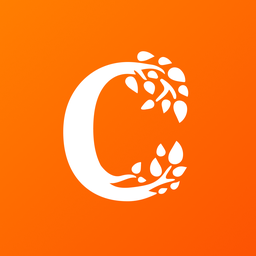
Full access? Get Clinical Tree
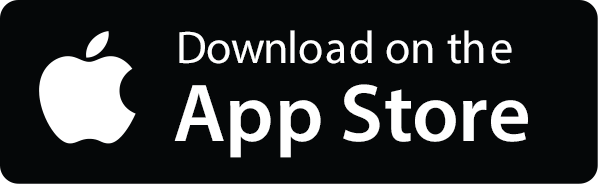

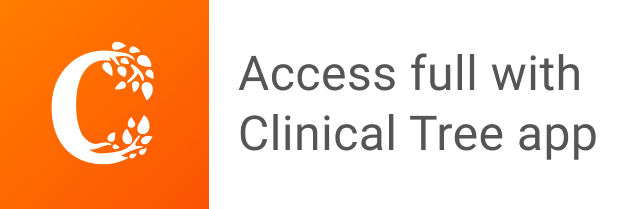