3 Deformation and Strength of Structures
The term structure designates an object built from one or more materials in a specific architecture. In this context, the term architecture refers to the geometrical shape of the object and the way in which its components are assembled and fixed together. Examples of structures in this sense are a beam made of wood, a vertebral body composed of an outer shell of cortical bone filled with trabecular bone, or a joint of the human body consisting of bone, cartilage, joint capsule, and ligaments. The mechanical properties of a structure depend on its architecture and on the mechanical properties of its building materials.
The deformation of a structure under load depends on several variables:
The nature of the load. The structure may be loaded by a compressive or a tensile force, by a moment, or by a combination of forces and moments. If it is loaded by a force, the deformation is measured in meters [m] or relative units [%] in relation to its initial dimensions. If it is loaded by a moment and torsion is observed, the deformation is measured in degrees [°]; if bending is observed, the deflection is usually measured in meters [m].
The architecture of the structure. The deformation of a beam under bending or torsion depends on its length and cross section. The deformation of a joint depends on the deformation of the bone and on the architecture of the cartilage and the ligaments crossing the joint.
The properties of the building materials. In the case of a wooden beam, the deformation depends on the type of wood used (for example: oak or pine). In the case of a joint, the mechanical properties of the building materials bone, cartilage, and ligament come into play, or in the case of an orthosis, the mechanical properties of steel and plastic materials. The mechanical properties are characterized by the moduli of elasticity and shear and by the elastic, viscoelastic, or plastic properties.
The strength of a structure is defined as that load which effects a destruction of the structure. Destruction occurs if the tensile, compressive, or shear stress in any one component of the structure exceeds its ultimate value, and the structure (or a part of it) is torn, fractured, or irreversibly deformed. Depending on the loading mode, we distinguish between compressive, tensile, or shear strength of a structure. Strength under tensile or compressive load is designated by the force effecting the destruction and is quoted in newtons [N]. Torsional or bending strength is designated by the moment effecting the destruction and designated in newton meters [Nm].
Tensile, compressive, bending, or torsional strengths of a structure are independent of one another and may assume widely different values. A pile of bricks, for example, has high compressive but very low tensile strength. The compressive strength of cortical bone is higher than its tensile strength. A rope, a muscle, or a ligament has high tensile but only low compressive, torsional, or bending strength.
Deformation and strength of structures may be determined experimentally or by calculation. For the experimental determination, the testing methods are similar to those employed when determining properties of materials. The structures are set up in a testing machine and loaded by a tensile or compressive force, or by a moment in bending or torsion. The resulting change in shape (deformation) is recorded in relation to the load. If the load is further increased, the load effecting destruction will eventually be found. Alternatively, a deformation can be imposed on the structure and the reaction force (that is, the resistance to the deformation) or the reaction moment can be recorded. It must be pointed out, however, that interpretation of the results of such experiments differs from interpretation of the results of experiments determining material properties. This is due to the fact that, when testing structures, the architecture as well as the properties of the building materials influence the result. It is obvious that a low-strength structure can be built with high-strength materials. On the other hand, a structure made out of relatively low-strength materials may have a high strength.
For structures composed of one single material and having simple geometrical shapes, formulae are available that allow deformation and strength to be calculated in the case of simple loading modes, provided the material properties are known. Simple geometrical shapes are, for example, beams or tubes with rectangular or circular cross sections. Simple loading modes include, for example, tension or compression or torsion about the axis of such beams. The prerequisite for the validity of these formulae is that the resulting deformations under load remain small. If more than one material is used to build a structure, and in the case of irregular shapes and simultaneous loading by forces and moments, deformation, stress, and strength can be determined by the finite element method.
3.1 Experimental Determination of Deformation and Strength
The relationship between deformation and load may vary within broad limits. In the following, this is illustrated by examples of different tissues and organs. A tensile test provides data on deformation and strength under a tensile force. Fig. 3.1 shows the tensile force of a ligament in relation to its increase in length. At each point of the force–deformation curve, the slope is approximated by the quotient dF/dL. In this expression dL designates the length change observed under a small change dF of the tensile force applied. dF/dL is termed the stiffness of the structure. Stiffness is measured in newtons per meter [N/m] or newtons per millimeter [N/mm]. The numerical value of the stiffness indicates how many newtons are necessary to effect a length change of 1 m or 1 mm respectively. In the case of torsion (see Figs. 3.5 and 3.7 ), torsional stiffness is defined as the slope of the moment versus the angle of the torsion curve. Torsional stiffness is measured in newton meters [Nm] (the angle being a dimensionless quantity).

The shape of the curve shown in Fig. 3.1 is typical of the behavior of soft tissues under tension. In general the force–deformation graph does not follow a straight line; the slope of the curve and thus the stiffness assume different values along the curve. In the example shown, the slope of the curve and hence the stiffness have low values under low forces and higher values under higher forces. In ligaments, this property is due to the collagen fibers becoming more and more aligned in the direction of the force as the tensile force increases.
If the magnitude of the tensile force F exceeds the strength of the structure, a partial or total rupture of the ligament is observed. In the example shown in Fig. 3.1 the first partial rupture occurred at a tensile force of about 200 N. It is a common finding in ligaments that rupture occurs stepwise, because under a given load not all fiber bundles of the ligament undergo the same deformation. In each bundle the ultimate tensile strain is reached at a different elongation of the whole ligament. In the example shown, complete rupture occurred only after an increase in length of about 3 mm. Between the point where the tensile strength of the ligament (about 200 N) was reached and the total rupture, the ligament can still transmit a tensile force, though of restricted magnitude.
Fig. 3.2 shows the force–deformation graph of human skin. In this example the initial region of high elongation under low forces (region of low stiffness) and the adjoining region with a relatively low increase of length under higher forces (region of higher stiffness) can be clearly distinguished. The force–deformation graph forms a hysteresis loop. The deformation is elastic because (at the levels of loading shown) no permanent deformation is observed after completion of the load cycle. The force–deformation curve of skin demonstrates that this structure is highly adapted to its physiological function (that is, enabling large deformations under low forces but only up to a certain limit).

Fig. 3.3 shows the force–deformation graph of passive elongation of a muscle in vitro. As in the preceding example, the stiffness assumes different values at each point of the graph. The graph forms a hysteresis loop. After completion of the loading cycle, the residual deformation subsequently decreases to zero. This structure is viscoelastic. We expect the force–deformation graph of a muscle measured in vivo to assume a different form, because innervation of a muscle will change its stiffness.

Fig. 3.4 illustrates the deflection of bones in a three-point bending experiment. In such an experiment the bone is supported at both ends and loaded in its mid-section by a force F. The deflection is measured at the point where the force is applied. All curves shown end at the point where fracture occurred. Force– deflection graphs of different bones are given here in one diagram merely to provide an overview. A quantitative comparison of deflection and strength of different bones, for example of fibula and femur, makes little sense, because deflection and bending strength depend on the bone material, the cross-sectional area, and the length of the bones. If, in contrast, effects of implantation-induced temporary immobilization or instrumentation have to be evaluated, conclusions can be drawn by comparing pairs of bones, for example the right and left femur specimen of a person or an experimental animal.

Fig. 3.5 shows experimental results for torsional deformation and torsional strength of bones. In this type of experiment, the bone is fixed at one end and a moment about the long axis of the bone is applied at the other. Deformation and torsional strength depend on the bone material, the length, and the shape of its cross section. It is therefore not surprising that large differences with respect to torsional stiffness (slope of the curves), torsional strength, and maximum deformation (end point of the curves) of the bones are observed.

Fig. 3.6 depicts the compression of a lumbar vertebral body by a force directed perpendicularly to the plane of the vertebral endplates. In this example, the stiffness (slope of the curve) increases with increasing load. The compressive strength of the vertebra shown is approximately 9 kN. After fracture, the ability to support a compressive load is not reduced to zero but is still approximately 5 kN. This is due to the fact that fragments of the trabecular bone may support one another until complete collapse occurs at larger deformations. In vivo, the ability to support some compressive force in the long run after occurrence of a compression fracture of a vertebra depends on whether and how fast the fractured bone material can be replaced by new bone.

If a structure contains components made out of viscoelastic or plastic materials, or if the components have some play in their connection so that small relative movements are possible, a permanent deformation is observed after the end of a load cycle. Fig. 3.7 illustrates this effect using the example of the passive, axial rotation of the cervical spine under the application of an external moment. In the example shown, the range of motion between maximum rotation to the right and to the left is approximately 160°. The angular position of the cervical spine in relation to the moment follows a hysteresis loop. The region of plastic deformation (that is, the deformation at zero moment) extends from +60°. to −60°. In this region the angular position depends on the mechanical history, that is, on the magnitude of the previously applied moment.

In the orthopedic and biomechanical literature, the region of plastic deformation of a structure is occasionally termed the neutral zone. Doubt may well be cast on the usefulness of this designation, because the well-established term plastic deformation already describes this effect. In addition, it must be pointed out that the extent of the plastic deformation is not characteristic of the structure under investigation but rather depends on the magnitude of the previously exerted load. If the load is increased or decreased, the “neutral” zone (plastic deformation) increases or decreases as well. Thus, the designation “neutral” zone is hardly appropriate for describing biomechanical characteristics of the human locomotor system.
Deforming a structure demands energy (work). When loaded by a force, the energy required to deform a structure (deformation energy) is defined as the momentary force multiplied by the momentary change in length. When loaded by a moment, the energy is defined as the momentary moment multiplied by the momentary change in angle. In both cases the dimension of the deformation energy is newton meters [Nm]. The total energy needed to achieve a specific deformation is determined by summation (or integration) of the deformation energy from the initial to the final state of deformation. It can be shown (the proof is not presented here) that the total energy required to effect a certain deformation is represented by the area (the integral) below the load–deformation graph. This is independent of whether the graph follows a straight line or some irregular curve.
Fig. 3.8 shows load–deformation graphs of structures A and B which have been differently deformed. Structure A exhibits a greater stiffness than structure B. However, the deformation energy, which depends on the shape of the load–deformation graph and on the extent of the deformation, is greater in case B than in case A. Practical use is made of this fact when damping impacts by means of a low-stiffness structure permitting a large deformation so that a large amount of energy can be absorbed.

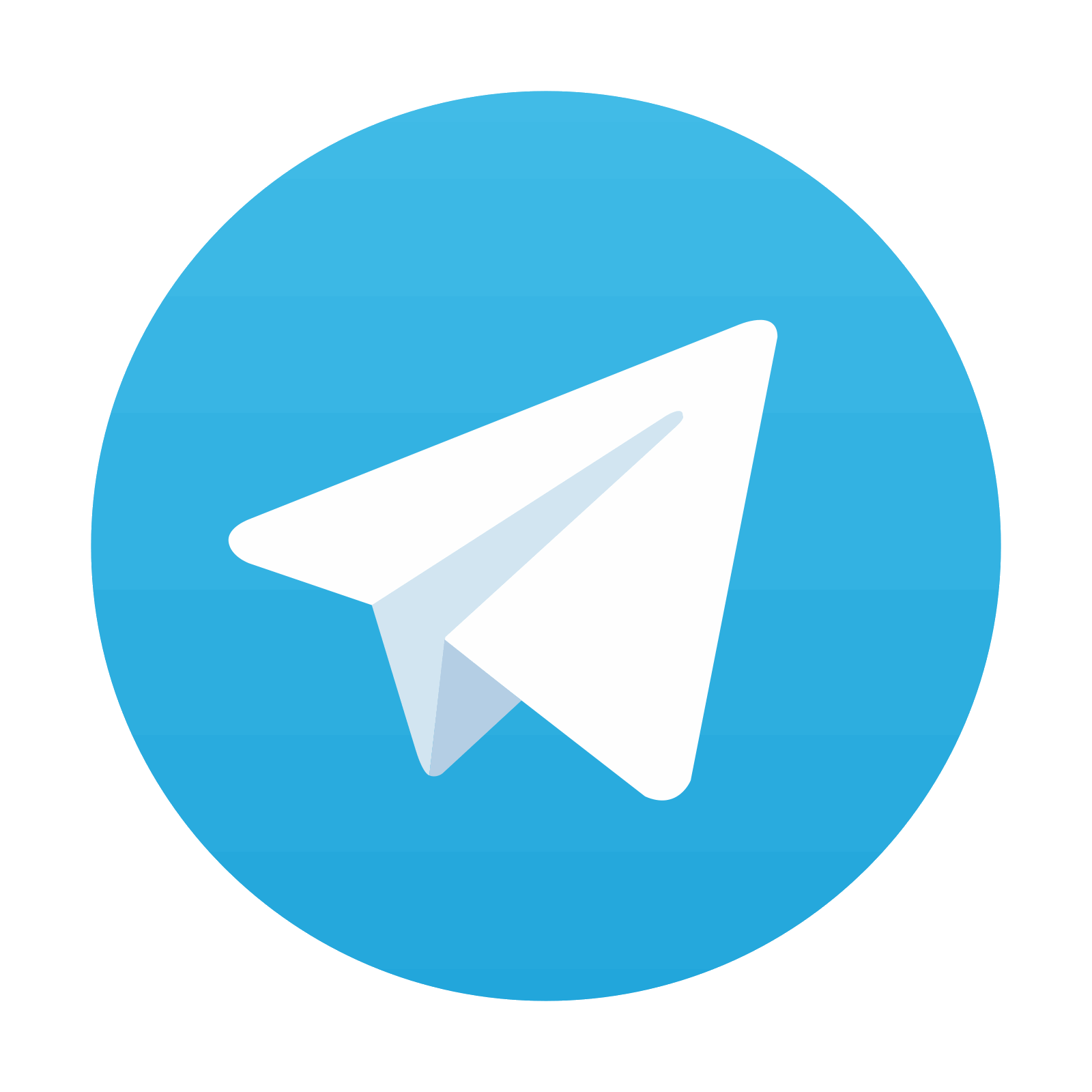
Stay updated, free articles. Join our Telegram channel
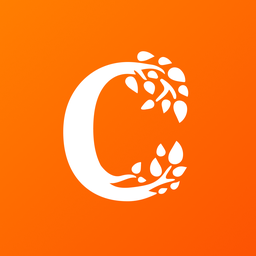
Full access? Get Clinical Tree
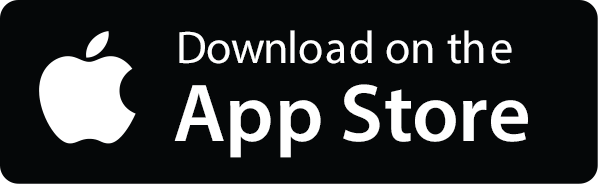
