2 Mechanical Properties of Solid Materials
The mechanical, electrical, magnetic, optical, or chemical properties of materials are determined in standardized experiments. The protocols of such experiments and the description of the material properties are always designed so that the dimensions of the samples under investigation do not influence the result. In other words, the experimentally determined parameters describe the materials as such: for example, the properties of the material steel or the material polyethylene, or bone. The properties of structures fabricated from a material—for example, the mechanical properties of a frame made of steel beams, or those of an orthosis or a femoral bone consisting of cortical and trabecular bone—must be determined in separate experiments. Obviously, the mechanical properties of a steel frame depend on the material properties of steel, but they also depend on the dimensions and joints of the beams.
A material is termed homogeneous if its matter is uniformly distributed over its whole volume. Every small volume element of a homogeneous material possesses identical material properties. By contrast, a sample of a material with irregular holes or with other materials or impurities included is described as inhomogeneous. A material is termed isotropic if its internal structure and/or its elastic properties show no preferred directions. Examples of isotropic materials are rubber or cast iron. Wood and bone, by contrast, are termed anisotropic due to the internal alignment of fibers in preferred directions. Semifinished products made of metals or plastics may be anisotropic if they have been pressed or pulled during the production process. The material properties of an anisotropic material depend on the orientation in which the sample was cut, while those of an inhomogeneous material depend on the location from which the sample was cut from a larger block of the material. The material properties of a sample of cortical bone, for example, will depend on the site on the bone from where the sample has been cut. In addition, samples cut longitudinally from a long bone will also exhibit different properties from samples cut transversely from the same bone. Trabecular bone is inhomogeneous because of the voids between the beams and plates, and because the trabeculae align in preferred directions it is (usually) anisotropic as well.
Materials are characterized not by a single parameter but rather by a set of parameters that describe their behavior in different applications and environments. In orthopedic biomechanics, the most important parameters are those describing deformation, failure, friction, and abrasion.
2.1 Elongation and Compression
In a tensile test, a beam-shaped sample of a material is subjected to a tensile force F ( Fig. 2.1 ). In this test, the change dL in the length of the sample is measured in relation to the tensile force. To ensure that the material property to be determined does not depend on the dimensions (cross-sectional area A, length L) of the sample tested, it is not the length change dL in relation to the force F that is reported, but rather the strain in relation to the mechanical stress ( Fig. 2.2 ). The stress σ is defined as the magnitude of the force F divided by the cross-sectional area A of the sample.



Mechanical stress (or, simply, stress) has the dimension (is measured in) newtons per square meter [N/m2] or pascals [Pa]. The strain ε is defined as the length change dL divided by the initial length L.

As the quotient of two lengths, strain is a dimensionless quantity. For clarity, however, the dimension of strain is sometimes quoted as [mm/mm] or [μm/μm].
In qualitative terms, many materials exhibit similar behavior in a tensile test. Under low values of stress, the strain increases in proportion to the stress. In the region of low stress, the dependence of the stress on the strain can be described by a straight line ( Fig. 2.2 ). Above a certain stress value characteristic of the material, the stress–strain graph deviates from a straight line. The quotient of stress and strain in the linear portion of the graph (that is, the slope of the graph in this region) is called the modulus of elasticity or Young’s modulus. The modulus of elasticity is stated in [N/mm2] or [Pa].
In the linear part of the stress–strain graph, Hooke’s law is valid.

Hooke’s law states that the stress is proportional to the strain. A steep slope of the stress–strain graph indicates that a high stress is necessary to effect a specified strain. The modulus of elasticity of such a material has a high numerical value. A shallow slope of the stress–strain graph indicates that a low stress is sufficient to effect a specified strain. The modulus of elasticity of such a material has a low numerical value. In everyday language, materials with a high modulus of elasticity are termed hard and those with a low one, soft.
To avoid quoting large numbers, the moduli are usually quoted in units of N/mm2, not in units of N/m2. Table 2.1 lists the moduli of elasticity of technical materials that are frequently used in the construction of implants together with, for comparison, the moduli of cortical and trabecular bone. The numbers in Table 2.1 show that, compared with metals, cortical bone and polyethylene are soft and trabecular bone is very soft. The numerical values in Table 2.1 are only approximate, because the precise value of the modulus of elasticity depends for metals on the details of the production process, for polyethylene on the degree of polymerization, and for cortical and trabecular bone on the location, the orientation, and the bone density of the sample tested.
Material | Modulus of elasticity E [N/mm2] |
Stainless steel | 2 · 105 |
Titanium alloy | 1 · 105 |
Polyethylene | 1 · 103 |
Cortical bone | 18 · 103 |
Trabecular bone | 90 |
In a tensile test it is not only a change in the length of a sample that is observed, but also a decrease in the diameter, of magnitude |dW| ( Fig. 2.1 ). The quotient of the strains in longitudinal and transverse directions

is a parameter characteristic for every material and is termed Poisson’s ratio. Poisson’s ratio typically has values between 0.2 and 0.5.
Some materials, for example soft tissues, exhibit in a tensile test a comparatively large increase in their strain under low values of stress before a region is reached where the stress increases (approximately) in proportion to the strain. If there is a further increase in the stress, a disproportionate increase of the strain may again be observed ( Fig. 2.3 ). In such cases the slope of the stress–strain curve and thus the modulus of elasticity depend on the strain. For this reason, if a modulus of elasticity is quoted, the strain value at which the modulus was measured must be specified. For a guide value, the modulus of elasticity derived from the approximately linear portion of the stress–strain curve may be quoted.

Rather than being subjected to a tensile force, a material sample may be subjected to a compressive force and the compressive strain dL/L may be plotted in relation to the compressive stress. In such a test it must, however, be ensured that the sample will not bend under the influence of the compressive force. A change in length caused by bending (and not by pure compression) would not allow direct comparison with the results of a tensile test. Experiments show that, for many materials in the region of low stress, the dependence of strain on stress in the linear region is virtually identical in tensile and compressive tests. ‘Low’ stress designates stress much lower than the breaking stress of the sample. In this region, then, the modulus of elasticity characterizes the deformation of a material under tensile as well as under compressive stress.
2.2 Shear
If two parallel and opposite forces of magnitude F act on two sides of a cuboid ( Fig. 2.4 ), a shear stressτ) is generated.


A shear stress does not effect a change in length, but rather a change in the shape of the sample. The initially vertical faces of the cuboid are now seen to be tilted. For small angles of tilt it holds that

G is a material constant and is termed the shear modulus. The angle α is measured in radians. It can be shown (the proof is not given here) that the modulus of elasticity E, Poisson’s ratio μ, and the shear modulus G are related.

Thus the deformation of a homogeneous, isotropic material is fully characterized by two of these three material constants.
2.3 Elastic, Viscoelastic, and Plastic Deformation
For some materials, if in a tensile test the stress is first increased and then reduced to zero, the stress–strain curves for increasing and for decreasing stress are observed to be superimposed. After completion of the load cycle, a sample of such a material returns to its initial length. This type of deformation is termed elastic. If the stress is increased above a certain peak value, which is characteristic for each material, the stress–strain curves for increasing and decreasing stress are observed to be no longer superimposed; deviations from elastic behavior will then be seen. The designation of a deformation or a material as “elastic” must thus be supplemented by information on the maximum stress level involved. Most metals, for example, show elastic deformation, provided the maximum stress is not too close to that leading to destruction of the sample.
If tissues of the human body or plastics are subjected to a tensile test, striking deviations from elastic behavior are observed. The stress–strain curve for increasing stress deviates from the curve for decreasing stress; the two curves form a hysteresis loop ( Fig. 2.5 ). At the end of the load cycle (that is, when the load and thus the stress have returned to zero), the sample is not restored to its original length but a strain dε remains. If, over time and without any exposure to an external force, this strain dε recedes to zero, the deformation is termed viscoelastic. If, by contrast, the strain dε remains constant, the deformation is termed plastic. As an example of a plastic deformation, Fig. 2.6 shows the measured stress–strain curves of the material PVC. In this material, the plastic deformation increased with increasing peak stress of the four load cycles applied.

If a sample of a viscoelastic material is held under constant stress, the initial strain ei is observed to increase with time until it reaches a limiting value εl ( Fig. 2.7 ). The increase in strain under constant stress is termed creep. The decrease in strain under zero stress after completion of a load cycle, mentioned above, is the reverse event. If a sample of a viscoelastic material is loaded up to a certain strain, and the strain is subsequently kept constant, it is observed that the stress within the material decreases with time from its initial value σi to a limiting value l ( Fig. 2.8 ). This effect is termed stress relaxation.



If a sample of a viscoelastic or plastic material is cyclically elongated and compressed, the stress–strain curve forms a complete hysteresis loop ( Fig. 2.9 ). In addition to the hysteresis loop, Fig. 2.9 shows the stress–strain curve of the first half of the first loading cycle, which starts at the origin of the graph. It should be noted that, due to the viscoelastic or plastic properties of the material, the strain at zero stress varies within a region dε. The size of this region dε depends on the peak values of the tensile and compressive stress. If the peak values are increased, the viscoelastic or plastic deformation of the material increases and thus the region de increases as well. In other words, the deformation seen at zero stress in cyclic loading tests depends on the mechanical history (that is, the type and magnitude of past loading). Thus, the deformation range dε is not a property of the material, but is dependent on the test conditions.

In 1963, Buehler and coworkers 2 observed a stress–strain dependence very different from other metals for a nickel–titanium alloy. Fig. 2.10 shows this behavior in relation to the behavior of spring steel. Starting from zero stress, the Ni-Ti alloy (nitinol) shows an increase of stress with strain. This is followed by a region of strain where the stress shows virtually no increase. This property is designated superelastic. A considerable number of technical applications, including some in the medical field, make use of this property. For example, a superelastic material can be employed to design springs, the spring force of which is virtually independent of their deformation.

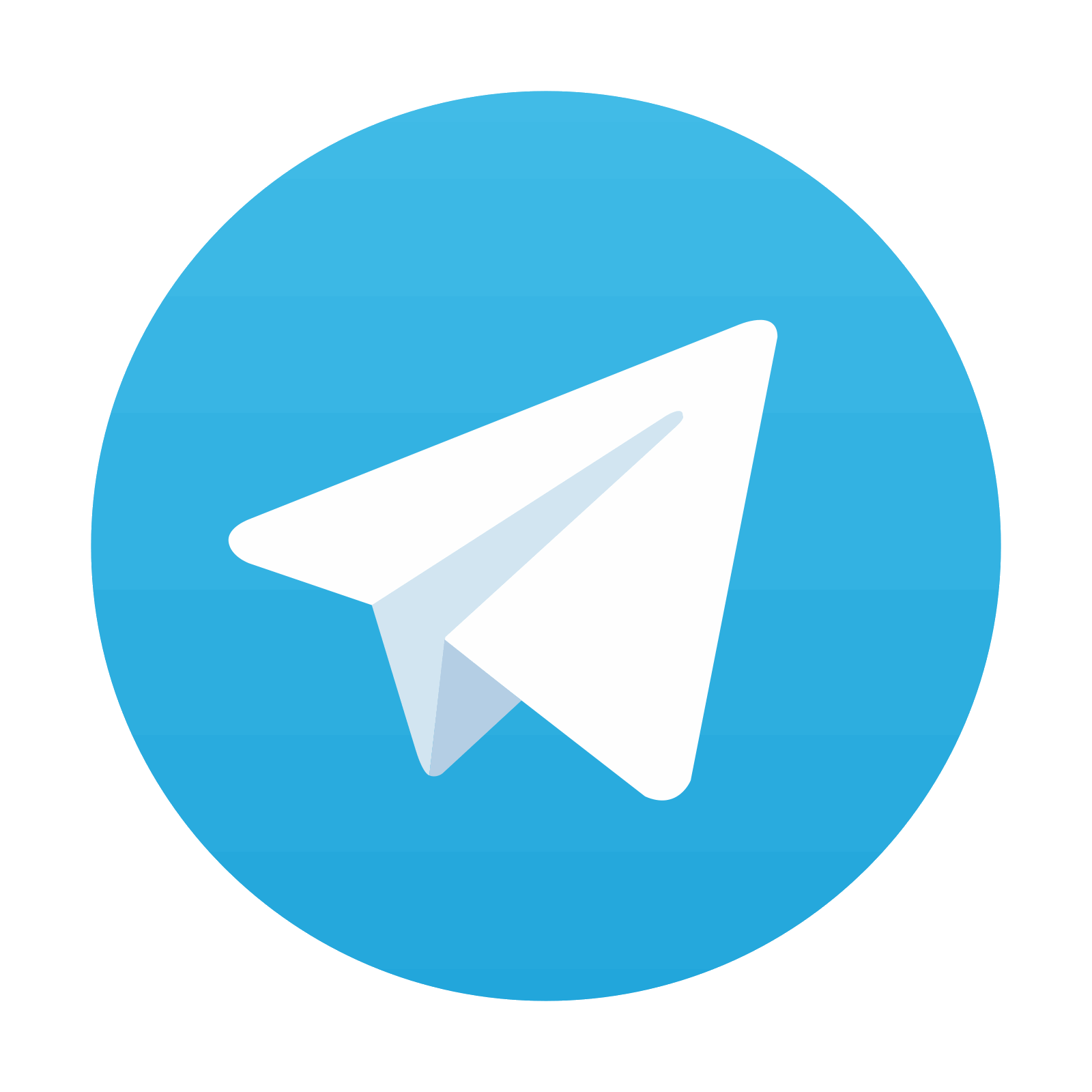
Stay updated, free articles. Join our Telegram channel
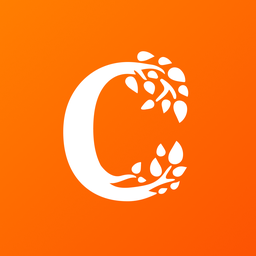
Full access? Get Clinical Tree
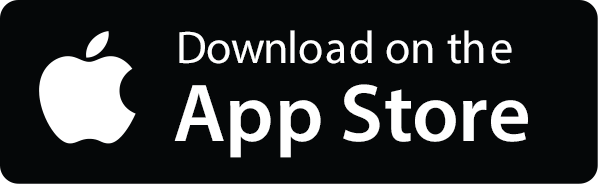
