10 Biomechanics of Fracture Fixation
The basic requirements for successful treatment of bone fractures have long been identified by Lorenz Böhler: reposition, retention, and rehabilitation. The fixation of the fracture has to respect these requirements and has therefore to provide sufficient biomechanical stability. Persistent retention of the fracture requires adequate fixation of the fracture fragments under full or partial load-bearing activities. Therefore, first of all the mechanical characteristics of the fracture fixation technique have to assure the retention of the fracture. Rehabilitation is required to maintain joint mobility but also to introduce some mechanical loading of the fracture. Mechanical loading of the fracture is a prerequisite for a successful healing progress. Certain amounts of motion at the fracture site (inter-fragmentary movements) induce callus formation and stimulate bridging of the fracture gap. Thus, the second requirement of the fracture fixation is to provide sufficient interfragmentary movement to promote healing. Finally, the fracture fixation technique has to transfer the load between the fracture fragments until the fracture has completely united. To endure the healing time without failure or loosening, the fracture fixation device has to have sufficient fatigue strength.
Measuring the biomechanical properties therefore should include assessment of (1) the quality of retention under load, (2) the stability of the osteosynthesis construct described by the stiffness and the interfragmentary movement, and (3) the strength of the osteosynthesis described by load at failure and fatigue strength.
Jargon Simplified: Fracture Fixation Construct
A fracture fixation device (plate, nail, or screw) can be mechanically tested by itself to assess its inherent mechanical performance, which typically includes fatigue testing. However, much more appealing is the mechanical test of the fixation device when it is applied to a fractured bone specimen or to a bone fracture model. The biomechanical testing of such a fracture fixation construct mimics the mechanical performance for a certain fracture situation and will have much more clinical relevance.
10.1 Design of Experiment
In order to appropriately design a biomechanical experiment on fracture fixation constructs (FFCs), it is essential to formulate a testable study hypothesis. The study hypothesis will define the mechanical characteristic that will be assessed and will also specify which type of FFC will be studied. The study conclusion will have to describe the clinical implications of the mechanical performance. Although the aim of most studies is to demonstrate some sort of mechanical superiority, it should be taken into consideration that the mechanical superiority does not necessarily correspond to similar clinical advantages. In the contrary, superior mechanical properties may eventually lead to inferior clinical outcome. 1
10.2 Choice of Load and Load Application
One major challenge in testing of FFCs is the fixation within the frame of the testing machine and the choice of an appropriate loading condition. Ideally, the applied load configuration mimics the physiological load situation as closely as possible. In particular, the direction and contact point of the resulting load vector should simulate the in vivo loading situation. For most of the major joints, the in vivo loading situation are well described, 2 and mechanical testing should consider this expertise. The load frame of the material testing device will have to simulate the resulting load by applying the load to one end of the FFC while the other end is somehow fixed to the machine frame.
Although uniaxial loading is the most frequent form of load application, it may not adequately simulate the in vivo load situation during gait or limb movement. Because it is not a priori known which of the loads occurring in vivo puts the highest challenge on the FFC, several load scenarios or combined load scenarios will have to be realized. The individual load scenario may realize a particular physiological situation or may be just a generic load case (i.e., torsion, shear, bending).
The load application by the testing machine usually simulates a single joint reaction force or the force resultants. Sometimes, it might be necessary to apply additional forces that would be generated from muscles or ligaments in order to simulate physiological loading situations. Such combined loading scenarios can be realized by multiaxial loading devices, lever arm constructs, special pulleys attached to dead weights, or by additional load cylinders (Fig. 10.1).

Fixation of the FFC in the testing frame will always be an approximation of the in vivo loading scenario, but the aim should be to mimic physiological loading as closely as possible. In reality, the fixation in the frame will always be a compromise between providing stable fixation and allowing all necessary degrees of freedom. Ignoring compensatory adjustments can generate very considerable constraining forces and extensive unphysiological load components that may even dominate the overall load. Compensatory adjustments can be realized by using cardanic joints, hinge joints, or linear bearings. This will not only induce defined loading conditions in the FFC but will also spare the load cells of the testing machine from harmful shear forces.
10.3 Testing Conditions
In a biomechanical experiment on an FFC, typically a certain load is applied and the resulting deformation is measured. An important feature is the time characteristic of the loading curve. Loading can be applied “quasi-”statically, dynamically, or cyclically. For the assessment of stability, loading should be applied statically, whereas for the assessment of fatigue strength and retention, cyclic loading should be applied. Dynamic loading can be employed if a sudden catastrophic failure scenario (fall or impact) needs to be simulated.
For “quasi-”static loading, usually several preconditioning cycles (load level less than 10% of failure load) will be performed to avoid settling artifacts and increase reproducibility. The static test itself is performed at relatively slow loading rates reaching the load at failure at around 1 minute. One major direct result from static testing is displacement of the fracture or displacement of the joint surface and deformation of the FFC in specific directions. Stiffness of the FFC is evaluated from the slope of the linear portion of the load-deformation plot with deformation measured in the direction of the applied load (Fig. 10.2). Deformation should be directly measured on the FFC with extensometers, displacement transducers, or optical trackers. If deformation is measured indirectly using the displacement transducer of the testing machine, the stiffness result is biased by the stiffness of the testing frame, testing setup, and intrinsic stiffness of the load cells. The FFC stiffness will be considerably underestimated if stiffness measurement is not accounting for system stiffness. If static loading is continued until failure, the load at failure and the failure energy can also be determined from the load-deformation plot.

Key Concepts: Considering System Stiffness
The compliance of the machine frame, test setup, and load cell can significantly contribute to measured displacement if measurement is performed with the machine transducers.
The correct stiffness of the FFC SFFC can be obtained by correcting the measured total stiffness Stotal by adjusting for intrinsic system stiffness SSystem according to:

The system stiffness SSystem can be determined by replacing the FFC with an extremely stiff dummy device, for example a solid steel cylinder.
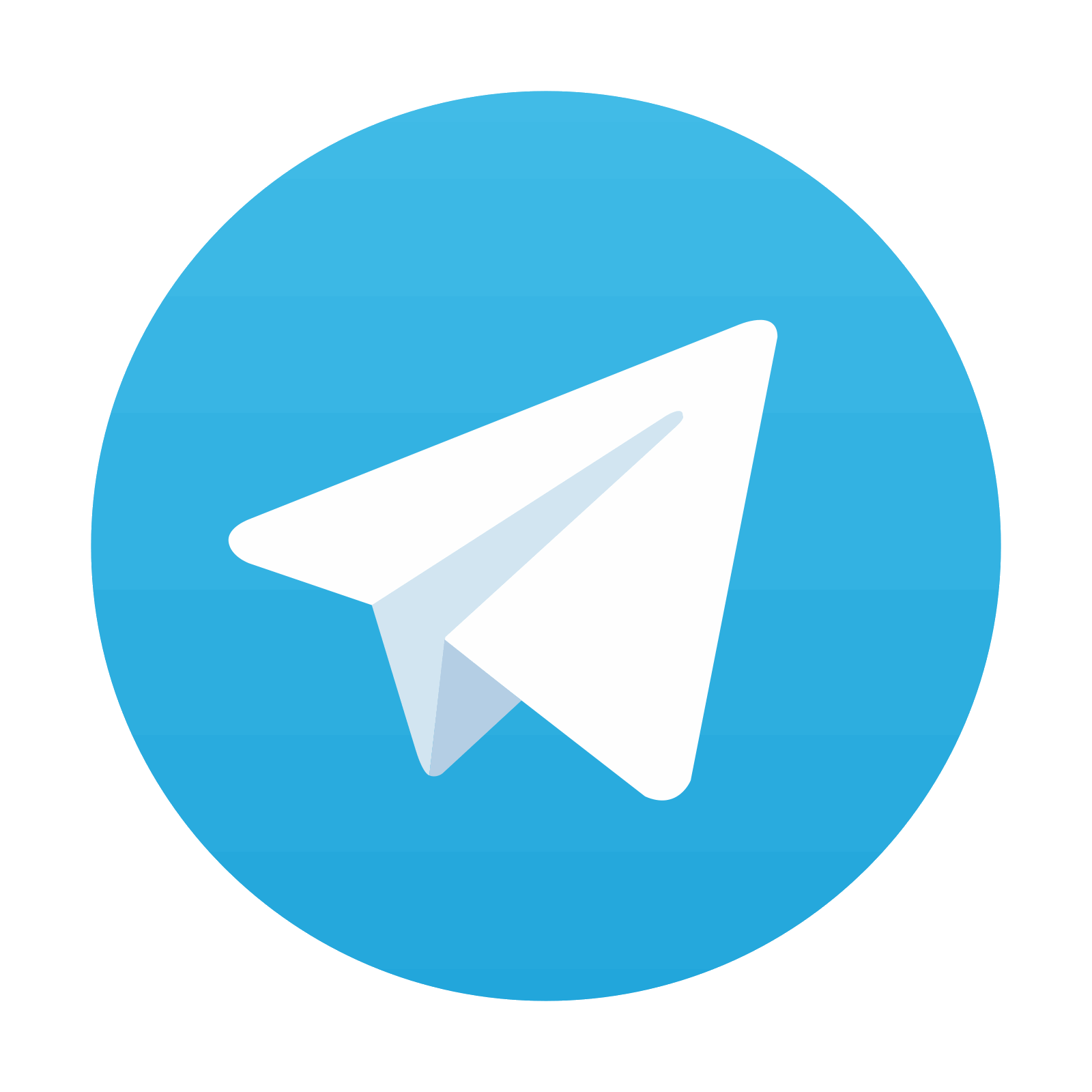
Stay updated, free articles. Join our Telegram channel
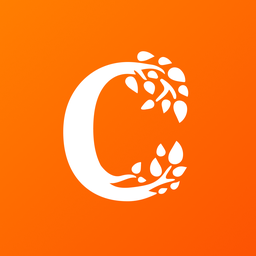
Full access? Get Clinical Tree
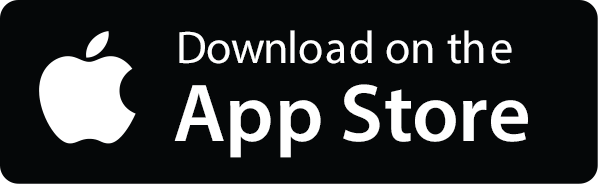

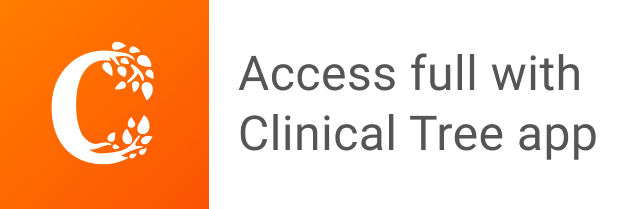