6 Static, Dynamic, and Fatigue Mechanical Testing
Mechanical testing is one of the most reliable and established methods in experimental research. The insight gained when seeing specimens move, bend, break, and in some cases, explode during data acquisition is unmatched in comparison to other available methods (i.e., computer simulation). In addition to handling the metals, plastics, and bone under investigation, the experience of seeing structures under load addresses the professional interest of almost any mechanical engineer or biomechanically interested medical doctor.
This chapter aims to provide an overview of material behavior under different loading conditions as well as an overview of the equipment used for static, impact, and dynamic medical device testing. Theory will be combined with examples derived from real tests showing how typical results are derived from test data. The selection of the tests may be biased and represents only a fraction of the infinite possibilities used in mechanical testing. Whenever the following pages pass on the enthusiasm all experimental researchers share, the intention of this chapter is more than achieved.
6.1 Static Testing
During a static test, loads are typically applied only once rates are at or below 1 Hz. As such, these tests are often referred to as “quasistatic” and are independent of time and inertial effects. The focus of a quasistatic test is to investigate the behavior of a structure under external forces and/or moments while maintaining equilibrium. Static tests are the most common biomechanical experiments used to answer questions about how implants interact with biological structures, as well as to detect “weak points” of complex implant designs. Typically, implants do not fail under a single loading event but rather under fatigue loading conditions. As such, the value of quasistatic testing for performance analysis of in vivo loaded implants is often overestimated; in vivo performance/fatigue analysis is addressed by dynamic testing as described in Chapter 6.3. There are certain considerations that should be kept in mind when designing a quasistatic test such that it yields meaningful results. In particular, test results should be independent of loading history, or all effects related to loading history, such as viscoelastic behavior, should be saturated prior to taking final measurements.
In theory, elastic materials behave like springs, as shown in Fig. 6.1 (left). Given that the yield load is not reached, loading and unloading will follow one straight line. In reality, we see this type of curve only once: in books. There are a number of factors contributing to the initial setting phase and hysteresis of materials, as depicted in Fig. 6.1 (right). The initial deviation from linear behavior is primarily related to fixtures and adaptors required for load application. In other words, small gaps and interface displacements will need a certain load to become closed. Some of the initial setting may also be related to surface effects between the load applicator and the contact area of the specimen. This effect becomes more apparent for porous surfaces (such as cancellous bone) featuring local contact points in comparison to homogeneous contact areas. 1 There are two methods for addressing these issues: One might simply define a pre-load as a starting point for any further calculation, or one might measure displacements directly at the specimen surface. To do so, there are special tools such as extensometers; these can be attached directly to the specimen or can be noncontacting (i.e., video). These methods provide valuable information about the displacement of a complete section of the test setup. Further, whenever the focus of the experiment requires greater detail, strain gauges offer an additional measurement alternative. The nature of strain gauges leads us to another important topic when designing a test: material behavior. The output of a strain gauge is, as the name suggests, “strain.” One might simply calculate stress by multiplying the strain signal by the material′s Young modulus (which is a constant). This approach is sufficient for isotropic and homogeneous materials such as most metal and nonrein-forced plastic, but will become less reliable for biological structures such as bone or tissue, which often have oriented material properties and are composites. As such, great care must be given when performing data analysis of any test series to ensure accurate and meaningful results.

At this point, it becomes important to clearly distinguish between stress/strain as well as load/displacement. Stresses and strains are given for an infinitesimal small cube of material, whereas loads and displacements are the values that apply to the whole construct. To calculate the lengthening of a segment of bone under tensile load, it is necessary to multiply the measured strain by the segment length. Of note, when performing such calculations it is important not to confuse the Young modulus, which indicates the stiffness of the material itself, with the structural stiffness of the entire implant. For example, a bulky hip replacement manufactured from a low modulus material might result in a much stiffer implant in comparison to a thin or hollow implant manufactured from a high modulus material (such as a cobalt chromium alloy).
As indicated earlier, the straight line of the load versus displacement curve will “yield” at a certain load level (Fig. 6.2). This point primarily indicates when plastic deformation of the material occurs; if yield occurs by plastic deformation, the test status changes from nondestructive to destructive. The yield point (E) is determined using an offset line to the load-displacement curve. The offset value (distance between point C and D—see black arrow) is given as a percentage of a reference length, which is often the free length between test fixtures, and is typically 0.2 or 2%. The linear portion of the curve (point A and B) is then defined; this is typically straightforward for some tests but depends largely on the “good judgment” of the test engineer. Linear regression using the least square method is often used to establish a well-defined line. The yield point is thereby easily calculated by the intercept between the offset line (defined by the same slope as the linear portion of the curve offset by the offset distance) and the load versus displacement curve. It is important to note that the determined “yield” point may also result from slippage within the fixtures of the test setup. Moreover, the effect of reaching the yield point is of particular importance if examining a second load cycle, as it will show an even longer straight line as the material properties may be altered by the so-called work hardening process (a process used to increase the hardness and strength of metals).

The following test example summarizes all effects discussed so far. The test standard ASTM F382 defines the test used to characterize the bending properties of bone plates, as seen in Fig. 6.3 left with the expected test results shown in Fig. 6.3 right. At point a shown in Fig. 6.3 (right), the complete test setup is approaching full contact: Roller bearings are (slightly) self-adjusting, adaptors and load cell connectors are closing small gaps, and small surface irregularities are compressed. Point A to point B is the reversible nondestructive portion of the test followed by the yield point (E), which is the “point of no return.” The test operator, for the sake of this example, decided to stop the test at this point and unload the implant for his lunch break. After returning to work, he restarted the test. The second attempt indicates yield at a higher load level (F) than seen before (work hardening has occurred). The test was stopped after the operator started to feel uncomfortable about the large displacement and the fact that the load curve did not show any distinct peak (ultimate) load. This behavior is typical for ductile materials as used for bone plates. Of course, it is important not to use the maximum force measured in this test for any calculations, as these values have affected the decision to stop the test (and the subsequent work hardening affects).

The operator would have seen a well-defined fracture load if testing brittle materials such as ceramics.
Moving toward investigating more complex material behavior, we might produce the bone from a plastic material such as polyetheretherketone. The load displacement curve will now show three additional features: creep, hysteresis, and loading rate dependence. Creep of a material is characterized by continuous displacement under constant load. Creeping, or viscoelastic behavior, is typically logarithmic in nature. The benefit of this is that most of the effect is saturated within a short time such that this can be accounted for by defining a “hold period” in our experiment. The bad news is that the material does have its own memory for loading history, so we will have to wait a certain time (in theory forever) before repeating the test. It is important to keep in mind that viscoelastic behavior is temperature dependent, which should be a controlled parameter for any test. The second effect is hysteresis of the material. In material mechanics, hysteresis is present whenever the unloading curve does not follow the path of the loading curve. This effect was discussed previously (unloading after yield) in the example of the metallic bone plate. By definition, the area enclosed by the loading and unloading curve is the dissipated energy (i.e., heat generation of dynamically loaded structures). This effect is also known as “damping” of the material and is often confused with the structural stiffness of implants. For example, a hip stem designed with a reduced structural stiffness will behave like a soft spring generating more displacement at a given load. In this case, the temperature of the implant will not increase (“damp”) when being cyclically loaded below the yield point. That is, as the implant is considered to behave as a linear-elastic spring, the loading and unloading curve will be identical with no energy being dissipated. As such, damping, which results in dissipated energy, is not analogous to low structural stiffness. The third and last effect is the impact of the loading rate on the load displacement curve. Typically, the higher the loading rate, the stiffer and stronger the material will behave. Again, this effect is temperature dependent.
For the sake of completeness, it should be noted that the area under the force versus displacement curve (integral) represents the total energy to failure.
Finally, when establishing a quasistatic test, correctly defining the degrees of freedom is of paramount importance. In the personal opinion of the author, this is the source of most errors that render a time- and cost-intensive biomechanical test useless. The inexperienced researcher might start with a slightly more time-consuming but straightforward procedure: any rigid body has six degrees of freedom, three translations, and three rotations. The question is: How many of those degrees can be “released” while keeping the test setup valid? The starting point will be to imagine the specimen being rigidly fixated at the base plate of the test frame as well as at the load application (no degrees of freedom released). Beginning with the translations at the point of load application, one might now remove constraints of the setup until it becomes unstable. One might proceed with the rotational constraints at the point of load application and then move to the specimen fixation at the base plate.
Key Concepts: Constraining Forces
Constraining forces prevent translational and rotational motions and must be compared critically to in vivo loading conditions.
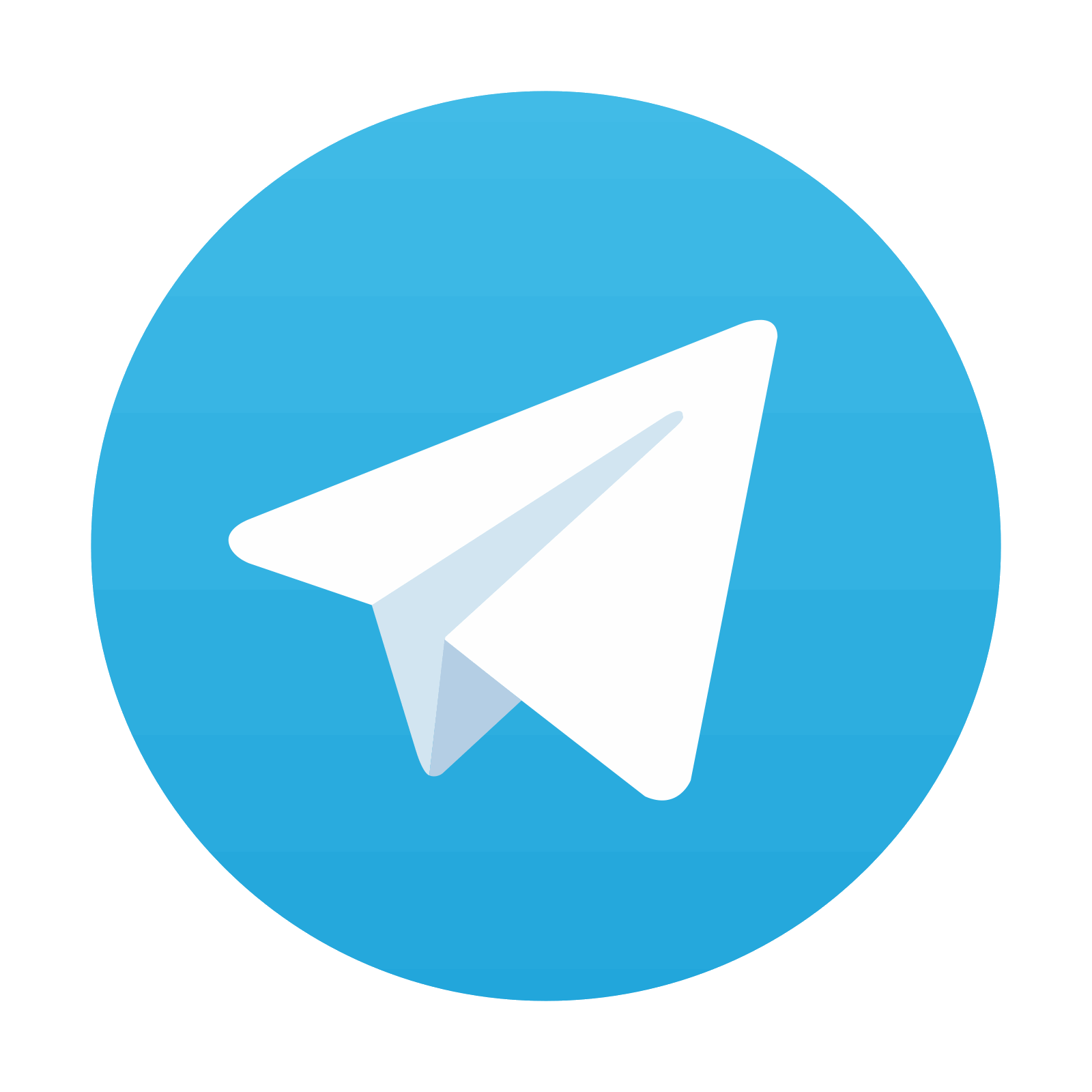
Stay updated, free articles. Join our Telegram channel
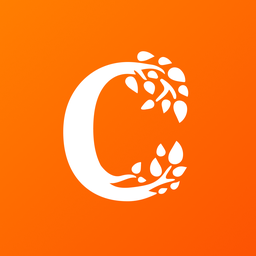
Full access? Get Clinical Tree
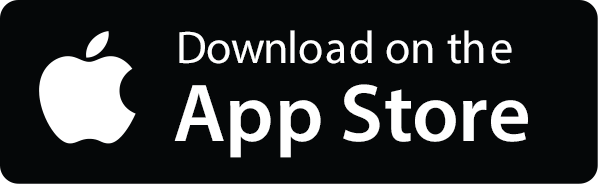

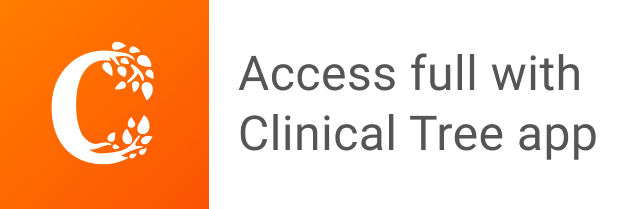