Fig. 18.1
Schematic representation of the volume transformed as a function of the temperature
According to its characteristics, Martensite transformation can be classified into two types-thermoelastic Martensite transformation and non-thermoelastic Martensite transformation. What distinguishes shape memory alloys from conventional materials is their ability to form thermoelastic Martensite. During the process of thermoelastic Martensite transformation, while below the transformation temperature, the deformation of the shape memory alloy is caused by simply adjusting the orientation of the crystal structure through the movement of twin boundaries (a twinning mechanism), instead of slipping and dislocation movement. In other words, the shape change resulting from Martensitic transformation can be accommodated by a crystal lattice distortion, and the boundary between Martensite and the parent phase can be driven by slight changes of the temperature or stress. That is to say, thermoelastic Martensite is completely crystallographically reversible. Whereas on the contrary, the growth rate of the non-thermoelastic Martensite is so quick because of the larger driving force from Martensite transformation that the boundary between Martensite and the parent phase is destroyed during the transformation, which results in an irreversible parent- Martensite boundary.
The Martensite transformation occurs not at a single temperature but within a range of temperatures (as shown in Fig. 18.1), which varies according to different alloy composition and microstructure constitution, the latter being determined mainly by the thermomechanical treatments. Since the phase transformation temperatures during heating and cooling do not overlap, a temperature hysteresis appears, which also varies according to different alloy systems. This temperature hysteresis is generally illustrated as the difference between Af and Ms (i.e., ΔT = Af−Ms) or the difference between Ap and Mp (i.e., ΔT = Ap−Mp).
Functional Properties
Shape Memory Effect
Usually, under external forces, a common metallic material deforms elastically first, then plastic deformation occurs after its yield point, and finally, even if the force is removed, the permanent deformation will be reserved. But for some other alloys, even when a plastic deformation occurs, they can still return to their original shapes after being heated up to a certain temperature. Such a shape recovery phenomenon is called the Shape Memory Effect (SME), which is due to the Martensitic transformation in these alloys. When an alloy with a given shape cools from the Austenite form to the Martensite form, it is easily deformed to a new shape (the restriction is that the deformations must not exceed a certain level), but if the same alloy is heated up to its transformation temperature, it will recover its previous shape due to the reversible reverse transformation.
After being deformed, Martensite can recover its parent shape via reverse transformation. This effect is called the one-way memory effect (Fig. 18.2a). After given proper training, some alloys can memorize to return to not only the parent shape during heating, but also the deformed Martensite shape during re-cooling. This effect is called the two-way memory effect (Fig. 18.2b). The latter can be obtained only after a specific thermomechanical treatment, which is usually called “training”. The amount of shape change that can be obtained by the two-way memory effect is always significantly less than that by the one-way memory effect.


Fig. 18.2
Schematic representation of one-way (a) and two-way (b) memory effects
Generally, the shape memory effect can be expressed by the shape recovery ratio (i.e., η). If the initial shape of the alloy in Austenite form is l0 (expressed as length), the shape of deformed Martensite (e.g., tension) is l1, and the shape after reverse transformation at high temperature is l2, the η can be expressed as [8].


Superelasticity
Superelasticity, as the name implies, refers to a phenomenon that the alloy can exhibit strain far beyond its elastic limit upon loading, whereas once the stress is removed, the original strain will be returned completely. According to the characteristics of the stress–strain curves, the superelasticity can be classified into two types: linear and non-linear superelasticity. The latter is caused by a stress that occurs during a loading and unloading process, which leads to Martensitic transformation and its reverse transformation at a temperature range above Af. The former is probably related to the contribution of microtwins to the deformation. The two kinds of superelastic behavior are shown in Fig. 18.3. As for the non-linear superelasticity, when the stress reaches a critical level, the alloy will start to transform into Martensite, accompanied by an increasing strain at constant stress until the alloy is fully transformed into Martensite (see Segment A–B in Fig. 18.3). When the stress is removed, the reverse transformation will occur at a lower stress level (see Segment C–D in Fig. 18.3). The SME described above depends on temperature changes. In contrast, the superelastic effect of shape memory alloys is a kind of isothermal phenomenon and the temperature changes are not necessary. The critical stresses can be adjusted by alloy composition, treatment and temperature. In general, the stress levels increase linearly with increasing temperatures [6]. Reversible strain obtained by the superelastic effect is always up to 8 %, which is 10–20 times higher than the normal elastic strain of conventional metallic materials. As shown in Fig. 18.3, the stress upon loading and unloading does not overlap and shows a hysteresis as well.


Fig. 18.3
Two kinds of superelastic behavior at constant temperature
High Damping Capacity
The shape memory alloys have a high damping capacity in the Martensite state or two-phase state. The high damping capacity of SMA is related to the hysteretic movement on interfaces (Martensite variants interfaces, twin planes, parent-Martensite interfaces) whereas a contribution of dislocations is not excluded [5].
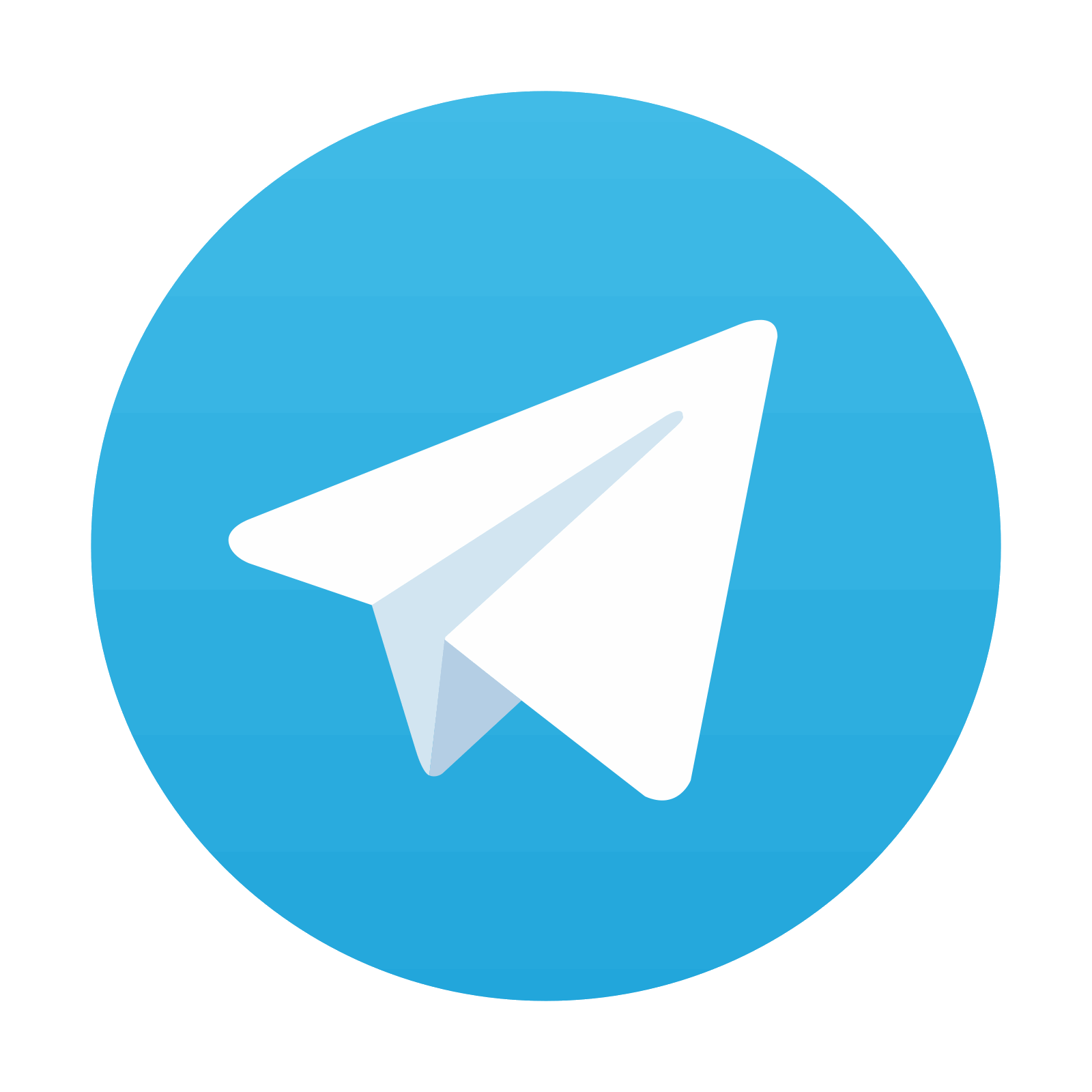
Stay updated, free articles. Join our Telegram channel
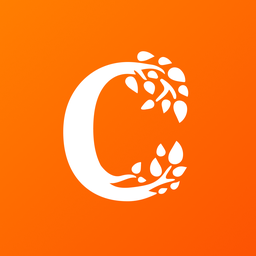
Full access? Get Clinical Tree
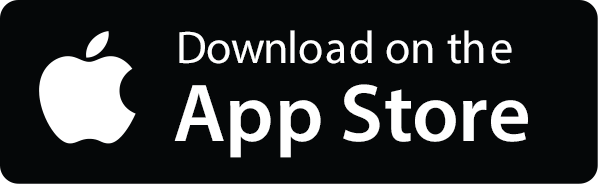
