Technology plays a critical role in promoting well-being, activity, and participation for individuals with spinal cord injury (SCI). As technology has improved, so has the realm of possibilities open to people with SCI. School, work, travel, and leisure activities are all facilitated by technology. Advances in materials have made wheelchairs lighter, and developments in design have made wheelchairs that fit individual needs. Software has made computer interfaces adaptive and in some case intelligent, through learning the user’s behavior and optimizing its structure. As participatory action design and aware systems take greater hold, transformational change is likely to take place in the technology available to people with SCI.
Technology plays a critical role in promoting well-being, activity, and participation for individuals with spinal cord injury (SCI). It is one of the few things that can be provided to people with SCI where one can see an immediate and profound benefit. As technology has improved, so has the realm of possibilities open to people with SCI. The range of activities in which people with SCI participate is impressive and yet still growing. School, work, travel, and leisure activities are all facilitated by technology. Advances in materials have made wheelchairs lighter, and developments in design have made wheelchairs that fit individual needs. Software has made computer interfaces adaptive and in some case intelligent, through learning the user’s behavior and optimizing its structure. The trend is certainly taking us in two exciting directions: (1) personalized design where the technology matches and adapts to the user’s needs; (2) and aware systems that learn from the user’s behavior, the context, and the environment to support the end-user. As participatory action design and aware systems take greater hold, transformational change is likely to take place in the technology available to people with SCI.
Universal design is likely superseded in many areas of assistive technology in favor of adaptive and smart design. The basic premise of universal design is that products, buildings, and entire systems be created that accommodate the maximum possible range of people. This is a noble goal, but it often leads to unsatisfactory results for large sectors of people; although, architecture and city planning are notable exceptions where universal design has been successful and has been a stimulus for creative thinking. Of course, there are other examples as well. Adaptive design is already making inroads, especially in devices and even systems that are programmable. For example an ubiquitous cellular telephone can be adapted in many ways. The cell phone software allows for personalization (eg, ring tone, address book), and limited learning (eg, recording numbers called and received). The appearance of some cell phones can be changed by changing the snap-on plastic cover. Another entirely different approach is used in the eyeglass business that allows people to try various colors of a fixed frame style at no risk; this is feasible because most of the cost is in the lenses, which are transferred between frames. This latter approach can be seen as smart design, where the needs of various customers are anticipated in advance and incorporated into the range of products and options made available. Rapid prototyping and flexible manufacturing are already making their impact on smart design. Rapid prototyping in a classical sense uses computer-aided engineering, design, and manufacturing to make products or components using more or less standard manufacturing processes. This removes much of the human labor and specialized tooling from the product pathways. State-of-the-art rapid prototyping uses constructive processes, such as 3-dimensioal printing, to assemble devices from basic materials. Flexible manufacturing is making change to the way products are designed and manufactured; as factories became more automated to reduce costs and increase flexibility, the concept grew to include making multiple products for different companies within the same factory. Flexible manufacturing allows the machines and product flow to change to meet an individual customer’s needs. Personal computers are an example of flexible manufacturing that most people may be familiar with. Quite readily, one can order a computer through the Internet or via telephone that is manufactured for them from a wide selection of options and features that they choose from. These technological changes are impacting assistive technology and will continue to do so for some time to come.
The team approach
Like other areas of rehabilitation, the delivery of assistive technology (AT) services are best provided using a team approach. The individual with SCI and the family members are critical members of the team, and they should set the goals. Ideally, an AT team would include a physician, therapist, AT supplier, and a rehabilitation engineer. Each has a unique but complementary role, and in cooperation with the end-user provides a comprehensive view of the AT needs. Physiatrists make ideal physicians on AT teams with their residency training and the opportunities that AT provides to benefit people with disabilities. The increasing complexity of AT selection, justification, fitting, tuning, and training requires specialized knowledge. The Rehabilitation Engineering and Assistive Technology Society of North America (RESNA) recognized the need for consumers and insurers to be able to distinguish individuals with relevant experience and specialized knowledge. Over the following 10 years, RESNA created three credentials that each year continue to grow throughout the United States and appears to be slowly becoming a model for several other countries. The Assistive Technology Supplier (ATS) credential is intended for distributors and manufacturer representatives of AT. The ATS is the most important of the credentials offered by RESNA, as it has started to bring order to an area of AT that was largely unregulated. Before the ATS there was no reliable credential for a supplier or manufacturer representative to demonstrate competency and for consumers to readily identify qualified suppliers. The Assistive Technology Provider (ATP) credential is geared toward therapists (physical, occupational, speech/language, counselors, and special educators). The ATP provides recognition for qualified clinicians who wish to be recognized for their specialized knowledge and expertise. For decades, rehabilitation engineers provided clinical services without formal recognition of their expertise and in many cases their services were not reimbursed by some insurance agencies. The Rehabilitation Engineering Technology (RET) credential addresses the needs of rehabilitation engineers and provides other professionals and consumers a clear way to recognize clinical rehabilitation engineers. In order to obtain the RET, the engineer must also have obtained the ATP credential. All of the RESNA credentials require proof of relevant experience and a passing score on a comprehensive examination. It is too early to tell, but the signs indicate that the credentials have improved the quality of services available. Although there remain some significant challenges ahead. It is difficult for comprehensive AT clinics to survive from reimbursement for their services. Therefore, most AT clinics are associated with a university, not-for-profit organization (eg, Easter Seals, United Cerebral Palsy), or a rehabilitation center; whereas other sources can assist in underwriting the costs.
Wheelchairs
There are four basic classes of wheelchair: (a) manual wheelchair, (b) power-assisted wheelchair, (c) electric-powered wheelchair, and (d) robotic wheelchair. We will discuss the benefits, applications, and likely advances for each of these categories. There are a large variety of manual wheelchair makes and models available; however, the ultralight manual wheelchair clearly shines brighter than the others. And even the ultralight wheelchair itself is being redefined as newer materials and design techniques are bringing down the mass and improving ergonomics. Let’s start with the decades old questions: what is more important, weight or fit? The short answer to this question appears simple, both, but a more effective way to determine the answer is to ask a related question. Which wheelchair and features are most functional and will cause the least harm. Weight is certainly important in preventing repetitive strain injuries, for ease of loading in a car, and for making it easier to propel up slopes or curbs. Ergonomics affect all of these properties and in addition affect seated comfort (or prevention of discomfort), propulsion over all terrain, and control over the wheelchair (eg, wheelies). Fortunately, weight and ergonomics often go together because designing a very light (less then 10 kg) manual wheelchair requires both good design and ergonomics. To keep the weight low, designers must carefully choose those features that will be fixed and those that will be adjustable. This also forces the clinician-consumer team to take equal care in selecting the wheelchair. Some options may make the chair slightly heavier such as ergonomic pushrims or solid backrests, but frequently they are worth the weight.
Research tells us that there are several guidelines that can be followed to choose and set up a properly fitting and functioning manual wheelchair. The seat width should be about 25 mm or less wider than the distance between the trochantors while seated. This keeps the chair narrow for negotiating doorways, aisles, and hallways. More importantly, it brings the wheels in so that the shoulders remain in a more neutral position close to the body while propelling. The seat depth should be about 50 mm less then the seated distance between the back and the popliteal area behind the knees. This will allow some repositioning within the seat, and provide a large surface area for the cushion. The seat back height should be such that the person can move freely for activities performed in the chair: eating, reaching, dressing, slouching, sitting, propelling. Too high a back height can be restrictive, and too low can lead to discomfort and reduced trunk stability. The seat height should be such that users while sitting upright in the chair can reach the axles comfortably with their hands extended at their sides. Seat inclination (dump) is more of an individual decision. About 5 degrees is common, but higher angles can help to hold the pelvis against the backrest increasing trunk stability; however, this often makes transfer from the chair more difficult. Positioning of the rear wheels is one of the most critical dimensions. Placing the axles forward of the backrest and nearer to the center of mass of the user and chair together reduces rolling resistance, decreases the downhill turning moment on side slopes, and allows the user to grasp the pushrims over a wide arc. All of these are positive attributes, but one negative result is that the wheelchair becomes less stable in the rearward direction. Therefore, it is wise to have the clinician-consumer team work on wheelie skills and balance to determine the best rear axle position.
When starting to use a wheelchair it is best to select one that provides the ability to adjust many of its seating and wheel positions. Typically people who first have a SCI go through a series of physical and functional changes, and the chair will need to be adjusted as these changes take place. Once the end-users have become more skilled at using a wheelchair and their function has stabilized, a change to a chair with more fixed features is likely warranted. Throughout a person’s life it is important to keep pace with improvements in wheelchair technology, as many times the advances can increase function, reduce discomfort, and protect against injury. Ultralight manual wheelchairs should be recommended for almost all individuals with paraplegia and for individuals with lower tetraplegia, unless there is a secondary condition or diagnosis to suggest otherwise.
The power-assisted wheelchair has become more popular within the past decade because of the availability of the pushrim-activated power-assist wheelchair (PAPAW). The PAPAW uses small motors that react to the torque applied to the pushrims. The motors are powered by a high-density battery (eg, NiMH, NiCd, Lithium). The PAPAW serves two important purposes: (1) it reduces the physical and physiologic strain on the user; and (2) it provides lightweight (about 20 kg) power-assisted mobility and transportability. A PAPAW can be a custom-designed wheelchair or it can be an ultralight manual wheelchair adapted to accept power-assist wheels. Fitting individuals for a PAPAW is much like fitting them for an ultralight manual wheelchair, with two notable exceptions: (1) the axle position should be more rearward for added stability; and (2) the power-assist wheels need to be tuned for the user. Key factors with the electronics of a PAPAW to pay attention to are: can the end-user safely operate at the maximum assisted speed; does the device provide adequate braking assistance and control on slopes; is the chair easy to maneuver in close quarters. A PAPAW is effectively a heavy manual wheelchair if the batteries lose their charge; therefore, regular charging is important.
There has been a virtual explosion in electric-powered wheelchair (EPW) designs. This has provided people with many more choices, but not all of them are appropriate for people with SCI. The taxonomy of EPW can be described based on function, drive wheel position, intended environment, and seating functions. A number of EPWs really do not need to be considered for people with SCI. Our goal should be to maximize functional mobility within the home and community at large. Therefore, activity duty EPWs are most appropriate. Although controversial, there is growing evidence to support the recommendation of powered seating functions for individuals with SCI. Powered seat elevation may be the most helpful to aide in transfers either assisted or unassisted. Seat height is also critical for extending the functional work space. Powered tilt and/or powered recline are also very important seating functions. Tilt and recline facilitates weight shift to increase comfort, reduce risk of soft tissue breakdown, decrease discomfort, and improve circulation in the lower extremities. The controversy stems basically from cost; powered seat functions increase the cost of the EPW, and therefore some will argue that they are unnecessary if the individual can perform an independent weight shift or transfer. The flaw in this logic is that performing an independent weight shift or transfer or even a few is not enough to determine what a person’s abilities and risks are in their home and community. The needs of people change from day to day and week to week; powered seating functions allow the end-user to adapt to these changes.
The location of the drive wheels of an EPW affect the driving behavior. Rear-wheel-drive EPWs hold their direction the best when rolling forward down a path. When steering, they turn about a point behind the driver, requiring the person to plan when turning into a doorway, for example. They were most popular before digital controls, although are still popular today. Mid-wheel-drive EPWs place the powered wheels near the center of mass of the user. This provides for turning about the center of the chair, which makes them maneuverable and easier for most end-users to judge turns. Mid-wheel-drive EPWs require six wheels, two front outriggers and two rear outriggers to remain stable. Setting the tension on the outrigger suspension is important to provide mobility and control; too soft and the chair rocks, and too hard and the chair cannot climb obstacles. Front-wheel-drive EPWs are popular among some individuals for their obstacle climbing ability. By having the powered wheels encounter the obstacle first, they can often climb over them. When turning a front-wheel-drive EPW, the rear end sweeps, which requires the driver to plan where it will move through the turn.
The controls of EPWs have been gradually improving, but have a long way toward achieving their full potential. Most EPWs allow for adjusting the maximum speed, rate of turning, and braking distance, which have made it possible to accommodate a larger population of end-users. Some systems allow for filter adjustments to compensate for tremor. The use of advanced control algorithms, such as robust control, has yet to be widely applied. A significant barrier to the use of advanced controls is that most wheelchair controllers come from only a few sources, and that EPWs are essentially assembled with existing commercial controllers. This barrier may be partially reduced through open-source software that manufacturers could ask controller suppliers to adopt so as to improve their products.
The operation of an EPW requires an effective and reliable user interface. The most common user interface is the motion joystick, which produces a speed and direction signal proportional to the position of the stick. Signal processing can be used to condition the joystick output to make it easier to control the EPW. Essentially, any reliable and sufficiently rapid source of information can be used to create a user interface. Switches (eg, hand, head, or tongue), gyroscopes and accelerometers (eg, head position), pressure sensors (eg, sip and puff), and isometric joysticks (a.k.a. force-sensing joysticks) are all used to control EPWs. The greatest challenges are in selecting the most effective user interface and tuning it to the user. Selection is typically based on a process of elimination starting with continuous interfaces (eg, joystick) and if necessary transitioning to switch control. The ability to produce continuous input signals most often results in more rapid and smoother control over the EPW. Switch control usually results in slower control dictated by a series of discrete commands. Research and development is active in creating more effective signal-processing algorithms and eventually aware algorithms to intuit the user’s intent and generate control signals.
Driving an EPW is not a simple activity; it requires judgment, vigilance, and adequate vision to effectively navigate in a community environment. When driving down a street, the driver must pay attention to pedestrians, look out for obstacles or cracks in the sidewalk, and align the chair with the curb-cut when crossing the street, as well as watch for traffic. Imagine trying to talk to a friend, talking on the phone, or carrying something on your lap during the circumstances described in the preceding sentence. Robotic mobility systems may offer a solution. Advances in robotics suggest that it may be possible to create mobility devices that are more aware of the environment and that can work in partnership with the user. For example, a fully robotic device could potentially transport an individual from one location to another simply by indicating the desired destination. One could envision current EPWs as the other end of a spectrum that would transverse through reliance solely on commands generated continuously by the driver and commands automatically generated by the robotic device based on broad commands provided by the user. Work is in progress toward the creation of robotic mobility devices. Presently the focal point is obstacle detection, obstacle avoidance, and route navigation. Currently, none of these mobility devices have become commercially available, primarily because they are not yet reliable enough to use in real-world situations. Thus far only simple stationary obstacles, commonly cardboard boxes, can be reliably detected. Advances in imaging processing, image tracking, multisensor integration, and aware systems need to be made before practical robotic mobility devices will be available; however, their deployment could be transformational. There has been limited commercial success in robotic mobility devices with such devices like the IBOT4000 that uses robotics technology to provide unprecedented mobility. The IBOT4000 demonstrates that a multilink design rather than a chassis (like classical EPW) allows the structure to change form to match the desired driving task. For examples, in standard function the links connecting the wheel clusters, base, and seat are at acute angles with respect to one another, whereas in standing function that links open to obtuse angles with respect to one another resulting in an extended height. Furthermore, the IBOT4000 detects the center of mass of the payload (user plus items being carried) and adjusts its response.
There is one unbreakable principle when selecting or recommending a wheelchair and that is to never recommend any wheelchair that has not been tested to and found to be in compliance with the RESNA or International Standards Organization (ISO) standards. The RESNA and ISO standards are intended to ensure minimal quality. Best results are often obtained through independent testing conducted within a reputable testing laboratory.
Wheelchairs
There are four basic classes of wheelchair: (a) manual wheelchair, (b) power-assisted wheelchair, (c) electric-powered wheelchair, and (d) robotic wheelchair. We will discuss the benefits, applications, and likely advances for each of these categories. There are a large variety of manual wheelchair makes and models available; however, the ultralight manual wheelchair clearly shines brighter than the others. And even the ultralight wheelchair itself is being redefined as newer materials and design techniques are bringing down the mass and improving ergonomics. Let’s start with the decades old questions: what is more important, weight or fit? The short answer to this question appears simple, both, but a more effective way to determine the answer is to ask a related question. Which wheelchair and features are most functional and will cause the least harm. Weight is certainly important in preventing repetitive strain injuries, for ease of loading in a car, and for making it easier to propel up slopes or curbs. Ergonomics affect all of these properties and in addition affect seated comfort (or prevention of discomfort), propulsion over all terrain, and control over the wheelchair (eg, wheelies). Fortunately, weight and ergonomics often go together because designing a very light (less then 10 kg) manual wheelchair requires both good design and ergonomics. To keep the weight low, designers must carefully choose those features that will be fixed and those that will be adjustable. This also forces the clinician-consumer team to take equal care in selecting the wheelchair. Some options may make the chair slightly heavier such as ergonomic pushrims or solid backrests, but frequently they are worth the weight.
Research tells us that there are several guidelines that can be followed to choose and set up a properly fitting and functioning manual wheelchair. The seat width should be about 25 mm or less wider than the distance between the trochantors while seated. This keeps the chair narrow for negotiating doorways, aisles, and hallways. More importantly, it brings the wheels in so that the shoulders remain in a more neutral position close to the body while propelling. The seat depth should be about 50 mm less then the seated distance between the back and the popliteal area behind the knees. This will allow some repositioning within the seat, and provide a large surface area for the cushion. The seat back height should be such that the person can move freely for activities performed in the chair: eating, reaching, dressing, slouching, sitting, propelling. Too high a back height can be restrictive, and too low can lead to discomfort and reduced trunk stability. The seat height should be such that users while sitting upright in the chair can reach the axles comfortably with their hands extended at their sides. Seat inclination (dump) is more of an individual decision. About 5 degrees is common, but higher angles can help to hold the pelvis against the backrest increasing trunk stability; however, this often makes transfer from the chair more difficult. Positioning of the rear wheels is one of the most critical dimensions. Placing the axles forward of the backrest and nearer to the center of mass of the user and chair together reduces rolling resistance, decreases the downhill turning moment on side slopes, and allows the user to grasp the pushrims over a wide arc. All of these are positive attributes, but one negative result is that the wheelchair becomes less stable in the rearward direction. Therefore, it is wise to have the clinician-consumer team work on wheelie skills and balance to determine the best rear axle position.
When starting to use a wheelchair it is best to select one that provides the ability to adjust many of its seating and wheel positions. Typically people who first have a SCI go through a series of physical and functional changes, and the chair will need to be adjusted as these changes take place. Once the end-users have become more skilled at using a wheelchair and their function has stabilized, a change to a chair with more fixed features is likely warranted. Throughout a person’s life it is important to keep pace with improvements in wheelchair technology, as many times the advances can increase function, reduce discomfort, and protect against injury. Ultralight manual wheelchairs should be recommended for almost all individuals with paraplegia and for individuals with lower tetraplegia, unless there is a secondary condition or diagnosis to suggest otherwise.
The power-assisted wheelchair has become more popular within the past decade because of the availability of the pushrim-activated power-assist wheelchair (PAPAW). The PAPAW uses small motors that react to the torque applied to the pushrims. The motors are powered by a high-density battery (eg, NiMH, NiCd, Lithium). The PAPAW serves two important purposes: (1) it reduces the physical and physiologic strain on the user; and (2) it provides lightweight (about 20 kg) power-assisted mobility and transportability. A PAPAW can be a custom-designed wheelchair or it can be an ultralight manual wheelchair adapted to accept power-assist wheels. Fitting individuals for a PAPAW is much like fitting them for an ultralight manual wheelchair, with two notable exceptions: (1) the axle position should be more rearward for added stability; and (2) the power-assist wheels need to be tuned for the user. Key factors with the electronics of a PAPAW to pay attention to are: can the end-user safely operate at the maximum assisted speed; does the device provide adequate braking assistance and control on slopes; is the chair easy to maneuver in close quarters. A PAPAW is effectively a heavy manual wheelchair if the batteries lose their charge; therefore, regular charging is important.
There has been a virtual explosion in electric-powered wheelchair (EPW) designs. This has provided people with many more choices, but not all of them are appropriate for people with SCI. The taxonomy of EPW can be described based on function, drive wheel position, intended environment, and seating functions. A number of EPWs really do not need to be considered for people with SCI. Our goal should be to maximize functional mobility within the home and community at large. Therefore, activity duty EPWs are most appropriate. Although controversial, there is growing evidence to support the recommendation of powered seating functions for individuals with SCI. Powered seat elevation may be the most helpful to aide in transfers either assisted or unassisted. Seat height is also critical for extending the functional work space. Powered tilt and/or powered recline are also very important seating functions. Tilt and recline facilitates weight shift to increase comfort, reduce risk of soft tissue breakdown, decrease discomfort, and improve circulation in the lower extremities. The controversy stems basically from cost; powered seat functions increase the cost of the EPW, and therefore some will argue that they are unnecessary if the individual can perform an independent weight shift or transfer. The flaw in this logic is that performing an independent weight shift or transfer or even a few is not enough to determine what a person’s abilities and risks are in their home and community. The needs of people change from day to day and week to week; powered seating functions allow the end-user to adapt to these changes.
The location of the drive wheels of an EPW affect the driving behavior. Rear-wheel-drive EPWs hold their direction the best when rolling forward down a path. When steering, they turn about a point behind the driver, requiring the person to plan when turning into a doorway, for example. They were most popular before digital controls, although are still popular today. Mid-wheel-drive EPWs place the powered wheels near the center of mass of the user. This provides for turning about the center of the chair, which makes them maneuverable and easier for most end-users to judge turns. Mid-wheel-drive EPWs require six wheels, two front outriggers and two rear outriggers to remain stable. Setting the tension on the outrigger suspension is important to provide mobility and control; too soft and the chair rocks, and too hard and the chair cannot climb obstacles. Front-wheel-drive EPWs are popular among some individuals for their obstacle climbing ability. By having the powered wheels encounter the obstacle first, they can often climb over them. When turning a front-wheel-drive EPW, the rear end sweeps, which requires the driver to plan where it will move through the turn.
The controls of EPWs have been gradually improving, but have a long way toward achieving their full potential. Most EPWs allow for adjusting the maximum speed, rate of turning, and braking distance, which have made it possible to accommodate a larger population of end-users. Some systems allow for filter adjustments to compensate for tremor. The use of advanced control algorithms, such as robust control, has yet to be widely applied. A significant barrier to the use of advanced controls is that most wheelchair controllers come from only a few sources, and that EPWs are essentially assembled with existing commercial controllers. This barrier may be partially reduced through open-source software that manufacturers could ask controller suppliers to adopt so as to improve their products.
The operation of an EPW requires an effective and reliable user interface. The most common user interface is the motion joystick, which produces a speed and direction signal proportional to the position of the stick. Signal processing can be used to condition the joystick output to make it easier to control the EPW. Essentially, any reliable and sufficiently rapid source of information can be used to create a user interface. Switches (eg, hand, head, or tongue), gyroscopes and accelerometers (eg, head position), pressure sensors (eg, sip and puff), and isometric joysticks (a.k.a. force-sensing joysticks) are all used to control EPWs. The greatest challenges are in selecting the most effective user interface and tuning it to the user. Selection is typically based on a process of elimination starting with continuous interfaces (eg, joystick) and if necessary transitioning to switch control. The ability to produce continuous input signals most often results in more rapid and smoother control over the EPW. Switch control usually results in slower control dictated by a series of discrete commands. Research and development is active in creating more effective signal-processing algorithms and eventually aware algorithms to intuit the user’s intent and generate control signals.
Driving an EPW is not a simple activity; it requires judgment, vigilance, and adequate vision to effectively navigate in a community environment. When driving down a street, the driver must pay attention to pedestrians, look out for obstacles or cracks in the sidewalk, and align the chair with the curb-cut when crossing the street, as well as watch for traffic. Imagine trying to talk to a friend, talking on the phone, or carrying something on your lap during the circumstances described in the preceding sentence. Robotic mobility systems may offer a solution. Advances in robotics suggest that it may be possible to create mobility devices that are more aware of the environment and that can work in partnership with the user. For example, a fully robotic device could potentially transport an individual from one location to another simply by indicating the desired destination. One could envision current EPWs as the other end of a spectrum that would transverse through reliance solely on commands generated continuously by the driver and commands automatically generated by the robotic device based on broad commands provided by the user. Work is in progress toward the creation of robotic mobility devices. Presently the focal point is obstacle detection, obstacle avoidance, and route navigation. Currently, none of these mobility devices have become commercially available, primarily because they are not yet reliable enough to use in real-world situations. Thus far only simple stationary obstacles, commonly cardboard boxes, can be reliably detected. Advances in imaging processing, image tracking, multisensor integration, and aware systems need to be made before practical robotic mobility devices will be available; however, their deployment could be transformational. There has been limited commercial success in robotic mobility devices with such devices like the IBOT4000 that uses robotics technology to provide unprecedented mobility. The IBOT4000 demonstrates that a multilink design rather than a chassis (like classical EPW) allows the structure to change form to match the desired driving task. For examples, in standard function the links connecting the wheel clusters, base, and seat are at acute angles with respect to one another, whereas in standing function that links open to obtuse angles with respect to one another resulting in an extended height. Furthermore, the IBOT4000 detects the center of mass of the payload (user plus items being carried) and adjusts its response.
There is one unbreakable principle when selecting or recommending a wheelchair and that is to never recommend any wheelchair that has not been tested to and found to be in compliance with the RESNA or International Standards Organization (ISO) standards. The RESNA and ISO standards are intended to ensure minimal quality. Best results are often obtained through independent testing conducted within a reputable testing laboratory.
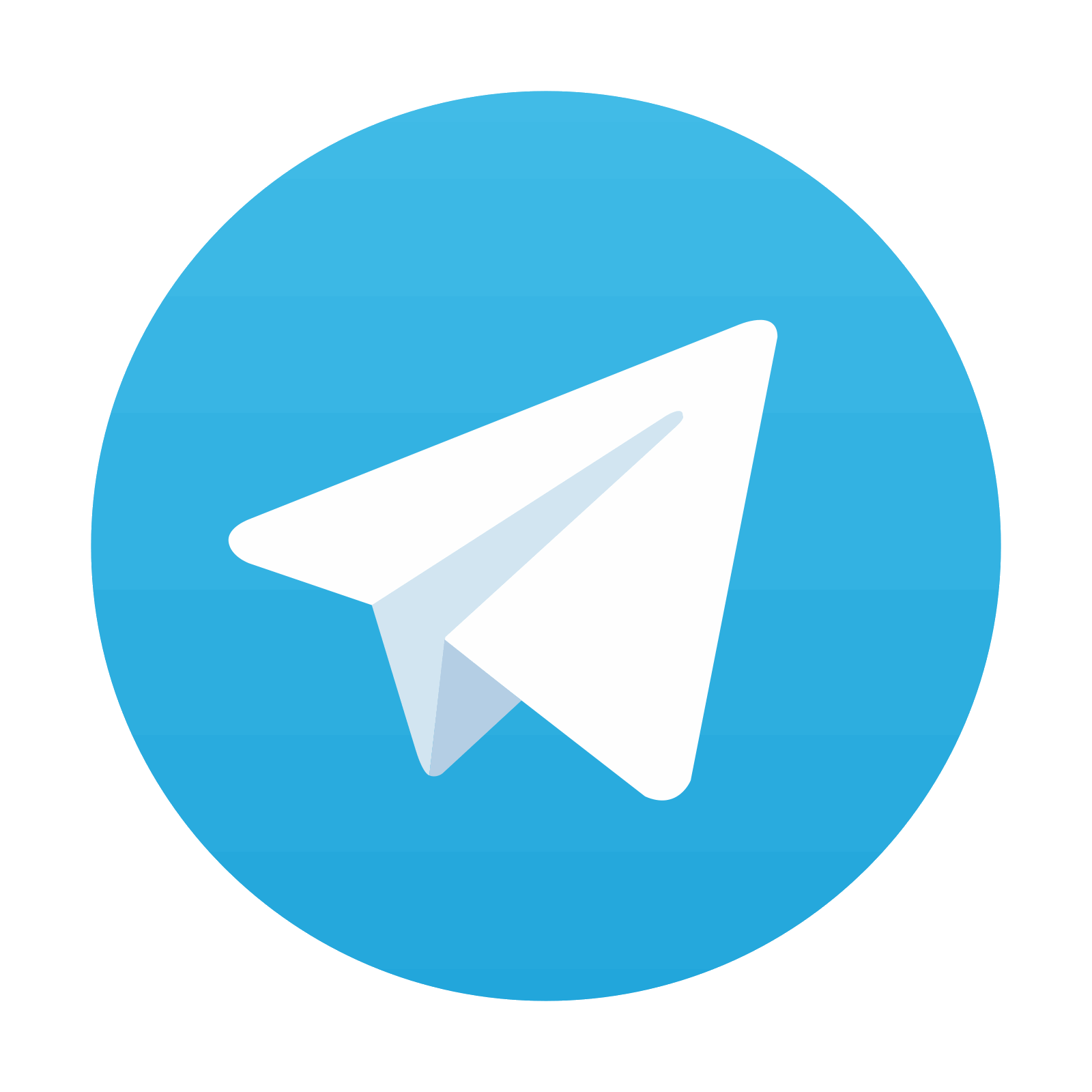
Stay updated, free articles. Join our Telegram channel
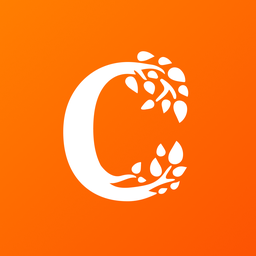
Full access? Get Clinical Tree
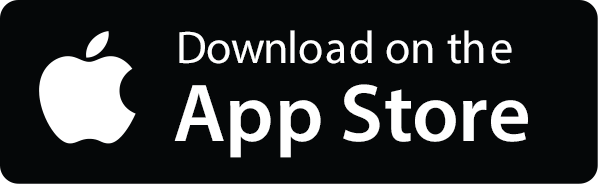
