Fig. 4.1
Steps performed to construct finite element model of the healthy wrist
The ratio of twice the radius of the inscribed circle to the radius of the ascribed circle of the triangle was used as the normalised indicator to determine the mesh quality (Fig. 4.2a) [3]. The value was set at 0.4 to produce a high quality of surface mesh [4]. An assessment made on the model quality based on surface element confirming its reliability where the ratio of twice the radius of the inscribed circle to the radius of the ascribed circle of the triangle for 90 % of elements was greater than 0.80 (where unity represents an equilateral triangle (Fig. 4.2b).
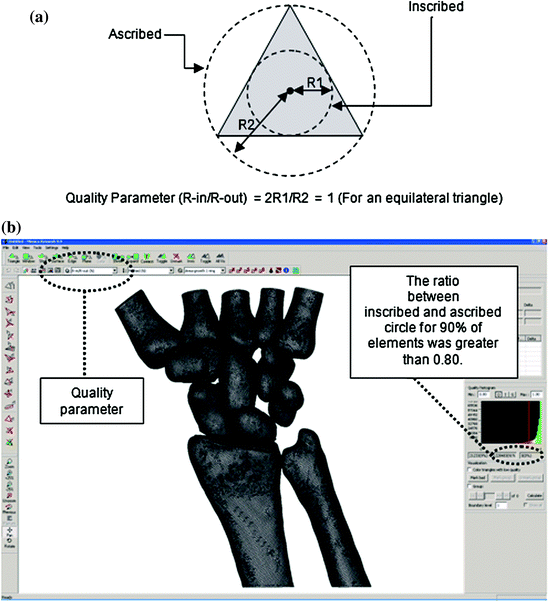
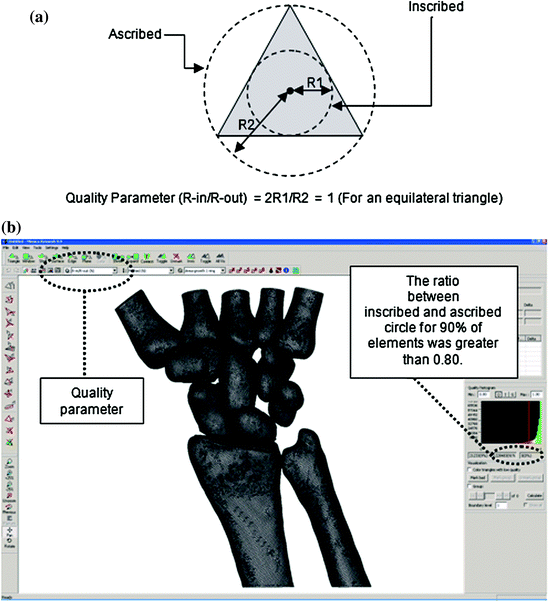
Fig. 4.2
The R-in/R-out as the quality parameter used to determine the quality of mesh (a). The software which indicates the location of the quality parameters (b)
4.2 Modelling of Cartilages
Cartilage layers in the articulations between the solid geometry were modelled by manually identifying the articulating surfaces between bones (Fig. 4.3). To form the cartilage, extracted profiles representing the surfaces of the cartilage distribution were extruded with a thickness size half of the minimum distance between two bones [5], resulted in a good geometrical representation and material distribution of the cartilage (Fig. 4.4). In total, there were 35 cartilages constructed. The distribution of the cartilage was compared and considered acceptable according to an anatomy software [2].
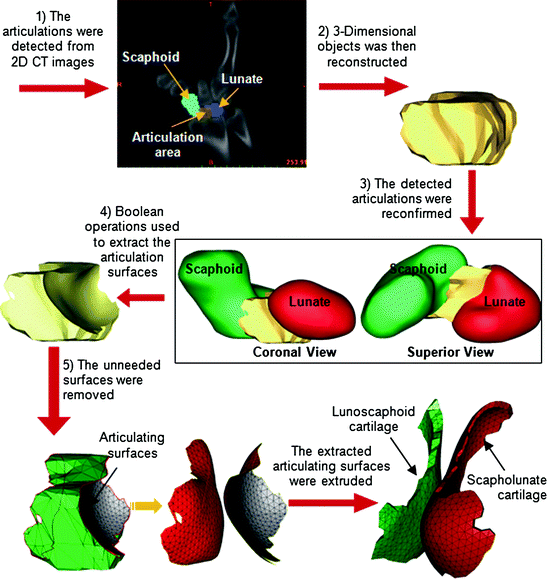
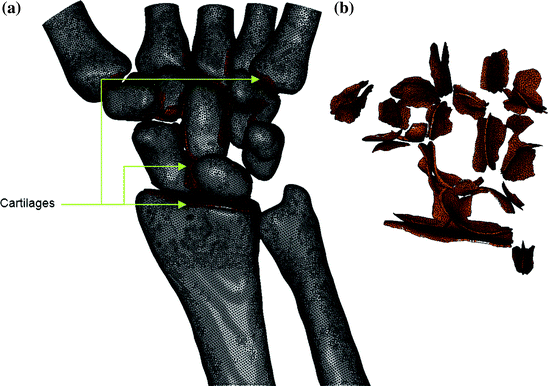
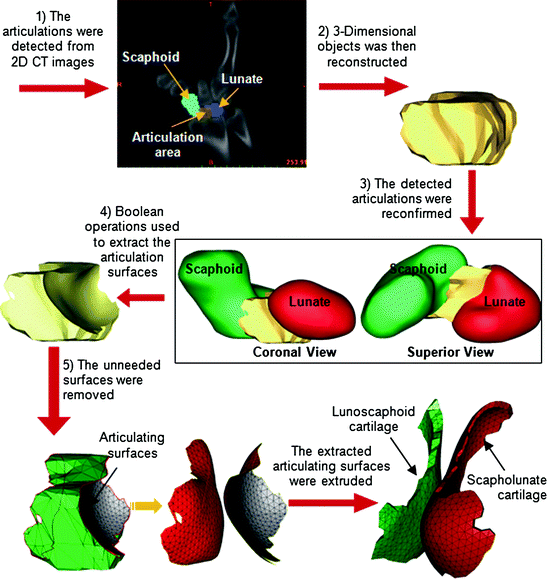
Fig. 4.3
Steps performed to construct finite element model of the cartilage
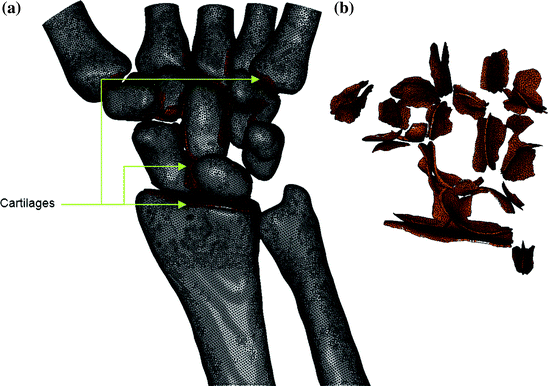
Fig. 4.4
Finite element model of the healthy wrist. The cartilage elements (a) can be seen as the extruded elements at the articulations between bones (b)
4.3 Modelling of Ligaments
All 60 ligamentous constraints as shown in Fig. 4.5 were modelled using linear link elements [6], and the positions of their insertion points were estimated based on previously published anatomical studies [2, 4]. The stiffness of the ligaments varied widely between 40 and 350 N/mm as were reported in previous experimental works (Table 4.1) [5, 7–10]. For ligaments that did not have published material parameters, it was assumed that the properties of the neighbouring ligaments would apply [11]. To simulate distribution of the origin and insertion of the ligaments, parallel multiple links were applied [4, 11].
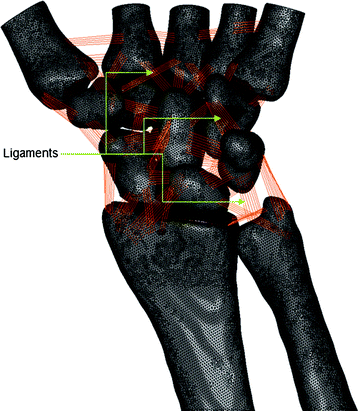
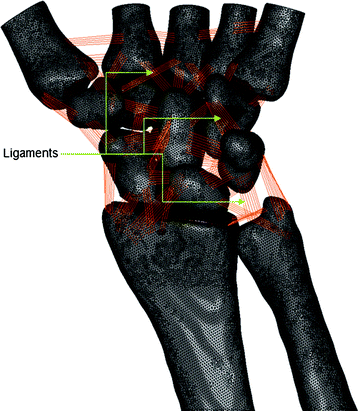
Fig. 4.5
Finite element model of the healthy wrist. The ligaments can be seen as sets of links connecting bones
Table 4.1
Listing of ligaments modelled specifying their connections and defined stiffness parameters
Ligament | Connection 1 | Connection 2 | Stiffness specified (N/mm) |
---|---|---|---|
Capitohamate | Capitate | Hamate | 325 [7] |
Capitotrapezial | Capitate | Trapezium | 300 [7] |
Dorsal carpometacarpal | Capitate | 4MC medial | 300 [12] |
Dorsal carpometacarpal | Capitate | 4MC lateral | 300 [12] |
Dorsal carpometacarpal | Capitate | 3MC medial | 300 [12] |
Dorsal carpometacarpal | Capitate | 3MC lateral | 300 [12] |
Dorsal carpometacarpal | Trapezoid | 2MC lateral | 100 [12] |
Dorsal carpometacarpal | Trapezoid | 2MC medial | 50 [12] |
Dorsal carpometacarpal | Trapezium | 2MC medial | 48 [9] |
Dorsal carpometacarpal | Hamate | 4MC | 300 [12] |
Dorsal carpometacarpal | Hamate | 5MC | 300 [12] |
Dorsal intercarpal | Hamate | Capitate | 325 [7] |
Dorsal intercarpal
![]() Stay updated, free articles. Join our Telegram channel![]() Full access? Get Clinical Tree![]() ![]() ![]() |