Fig. 6.1
The radiographic images of the healthy joint (left) and its replacement (right) for the hip (a), knee (b) and wrist joint (c). It was clearly depicted that for the total hip arthroplasty [12] (a), the affected parts of femur including its head and neck are removed, whereas for total knee replacement [13] (b), only affected surfaces are removed. These two procedures have received great satisfaction from patients and surgeons. However, for total wrist arthroplasty [14] (c), some affected bones are still remained. Even though bone grafts and screws are used to obtain bony support for stability, its effectives were still questionable
6.2 Finite Element Modelling of the Total Wrist Arthroplasty
In this simulation, the latest wrist joint replacement, ReMotion™ produced by Small Bone Innovations, was occupied [11]. CAD software, Solidworks® 2009 was used to model the implant, whereas MARC.MENTAT software used to convert the model into surface triangular elements. Similar to the real surgical procedure, the scaphoid, lunate and some parts of the capitate and triquetrum were resected, and followed by the installation of the implant component to their respective bones. All parts were then converted into solid tetrahedral mesh with 1,305,415 elements and 277,070 nodes. These steps are illustrated in Fig. 6.2.
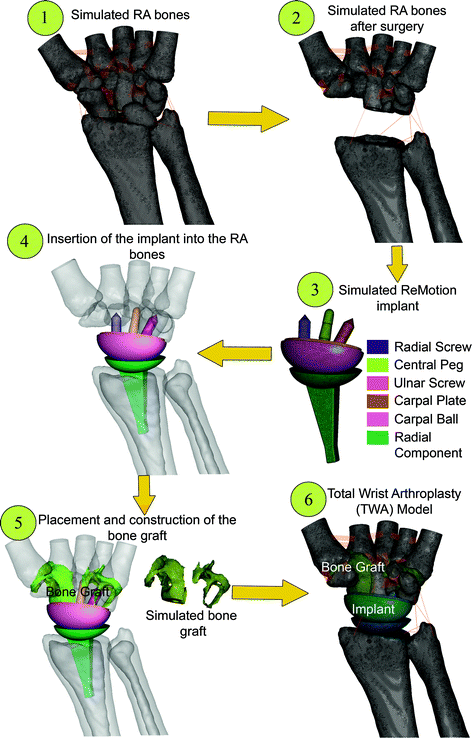
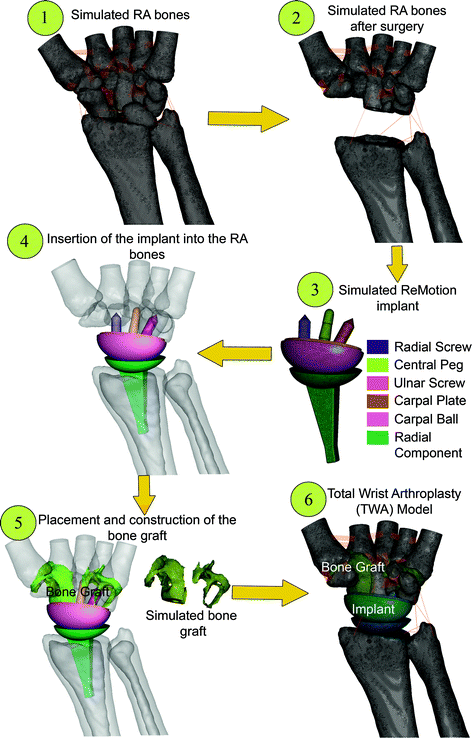
Fig. 6.2
Steps to construct the model of total wrist arthroplasty (TWA)
6.3 Finite Element Analysis: Pre-Processing Procedures
For contact modelling, articulating surfaces were established with deformable-to-deformable contact. Surface roughness at the carpal plate component was set at 0.8 simulating its rough surface to support osseointegration [15]. The effect of screw thread in preventing any slippage at the contacting surfaces was simulated [16]. Physiological movements are allowed for the remaining contacting bodies.
Bones of the wrist in the TWA were modelled as having the same properties as the RA model (the cortical bone; E = 12 GPa, ν = 0.2 and the cancellous bone; E = 33 MPa, ν = 0.25). They were modelled to incorporate linear elastic, isotropic and homogenous properties. Implant components (radius component, carpal plate, central peg and screws) were assigned with properties simulating CoCrMo alloys (E = 210 GPa, ν = 0.3) [17], whereas the carpal ball was assigned with UHMWPE properties (E = 1.4 GPa, ν = 0.3 [18]). The bone graft modulus was varied (E = 0.1, 1 and 5 GPa, ν = 0.2 [19]) to analyse their effects in performing intercarpal fusion. These parameters are summarised in Table 6.1.
Table 6.1
Material properties of the reconstructed 3D models
Materials | Young’s modulus, E (MPa) | Poisson ratio, ν |
---|---|---|
Cortical bone | 12,000 | 0.20 |
Cancellous bone | 33 | 0.25 |
Implant components (CoCrMo) | 210,000 | 0.30 |
Carpal ball (UHMWPE) | 1,400 | 0.30 |
Bone graft | 100 | 0.20 |
1,000 | ||
5,000 |
The load simulating static gripping force of the wrist calculated by Gislason et al. [20] was used. The magnitude of the resultant compression pressure was 7.33 MPa distributed over the five metacarpals, as shown in Table 6.2. All the applied loads and their distributions are presented in Fig. 6.3.
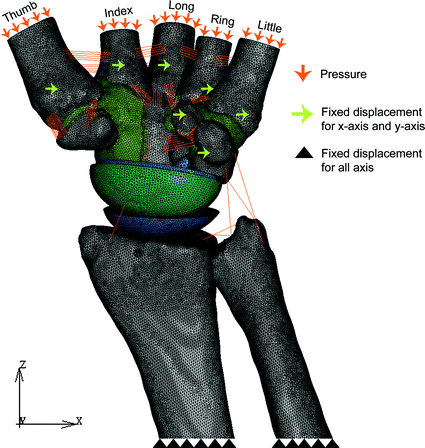
Table 6.2
Relative loading on the metacarpal bones
Thumb | Index | Long | Ring | Little | |
---|---|---|---|---|---|
Cross-sectional area (mm2) | 126.30 | 77.00 | 84.15 | 57.60 | 80.20 |
Load (N) | 255.60 | 120.30 | 106.40 | 88.00 | 77.30 |
Pressure (MPa) | 2.02 | 1.56 | 1.26 | 1.53 | 0.96 |
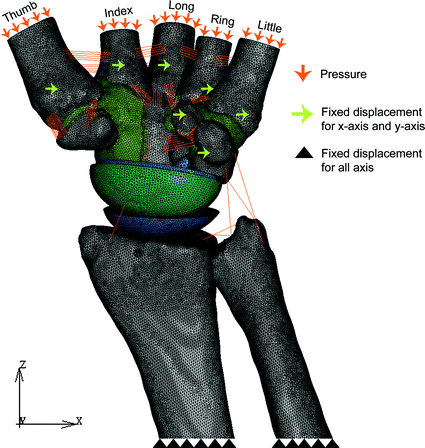
Fig. 6.3
Applied boundary condition simulating static hand grip action
The proximal ends of the radius and ulna were fully constrained to assist convergence of the solution [21]. Additional constraints were occupied by fixing the carpometacarpal joint and the insertions of tendons (abductor pollicis longus muscle, flexor carpi radialis muscle, flexor carpi ulnaris muscle, extensor carpi ulnaris muscle, extensor carpi radialis brevis muscle, extensor carpi radialis longus muscle). All the components (excluding the radius and the ulna) were only allowed to move at the z direction similar to the direction of the applied loading [22].
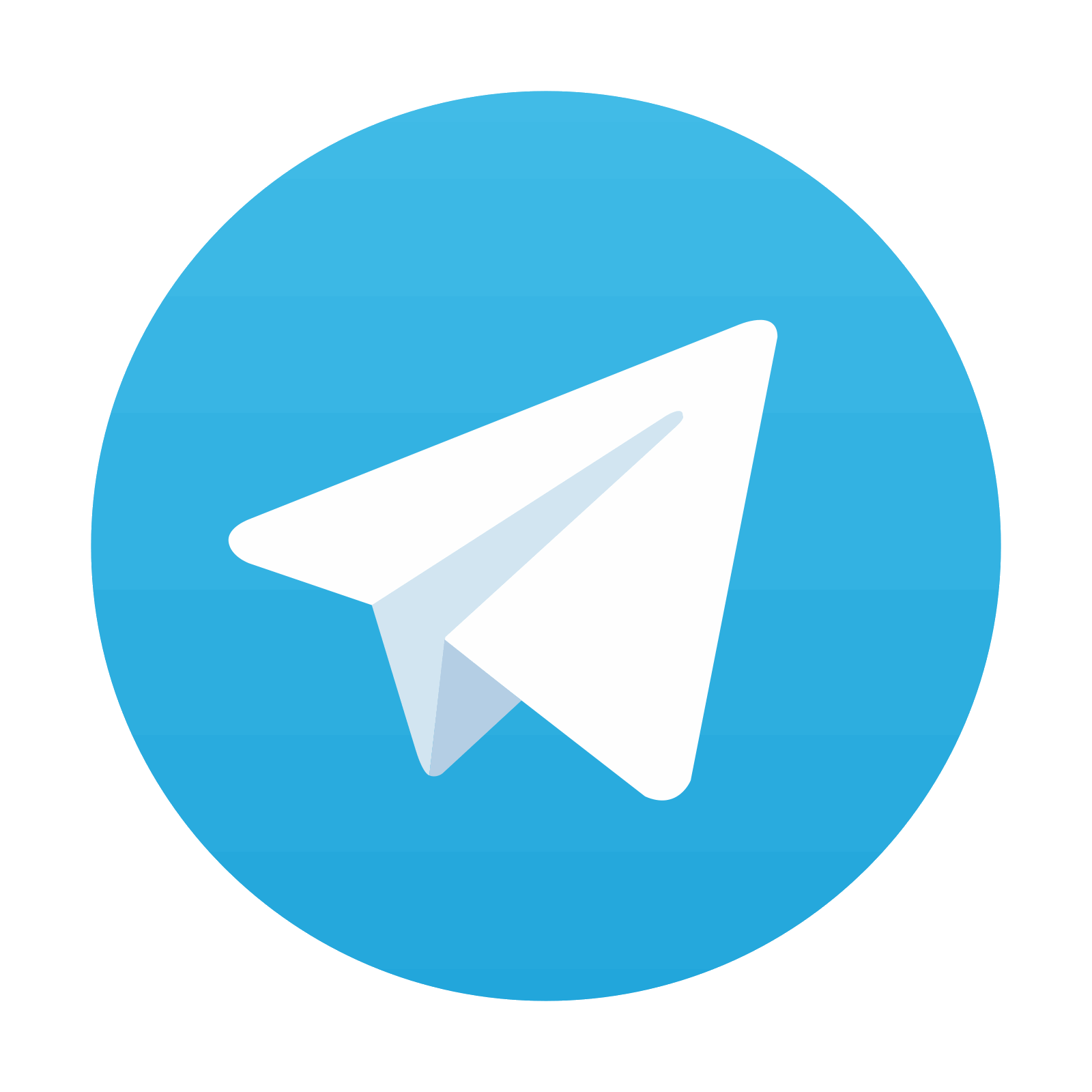
Stay updated, free articles. Join our Telegram channel
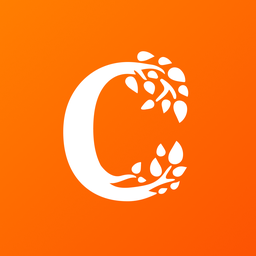
Full access? Get Clinical Tree
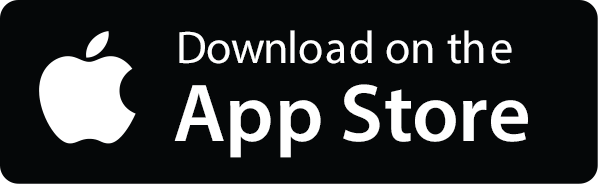
