This article reviews the history of the development of highly cross-linked polyethylene and provides an in-depth review of the clinical results regarding the durability of highly cross-linked polyethylene (HXLPE) used in total hip arthroplasty (THA) and total knee arthroplasty (TKA). The use of polyethylene as a bearing surface has contributed to the success of THA and TKA; however, polyethylene wear and osteolysis can lead to failure. Ongoing clinical and retrieval studies are required to analyze outcomes at longer-term follow-up.
Key points
- •
The durability of modern highly cross-linked polyethylene in total hip arthroplasty and total knee arthroplasty has been excellent.
- •
The manufacturing process leads to free radical generation, which leads to oxidation and reduced mechanical properties.
- •
Postprocessing modifications such as remelting and vitamin E doping reduce the risk of oxidation.
- •
Ten-year wear and survival data for highly cross-linked polyethylene continue to be favorable, but the long-term durability has not yet been demonstrated in vivo.
Introduction
Total hip arthroplasty (THA) and total knee arthroplasty (TKA) have excellent track records with regards to pain relief and improvement of function. Over the past several decades, there have been significant improvements in the engineering and materials science of bearing surfaces. The use of highly cross-linked polyethylene (HXLPE) in large-joint arthroplasty has led to improved outcomes, particularly for THA. This article briefly reviews the history of the development of HXLPE and provides an in-depth review of the clinical results regarding the durability of HXLPE in THA and TKA.
Sir John Charnley attempted to develop a low-friction arthroplasty with the use of Teflon-bearing surfaces. The wear characteristics of this material were unsatisfactory with dramatic early failure from wear. He eventually transitioned to metal-on-polyethylene THA. Charnley’s recognition that polyethylene was a good bearing surface revolutionized hip arthroplasty.
The use of polyethylene as a bearing surface contributed to the success of THA and TKA; however, it was not without complications. Ultra-high-molecular-weight polyethylene (UHMWPE) wear can lead to a local reaction that results in bone resorption or osteolysis. Fig. 1 demonstrates a radiograph of a patient with osteolysis around the acetabular and femoral components due to polyethylene wear following THA. Polyethylene wear and osteolysis have been an important cause of long-term failure of THA. The technique of highly cross-linking polyethylene was developed to make the material more resistant to wear and reduce the incidence of this mechanism of failure in arthroplasty.
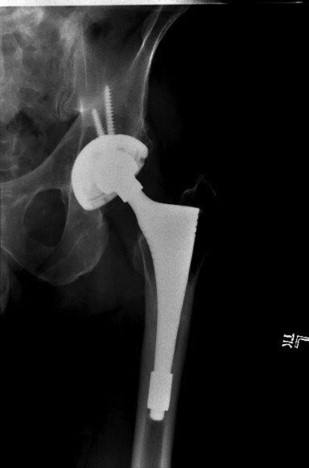
Ionizing γradiation is used to highly cross-link polyethylene by breaking hydrogen-carbon bonds, which then allows molecular cross-linking, thus improving the wear characteristics of the polymer but leading to the creation of free radicals. These free radicals can allow the polyethylene to oxidize over time and decrease the material’s fracture resistance. Irradiation with oxygen present potentiates this detrimental effect and leads to early oxidation. Fig. 2 demonstrates a thin section of a retrieved conventional polyethylene insert demonstrating white banding due to subsurface oxidation of the material. The result of oxidation is a reduction in the mechanical properties leading to a more brittle polyethylene. Delamination of the polyethylene in TKA can be seen under these circumstances. Cracking can compromise the locking mechanism. As a result, modern components are sterilized and irradiated in oxygen-free environments with the use of inert gas or gas sterilization.
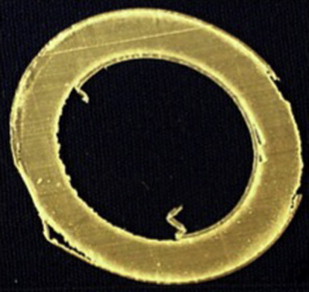
Postradiation processing techniques have been developed to reduce or eliminate the number of free radicals that remain after γ irradiation. Remelting, annealing, and mechanical elimination of free radicals are 3 well-described techniques that have been used to improve the oxidative stability of HXLPE. When remelting, the polyethylene is heated past its melting point to eliminate crystals and allow the remaining free radicals to cross-link with each other. Remelting creates a material with no free radicals but slightly decreases mechanical strength and fracture toughness. During annealing, the maximum temperature is less than the melting point. Annealing results in a greater number of remaining free radicals compared with melting but may be less detrimental to the mechanical properties and J-fracture toughness.
A more recent technique for reducing oxidation in polyethylene involves manufacturing the polymer to include an antioxidant. The antioxidants can stabilize free radicals that exist as a byproduct of manufacturing and protect against future in vivo oxidation as well. Vitamin E has been the most commonly used antioxidant for this purpose. Irganox is another antioxidant that was recently introduced for TKA. Laboratory data have suggested that the use of vitamin E in polyethylene can decrease oxidation characteristics without negatively impacting the mechanical qualities. It eliminates the need for melting. There is also some evidence that it is associated with a reduction in the biologic activity of wear particle. Long-term clinical data are not yet available, but clinical studies are ongoing. Greene and colleagues presented a multicenter prospective study of 977 THA patients. The vitamin E–diffused polyethylene group had −0.04 mm/yr head penetration at 5 years and no evidence of osteolysis. An radiostereometric analysis study of vitamin E UHMWPE by the same group demonstrated 0.05-mm median head penetration in 47 patients at 5 years.
The types of wear that most frequently impact implanted polyethylene in THA and TKA are adhesive, abrasive, and third-body wear. Adhesive wear is an expected wear pattern in arthroplasty that is due to the friction between the polyethylene and the metal or ceramic-bearing surface with which it articulates. Abrasive wear occurs because of a harder surface sliding against a softer surface. In this case, polyethylene is the softer surface. Fig. 3 demonstrates the articular surface of a highly cross-linked and melted polyethylene insert retrieved because of sepsis at 5 years showing retention of the original machine marks, indicating extremely low wear. Fig. 4 shows a retrieved conventional polyethylene tibial insert demonstrating delamination and pitting due to subsurface oxidation as well as loss of material due to adhesive and abrasive wear. Third-body wear is caused by some substance other than the prosthesis causing abrasion of the polyethylene. This substance is most often a piece of bone, cement, or metal in arthroplasty. HXLPE retrievals can sometimes show surface changes that appear to be wear but are just scratches. The material restores its form because of shape memory.
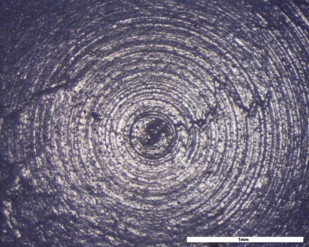
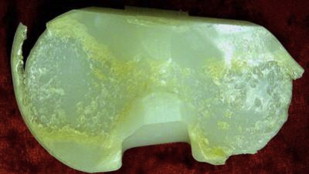
Introduction
Total hip arthroplasty (THA) and total knee arthroplasty (TKA) have excellent track records with regards to pain relief and improvement of function. Over the past several decades, there have been significant improvements in the engineering and materials science of bearing surfaces. The use of highly cross-linked polyethylene (HXLPE) in large-joint arthroplasty has led to improved outcomes, particularly for THA. This article briefly reviews the history of the development of HXLPE and provides an in-depth review of the clinical results regarding the durability of HXLPE in THA and TKA.
Sir John Charnley attempted to develop a low-friction arthroplasty with the use of Teflon-bearing surfaces. The wear characteristics of this material were unsatisfactory with dramatic early failure from wear. He eventually transitioned to metal-on-polyethylene THA. Charnley’s recognition that polyethylene was a good bearing surface revolutionized hip arthroplasty.
The use of polyethylene as a bearing surface contributed to the success of THA and TKA; however, it was not without complications. Ultra-high-molecular-weight polyethylene (UHMWPE) wear can lead to a local reaction that results in bone resorption or osteolysis. Fig. 1 demonstrates a radiograph of a patient with osteolysis around the acetabular and femoral components due to polyethylene wear following THA. Polyethylene wear and osteolysis have been an important cause of long-term failure of THA. The technique of highly cross-linking polyethylene was developed to make the material more resistant to wear and reduce the incidence of this mechanism of failure in arthroplasty.
Ionizing γradiation is used to highly cross-link polyethylene by breaking hydrogen-carbon bonds, which then allows molecular cross-linking, thus improving the wear characteristics of the polymer but leading to the creation of free radicals. These free radicals can allow the polyethylene to oxidize over time and decrease the material’s fracture resistance. Irradiation with oxygen present potentiates this detrimental effect and leads to early oxidation. Fig. 2 demonstrates a thin section of a retrieved conventional polyethylene insert demonstrating white banding due to subsurface oxidation of the material. The result of oxidation is a reduction in the mechanical properties leading to a more brittle polyethylene. Delamination of the polyethylene in TKA can be seen under these circumstances. Cracking can compromise the locking mechanism. As a result, modern components are sterilized and irradiated in oxygen-free environments with the use of inert gas or gas sterilization.
Postradiation processing techniques have been developed to reduce or eliminate the number of free radicals that remain after γ irradiation. Remelting, annealing, and mechanical elimination of free radicals are 3 well-described techniques that have been used to improve the oxidative stability of HXLPE. When remelting, the polyethylene is heated past its melting point to eliminate crystals and allow the remaining free radicals to cross-link with each other. Remelting creates a material with no free radicals but slightly decreases mechanical strength and fracture toughness. During annealing, the maximum temperature is less than the melting point. Annealing results in a greater number of remaining free radicals compared with melting but may be less detrimental to the mechanical properties and J-fracture toughness.
A more recent technique for reducing oxidation in polyethylene involves manufacturing the polymer to include an antioxidant. The antioxidants can stabilize free radicals that exist as a byproduct of manufacturing and protect against future in vivo oxidation as well. Vitamin E has been the most commonly used antioxidant for this purpose. Irganox is another antioxidant that was recently introduced for TKA. Laboratory data have suggested that the use of vitamin E in polyethylene can decrease oxidation characteristics without negatively impacting the mechanical qualities. It eliminates the need for melting. There is also some evidence that it is associated with a reduction in the biologic activity of wear particle. Long-term clinical data are not yet available, but clinical studies are ongoing. Greene and colleagues presented a multicenter prospective study of 977 THA patients. The vitamin E–diffused polyethylene group had −0.04 mm/yr head penetration at 5 years and no evidence of osteolysis. An radiostereometric analysis study of vitamin E UHMWPE by the same group demonstrated 0.05-mm median head penetration in 47 patients at 5 years.
The types of wear that most frequently impact implanted polyethylene in THA and TKA are adhesive, abrasive, and third-body wear. Adhesive wear is an expected wear pattern in arthroplasty that is due to the friction between the polyethylene and the metal or ceramic-bearing surface with which it articulates. Abrasive wear occurs because of a harder surface sliding against a softer surface. In this case, polyethylene is the softer surface. Fig. 3 demonstrates the articular surface of a highly cross-linked and melted polyethylene insert retrieved because of sepsis at 5 years showing retention of the original machine marks, indicating extremely low wear. Fig. 4 shows a retrieved conventional polyethylene tibial insert demonstrating delamination and pitting due to subsurface oxidation as well as loss of material due to adhesive and abrasive wear. Third-body wear is caused by some substance other than the prosthesis causing abrasion of the polyethylene. This substance is most often a piece of bone, cement, or metal in arthroplasty. HXLPE retrievals can sometimes show surface changes that appear to be wear but are just scratches. The material restores its form because of shape memory.
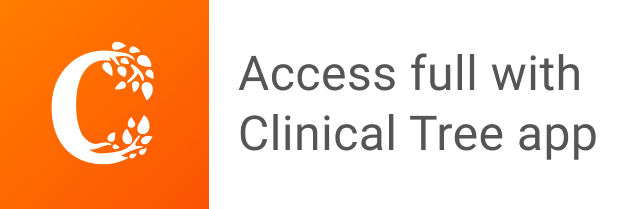