Ceramic Articulations
Moussa Hamadouche
Introduction
Ceramics are defined as nonmetallic and inorganic materials, including a broad range of compositions. The usual processing of ceramics consists of mixing the particulates of the material together with water and an organic binder. The mixture then is pressed into a mold to obtain the desired shape. Subsequently, the formed piece is dried to evaporate the water, and the binder is burned out following thermal treatment. Firing or sintering at a very much higher temperature then densifies the resultant part. The final microstructure of the ceramic is greatly dependent on the thermal process applied (maximal temperature reached, duration of thermal steps), and can belong to one of the following five categories: glass, plasma-sprayed polycrystalline ceramic, vitrified ceramic, solid-state sintered ceramic, or polycrystalline glass-ceramic. Other parameters such as purity of the powder, grain size, grain distribution, and porosity are of paramount importance for the mechanical and biologic properties. The extended use of bioceramics in medicine is related to their excellent biocompatibility related to their high oxidation level.
Ceramics used in orthopedic surgery are basically classified according to the tissue response when implanted in an osseous environment. Hence, they are described as bioactive ceramics and inert ceramics. The bioactivity of a material can be defined as its ability to biologically bond bone, whereas an inert ceramic elicits a fibrous reaction of minimal magnitude. In clinical practice, inert fully dense ceramics are used as bearings in total joint replacements because of their exceptional wear resistance and tribologic properties, whereas bioactive ceramics are utilized as coatings to enhance the fixation of a device or as bone graft substitutes because of their osteoconductive properties.
In this chapter, we will describe the in vitro properties and clinical applications of ceramics used in hip joint surgery. Sliding ceramics and bioactive ceramics will be detailed in two distinct sections.
Sliding Ceramics
The most widely used bearing couple in total joint replacements remains metal-on-polyethylene. However, the long-term survival of the artificial joint is impaired by wear of the components, ultimately leading to osteolysis around the prosthetic components. This phenomenon has been related to an inflammatory response induced by wear debris occurring from both the articulating and nonarticulating surfaces. Among the different particle types found in the membranes surrounding the loosened components, polyethylene debris has been identified as a major factor inducing macrophage activation leading to the production of bone-resorbing cytokines, that results in loss of bone stock, especially in the young and active population (1). To eliminate or reduce complications related to polyethylene (2), Pierre Boutin (3) first introduced ceramics in the early 1970s. Sliding ceramics are mainly used in total hip arthroplasty (THA) as femoral heads articulating against polyethylene, or as acetabular inserts in ceramic-on-ceramic combination.
Because of their relative brittle nature, fracture of ceramic femoral heads has been along with cost the main limitations to their expanded use worldwide. However, the risk for fracture has been substantially reduced due to a great improvement in the manufacturing process (purity, density, grain size, and distribution), quality control, proper surgical technique, and accurate fixation of the ceramic ball to the femoral stem through a well-designed Morse taper avoiding critical stresses in the head. For obvious reasons, it is difficult to determine the actual incidence of fracture the frequency of which is very variable. However, when the above conditions are optimized, the rate has been evaluated to 0.02% for alumina heads and 0.03% for zirconia heads (4).
Materials Science
Alumina Ceramic
Surgical grade dense alumina is obtained by sintering alumina powder at temperatures comprised between 1,600° and 1,800°C. The resultant material is in its highest state of oxidation, allowing thermodynamic stability, chemical inertness, and therefore excellent resistance to corrosion. Moreover, an improvement in the manufacturing process has lowered the grain size and grain distribution, which are major factors to help avoid crack propagation and fracture (Fig. 19.1A,B). Machining processes also should be very accurate to avoid any crack initiation or other problems that could alter the material. Alumina is a standardized
material since 1984 (International Standard Organization, ISO 6474). Properties of surgical grade dense alumina are summarized in Table 19.1. The Young modulus is 300 times higher than the one of cancellous bone, and 190 times higher than that of polymethyl methacrylate. Alumina is a brittle material owing excellent compression strength whereas bending strength is limited. Alumina exhibits a linear elastic behavior and low fracture toughness. This means that the material has no possibility to deform without breakage. The fracture toughness (K1c value) is used to measure the brittleness of a material. Fracture will occur if the stress intensity factor K1 of one of the volume elements becomes larger than the fracture toughness. In fact, the mode of failure is usually related to subcritical crack growth. This is due to imperfections in the materials including pores, inhomogeneities, scratches, and micronotches in the material or at its surface. Under appropriate conditions, these initial cracks will grow at different velocities depending on the size of the initial flaw, the quality of the alumina material, and the load applied. Local stresses are related to the geometry, shape, and design. They can be entirely calculated and thus predicted using finite element analysis models. It is not possible to completely avoid limited imperfections during material processing, but it is of major importance that the initial crack length be smaller than 100 μm. Willmann (4) demonstrated that under normal physiologic condition, the stress intensity K1 will not reach the fatigue limit. Moreover, proof tests have been designed to prevent fracture and check accurately any manufacturing flaw that could have been introduced during production. These tests randomly conducted can result in deleting a complete batch if not compelling to the standards. The burst strength tests give values of 102 kN for a 32-mm head diameter and a 12/14-mm cone. These values exceed the FDA requirements that are 46 kN and the physiologic stresses that are considered to be less than 20 kN. Any material interposed between the metal and the ceramic head could give rise to stress intensity factors that could then exceed the fatigue limit. A thorough cleaning process of the metal Morse taper as well as a smooth introduction of the ceramic head without heavy hammering at surgery is mandatory (5). In Sedel et al.’s (6,7) department, the risk for fracture has been estimated to be less than 1/1,000 for a 10-year period. The risk for fracture reported by Willmann (4) based on over 1.5 million heads used since 1974 was 0.02%. These figures were confirmed by Heck et al. (8) who reported on 22 out of 10,000 ceramic head fractures over a 5-year period based upon a survey study of the entire membership of the American Association of Hip and Knee Surgeons.
material since 1984 (International Standard Organization, ISO 6474). Properties of surgical grade dense alumina are summarized in Table 19.1. The Young modulus is 300 times higher than the one of cancellous bone, and 190 times higher than that of polymethyl methacrylate. Alumina is a brittle material owing excellent compression strength whereas bending strength is limited. Alumina exhibits a linear elastic behavior and low fracture toughness. This means that the material has no possibility to deform without breakage. The fracture toughness (K1c value) is used to measure the brittleness of a material. Fracture will occur if the stress intensity factor K1 of one of the volume elements becomes larger than the fracture toughness. In fact, the mode of failure is usually related to subcritical crack growth. This is due to imperfections in the materials including pores, inhomogeneities, scratches, and micronotches in the material or at its surface. Under appropriate conditions, these initial cracks will grow at different velocities depending on the size of the initial flaw, the quality of the alumina material, and the load applied. Local stresses are related to the geometry, shape, and design. They can be entirely calculated and thus predicted using finite element analysis models. It is not possible to completely avoid limited imperfections during material processing, but it is of major importance that the initial crack length be smaller than 100 μm. Willmann (4) demonstrated that under normal physiologic condition, the stress intensity K1 will not reach the fatigue limit. Moreover, proof tests have been designed to prevent fracture and check accurately any manufacturing flaw that could have been introduced during production. These tests randomly conducted can result in deleting a complete batch if not compelling to the standards. The burst strength tests give values of 102 kN for a 32-mm head diameter and a 12/14-mm cone. These values exceed the FDA requirements that are 46 kN and the physiologic stresses that are considered to be less than 20 kN. Any material interposed between the metal and the ceramic head could give rise to stress intensity factors that could then exceed the fatigue limit. A thorough cleaning process of the metal Morse taper as well as a smooth introduction of the ceramic head without heavy hammering at surgery is mandatory (5). In Sedel et al.’s (6,7) department, the risk for fracture has been estimated to be less than 1/1,000 for a 10-year period. The risk for fracture reported by Willmann (4) based on over 1.5 million heads used since 1974 was 0.02%. These figures were confirmed by Heck et al. (8) who reported on 22 out of 10,000 ceramic head fractures over a 5-year period based upon a survey study of the entire membership of the American Association of Hip and Knee Surgeons.
Table 19.1 Comparative Physical Properties of Surgical Grade Alumina and Zirconia Ceramics | ||||||||||||||||||||||||||||||||||||||||
---|---|---|---|---|---|---|---|---|---|---|---|---|---|---|---|---|---|---|---|---|---|---|---|---|---|---|---|---|---|---|---|---|---|---|---|---|---|---|---|---|
|
All ceramics are not alike. Alumina is monophasic polycrystalline, very hard, very stable, highly oxidized, with a high thermal conductivity coefficient, low bending stress, and low resilience. The resultant material is in its highest state of oxidation, allowing thermodynamic stability, chemical inertness, and therefore excellent resistance to corrosion. The ionic structure of alumina ceramic creates a hydrophilic structure and fluid film lubrication resulting in a higher wettability than that of orthopedic polymers and metals. It has been demonstrated in vitro that water is adsorbed with high
bond strength and that proteins quickly and completely cover the ceramic surface with a monolayer after surgical implantation. This phenomenon improves lubrication of the joint (9).
bond strength and that proteins quickly and completely cover the ceramic surface with a monolayer after surgical implantation. This phenomenon improves lubrication of the joint (9).
Zirconia Ceramic
Zirconia was introduced to overcome some of the limitations of alumina related to the mechanical properties of the material (10). However, pure zirconia is an unstable material, exhibiting three different crystalline phases: Monoclinic, tetragonal, and cubic. The phase changes result in large volume changes, and decrease significantly the mechanical properties of the material due to crack production. Stabilization of zirconia to maintain the tetragonal phase by adding oxides has therefore been performed. Yttrium-stabilized tetragonal zirconia polycrystalline (Y-TZP) has a fine grain size, and offers the best mechanical properties as summarized in Table 19.1. This material has also been standardized in 1997 (International Standard Organization, ISO 13356). Tetragonal phase that is the most resistant tends to transform into monoclinic phase. This phenomenon explains its higher resistance to shock but it also explains its lower sliding properties and moreover its unstable situation over time. Transformation phase per year is debated. Some stated that 2% of the bulk material transforms each year. Other described a phase transformation that is more important at the surface when compared to the inner material (11).
The thermal conductivity of zirconia ceramic is low (12). This phenomenon could be responsible for some of the negative clinical results described below in this chapter. However, the question remains open and it could be suspected that something concerning zirconia ceramic has not been clearly understood currently.
Mixed Oxide Ceramic
A new class of ceramic materials has been developed during the past 10 years to combine the advantages of both alumina and zirconia (13). These mixed oxide ceramics or composite ceramic materials containing up to 80% zirconia are based on the principle of transformation toughening to improve the strength of pure alumina. The most popular of this class of materials is Biolox Delta ceramic (Cermatec AG) which contain 82% alumina and 17% zirconia stabilized in tetragonal phase (Figs. 19.2 and 19.3) (14). This alumina matrix composite (AMC) is reinforced through three mechanisms. First, elongated grains of strontium oxide with a hexagonal structure are dispersed throughout the alumina matrix. Due to their shape, these grains are able to stop crack propagation. Second, the presence of metastable zirconia grains within the structure also increases the fracture toughness of AMC. In case of crack, zirconia will transform from tetragonal to monoclinic phase resulting in an increased volume of zirconia. This phenomenon will stop crack propagation through energy absorption. Finally, the addition of chromium oxide as a solid solution allows for compensation of hardness loss related to the presence of zirconia, resulting in hardness comparable to that of pure alumina (Table 19.1).
Phase transformation of AMC has been tested under severe conditions (aging in autoclave for 6 hours, ASTM F-2345), and no significant difference was observed between the aged and nonaged specimens. These data demonstrate excellent hydrothermal stability of AMC material when compared to pure zirconia ceramic.
Oxidized Zirconium
Oxidized zirconium, also named Oxinium (Smith & Nephew, Memphis, TN), is not a strict ceramic as described previously. However, it should be included in this chapter as the oxidized surface confers to the material tribologic properties close to a ceramic (15). Oxinium is a metal alloy made of 97.5% zirconium and 2.5% niobium. This metal alloy is subjected to a thermal treatment at 500° to 700°C in air for 6 hours resulting in an oxidized surface layer of 5 μm on the surface made of monoclinic zirconium dioxide (zirconia, ZrO2). This ceramic layer is not a coating but a continuum between the metal substrate and an oxygen-enriched metal without an additional interface. This manufacturing process is fundamentally different from that of various ceramic-like coatings that all led to failures including plasma-sprayed ceramic and diamond-like carbon coatings using chemical or physical vapor deposition methods. Oxinium is a highly scratch-resistant material when compared to CoCr.
In addition, as the core is metallic, it can deform under burst strength but will not break.
In addition, as the core is metallic, it can deform under burst strength but will not break.
Tribologic Properties
In Vitro Wear Studies
Several in vitro wear studies have clearly demonstrated that alumina-on-alumina was an excellent friction couple (16,17,18,19,20,21,22,23). Indeed, comparative studies of alumina-on-alumina versus metal-on-polyethylene favored the ceramic couple. The outstanding tribologic properties of the alumina couple are related to a low surface roughness (Ra = 0.02 μm) due to the low grain size, a high hardness responsible for major scratch resistance, a high wettability, and fluid film lubrication. Two phases have been described during in vitro wear testing of alumina against alumina. The first phase or “run-in phase” concerns the first million cycle during which volumetric wear rate measures from 0.1 to 0.2 mm (24) per million cycle, whereas during the second phase or “steady-state phase,” volumetric wear rate decreases to less than 0.01 mm3 per million cycle. These results have been confirmed by Clarke et al. (19), up to 20 million cycles. In addition, it has been reported on a simulator study using bovine serum as a lubricant up to 14 million cycles that the steady-state wear rate was 13 times lower when compared to the running state (0.3 vs. 0.02 mm3 per million cycle). These figures are about 2,000 to 5,000 times less than that of metal-on-polyethylene friction couple. The friction coefficient of the alumina couple is 0.09 versus 0.21 for metal-on-polyethylene bearings. Two major factors should be considered to enhance alumina-on-alumina tribologic performances, including limited deviations from sphericity and optimal clearance between the alumina femoral head and cup. In vitro wear studies (25) have demonstrated that the optimal deviation from sphericity was ±1 μm, and that optimal clearance between the two components was from 20 to 50 μm. Contrary to metal-on-polyethylene, the alumina-on-alumina combination does not favor small head size. Alumina femoral heads ranging from 32 to 36 mm also generate little debris. However, it should be emphasized that up to studies published by J. Fisher’s group in Leeds (26,27), in vitro wear results differed from what had been observed in vivo. Indeed, wear patterns observed in vitro were different from those observed on retrieved specimens. To reproduce separation observed in metal or alumina-on-polyethylene couple under fluoroscopy between the ball and socket during the swing phase of walking (28), this group introduced microseparation during hip simulator testing by applying a force in the lateral direction using a spring. This force combined with a low swing phase load allowed the artificial joint to separate. Testing was carried out using bovine serum as the lubricant. Under these conditions, femoral heads showed wear stripes associated with wear on the rim of the cups (26). Volumetric wear determined gravimetrically was 1.24 mm3 per million cycle. Moreover, a bimodal distribution of particle sizes was observed (27). Nanometer-sized particles (1 to 35 nm) were probably obtained under normal articulating conditions from relief polishing, whereas micrometer-sized particles (0.05 to 10 μm) were assumed to originate from the wear stripes related to transgranular fracture of the alumina ceramic. Although the assumptions obtained from this study are very appealing, it should be noted that no microseparation was observed in vivo under fluoroscopy while patients with an alumina-on-alumina THA were performing active hip abduction (Komistek RD, Northcut EJ, Bizot P, et al. In vivo determination of hip joint separation in subjects having either an alumina-on-alumina or alumina-on-polyethylene total hip arthroplasty. Presented at the 69th American Academy of Orthopaedic Surgeons, Dallas, TX, 2002). The sensitivity of the method used by Komistek et al. might have been too low.
In vitro wear studies evaluating either alumina- or zirconia-on-polyethylene are very confusing as a number of them used water or nonphysiologic protein concentrations in the bovine serum as the joint lubricant (29,30). As ceramics could be manufactured with properties including a surface roughness (Ra) as small as 0.02 μm, an increased sphericity, and a high scratch resistance, it was postulated that these might reduce the long-term wear debris production of polyethylene sockets. However, after 3 to 5 million cycles, the coefficient of friction increases with subsequent deterioration of the articular surface. A critical appraisal suggests that the real reduction in wear debris production compared to metal-on-polyethylene is in the order of twofold when physiologic protein concentrations are used (29).
Concerning zirconia ceramics, Lu et al.’s (12) findings should be noted. These authors have shown that major frictional heating was observed in vitro when testing zirconia against polyethylene. This phenomenon was responsible for proteins’ lubricant precipitation. The resultant protein layer between the femoral head and polyethylene socket could protect the bearing surfaces from wear. The maximum temperatures reached in vivo are likely much lower than those observed in hip simulators as patients do not walk so fast and/or so long. Hence, the protecting layer observed in vitro may be artifact leading to underestimated polyethylene wear by simulator when testing the zirconia-on-polyethylene combination.
Wear studies even in adverse conditions have demonstrated that AMC produced very small amount of volumetric wear. In addition, excessive abduction angle of the cup had no effect on wear under microseparation (14).
The wear rate of oxinium against standard and highly cross-linked polyethylene (XLPE) has been evaluated versus CoCr using smooth and roughened heads. Both conditions demonstrated significantly less wear for oxinium when compared to CoCr. However, when smooth heads were tested against XLPE, there was no significant difference in polyethylene wear rates between CoCr and oxinium. The scratch-resistant surface of oxinium is expected to produce less wear in vivo (15).
Retrieved Implants
Besides in vitro wear studies, comprehensive retrieval studies have been performed to better understand failures and to avoid them in the future (Fig. 19.4) (31,32,33,34,35). Prudhommeaux et al. (36) have investigated the wear patterns of a series of explanted alumina components retrieved for aseptic loosening of the socket. Wear quantification on macro and microscopic scales in combination with microstructure analysis, clinical and roentgenographic data were used to identify the
main risk factors involved in the in vivo alumina wear process. Eleven alumina-on-alumina THAs retrieved for aseptic loosening at a mean 11-year follow-up were investigated. Macroscopic wear was assessed using a coordinate measuring machine. Microscopic wear features were evaluated by Talysurf analysis. Scanning electron microscopy was used to look at the alumina microstructure. Components were classified into three groups: (1) Low wear with no sign of wear and Ra values below 0.05 μm; (2) stripe wear with a visible oblong worn area on the heads and penetration rates below 10 μm/yr; and (3) severe wear with a visible loss of material on both components, showing Ra values up to 4 μm and maximum penetrations higher than 150 μm. Among the 11 available components, two showed evidence of massive wear. The remaining nine pairs exhibited linear wear rates below 15 μm/yr. This work confirmed that the wear of alumina ceramic components may take two different forms: It may be very limited with a negligible incidence on the long-term behavior of the system or it may be catastrophic, leading to a rapid destruction of the bearing surfaces. Published alumina wear rates measured in vivo appeared to be highly variable. Boutin and Blanquaert (37) reported wear rate ranging from 5 to 9 μm/yr, whereas Mittelmeier and Heisel (38) reported a wear rate of approximately 10 μm/yr. Plitz and Griss (33) gave an example showing massive wear about 0.9 mm after 3 years of implantation. These discrepancies may be related to material and design considerations. These data were published using early alumina material and since that time numerous improvements have been achieved in terms of alumina quality and prosthesis designs. Among the series published by Prudhommeaux et al. (36), the two severely worn components were implanted before 1978. After that time, wear rates always remained below 15 μm/yr with a median value of 5 μm/yr of use.
main risk factors involved in the in vivo alumina wear process. Eleven alumina-on-alumina THAs retrieved for aseptic loosening at a mean 11-year follow-up were investigated. Macroscopic wear was assessed using a coordinate measuring machine. Microscopic wear features were evaluated by Talysurf analysis. Scanning electron microscopy was used to look at the alumina microstructure. Components were classified into three groups: (1) Low wear with no sign of wear and Ra values below 0.05 μm; (2) stripe wear with a visible oblong worn area on the heads and penetration rates below 10 μm/yr; and (3) severe wear with a visible loss of material on both components, showing Ra values up to 4 μm and maximum penetrations higher than 150 μm. Among the 11 available components, two showed evidence of massive wear. The remaining nine pairs exhibited linear wear rates below 15 μm/yr. This work confirmed that the wear of alumina ceramic components may take two different forms: It may be very limited with a negligible incidence on the long-term behavior of the system or it may be catastrophic, leading to a rapid destruction of the bearing surfaces. Published alumina wear rates measured in vivo appeared to be highly variable. Boutin and Blanquaert (37) reported wear rate ranging from 5 to 9 μm/yr, whereas Mittelmeier and Heisel (38) reported a wear rate of approximately 10 μm/yr. Plitz and Griss (33) gave an example showing massive wear about 0.9 mm after 3 years of implantation. These discrepancies may be related to material and design considerations. These data were published using early alumina material and since that time numerous improvements have been achieved in terms of alumina quality and prosthesis designs. Among the series published by Prudhommeaux et al. (36), the two severely worn components were implanted before 1978. After that time, wear rates always remained below 15 μm/yr with a median value of 5 μm/yr of use.
Various studies have been performed to further explain the occurrence of massive wear. Plitz and Griss (33), Plitz and Hoss (34
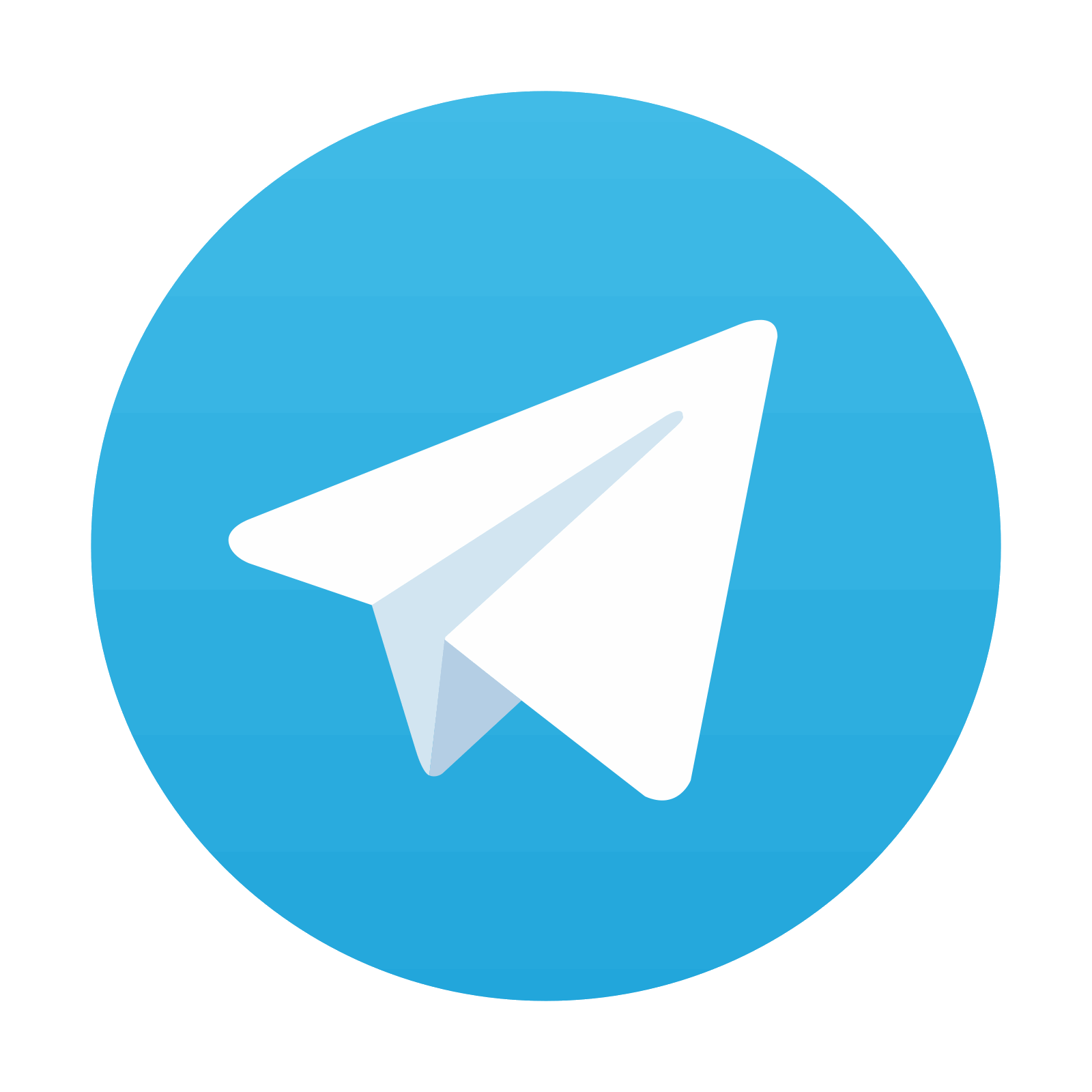
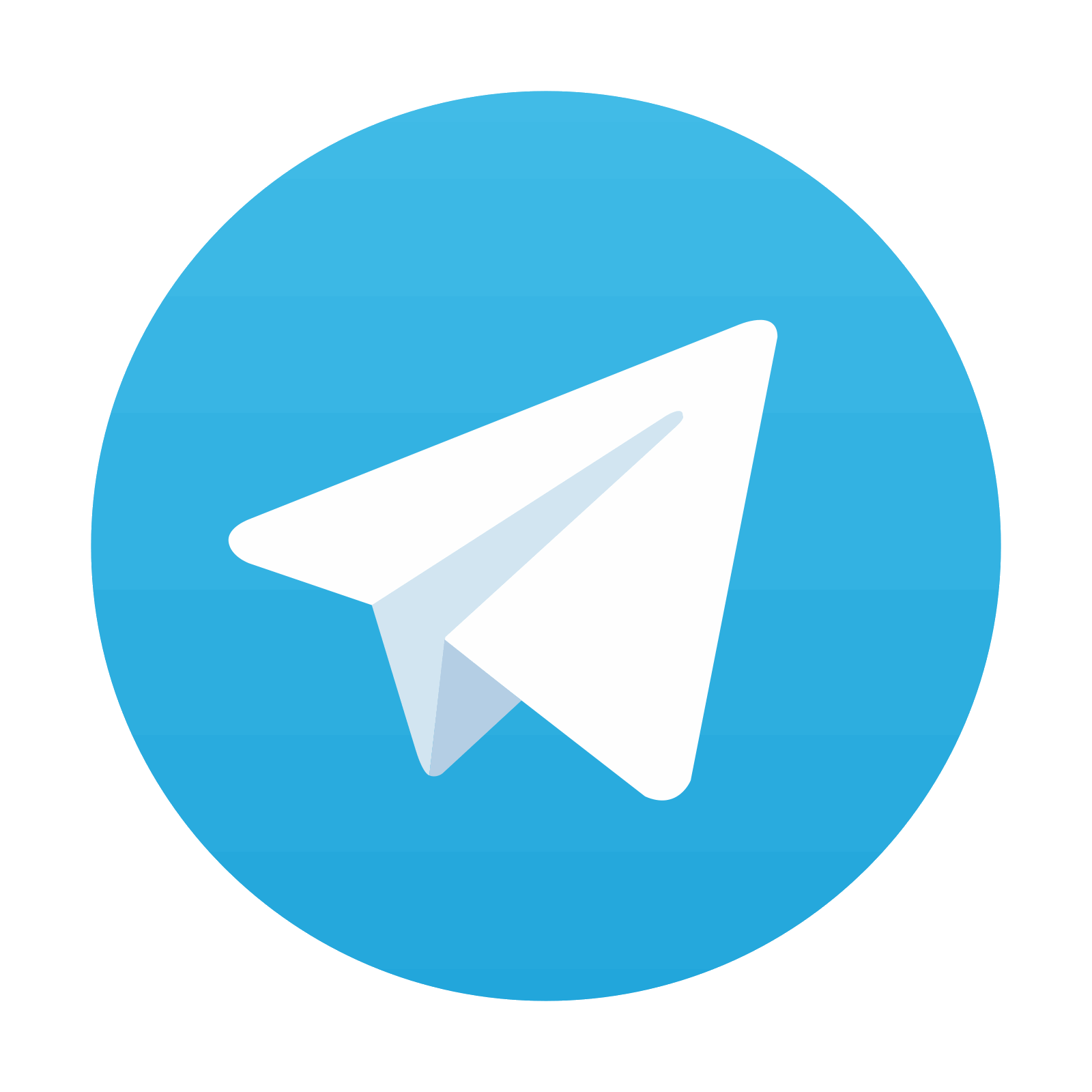
Stay updated, free articles. Join our Telegram channel
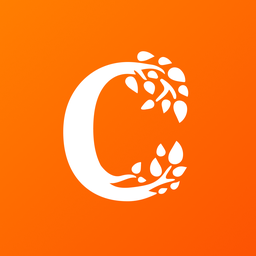
Full access? Get Clinical Tree
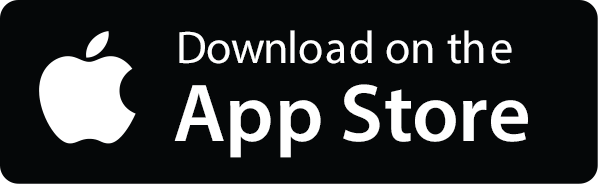

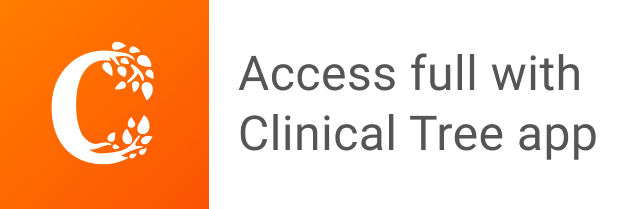