20 Principles of Finite Elements Analysis
The biomechanical community is challenged by the need to predict the mechanical response of biological tissues as bones, muscle, blood vessels, etc., especially when an intervention is mandatory. For example, the mechanical response is of major interest in the case of insertion of metallic implants in a fractured bone or in the case of stents insertion in an atherosclerotic artery. In such instances, numerical simulations by finite element (FE) methods can provide invaluable information for the clinical community, if the FE analyses are verified and validated. This chapter, therefore, provides the principles of FE methods with an emphasis on the concept of verification and validation and its optimal and successful use in biomechanical practice.
Consider as an illustrative example a physical system that is composed of a human femur that is clamped at its distal part and loaded by a given force on its head. If an experiment can be performed on the femur (as shown in Fig. 20.1), the displacements at any point on the femur′s surface as well as the strains may be measured. These are the “physical quantities” of interest, denoted by uPhy. To enable the prediction of these quantities of interest without the need to perform an experiment (or when such experiments are impossible to be performed), a mathematical model can be formulated that will provide the solutions uComp. Such complex mathematical models are usually extremely nonlinear and very difficult to formulate. Therefore, idealization assumptions are being introduced (generating idealization errors) to enable a more simplified mathematical model to be formulated, with a solution denoted by uSimp. This simplified mathematical model should be understood to be an idealized representation of the reality and should never be confused with the physical reality that it is supposed to represent. Due to the complex geometry of the domain of interest and the nonlinearity of the problem, even the simplified mathematical formulation cannot be solved analytically. Therefore, a discretization process is applied by which the simplified mathematical problem is reformulated so it can be solved on digital computers. The most frequently applied method of discretization is the FE method. The FE method finds an approximate solution denoted by uFE and the discretization error is the difference between the approximated FE solution and the solution of the simplified mathematical problem uSimp. Referring again to Fig. 20.1, one notices that:


Equation (20.1) implies that if one wishes to determine how well the FE solution represents the physical quantities of interest, then the discretization, the idealization, and the conceptualization errors have to be quantified.
This chapter concentrates on the principles of the FE solution, uFE, and on the estimation of the associated discretization error, eD. Estimating eD is essentially what is meant by verification.
The first part of this chapter provides a deeper understanding on the basics and principles of FE methods, and the second part is more practical, discussing the appropriate use of FE analyses and the interpretation of FE results. Specific considerations and pitfalls are highlighted, and a proper process for the verification of the results is detailed.
20.1 The Finite Element Methodology
Let us consider for demonstration purposes the mechanical response of a femur under moderate loads, which after idealization can be considered to behave linearly elastic having isotropic but inhomogeneous material properties. One would be interested in the displacements, strains, and stresses at any point in the femur to determine, for example, if there is a risk of fracture. For this purpose, an FE analysis may be performed that requires three ingredients: (1) the geometric description, (2) a “constitutive model” and material properties that describe the physical phenomenon and the behavior of the material, and (3) boundary conditions (forces and constrains) that are applied.
20.2 The Geometry and Finite Element Mesh
For a patient-specific analysis, the geometry description of the femur may be obtained from a computed tomography (CT) scan, so that the outer and inner contours of the femur can be segmented (Fig. 20.2). After segmentation, the data is manipulated using a computer-aided design software and a solid model of the bone is generated, call it Ω. This solid model of a complex topology can be divided into a collection of smaller, simple geometric shapes such as hexahedral, pentahedral, or tetraherdral elements—each called a finite element. The collection of these elements is called the FE “mesh”. Each element is denoted by Ω⍳, so that ⋃ Ω⍳ = Ω.

20.3 The Mathematical Basis of the Finite Element Method
To compute the elastic response of the femur, a set of partial differential equations (the Navier-Lame system,1 known also as the elasticity system, without body forces) has to be solved in the domain of the femur denoted by Ω:

Here uSimp = [ux(x,y,z), uy(x,y,z), uz(x,y,z)]T is the sought displacement vector, E(x,y,z) (Young′s modulus), and v(x; y; z) (Poisson ratio) are the material properties at each point. The elasticity system (20.2) is complemented by traction T or displacement boundary conditions. The analytical solution that solves this problem would be the “classical” or “strong” solution uSimp. However, due to the complex domain of the femur, it is impossible to obtain analytically uSimp. To obtain an approximated solution by FE methods, we first transform the strong form into a “weak formulation” by multiplying the set of equations by a “test function” v = (vx(x,y,z),vy(x,y,z),vz(x,y,z))T, then integrate over the entire femur and apply the Green′s lemma (integration by parts) so we finally obtain the formulation:

The weak formulation of equation (20.3) can also be cast into an equivalent formulation, the “minimum potential energy”:
Seek uSimp that minimizes the “potential energy”:

Once uSimp is found, one can easily compute the stress vector by σ = [E] [D] uSimp.
To solve equation (20.4), a major difficulty still exists, namely, one is required to find one displacement field among an infinite number of displacements that when inserted into ∏(u) will result in a minimum value. Let us denote by ℰ(Ω) the space of all possible displacements, so we seek for uSimp ∊ ℰ(Ω). From the practical point of view, this is of course impossible, and instead of an infinite number of possible functions, we seek a displacement field within a finite number of functions (we denote this finite set of functions S (Ω) ⊂ ℰ(Ω) that satisfies equation (20.4). This function is the FE solution, uFE. Of course, that uFE may not provide the minimum value to ∏(u), among all possible functions in ∏(Ω), but it is the “closest” to uSimp among all functions in S (Ω). The discretization error is introduced because we seek for a solution in S(Ω) instead of in ℰ(Ω). If one uses hierarchical spaces, that is a family of increasingly larger spaces, each containing the smaller spaces, S1(Ω) ⊂ S2(Ω) ⊂ S3(Ω) … ⊂ ℰ(Ω), then the FE solutions uFE1, uFE2, uFE3 … obtained are progressively closer to uSimp. Of course, as the space S (Ω) is enriched by more and more functions, then the approximated solutions become closer to the exact solution. The systematic enrichments of the subspaces are called extensions, and these are mandatory for estimating the discretization error to quantify how close are uFE1, uFE2, uFE3 … to uSimp. We will get back to the estimation of the discretization later on.
Having a mesh, the integral over the entire domain in equation (20.4) is the sum of integrals over the elements, so that equation (20.4) can now be stated as:

One may observe that we partitioned the overall problem into “elemental problems,” and have now to compute the integrals in equation (20.5) over each element. Integrating over different-shaped hexahedra elements, for example, is a complicated procedure. To overcome this difficulty, a standard element is introduced ΩST = {(ζ, ŋ, ς) −1 ≤ ζ ≤ 1, −1 ≤ ŋ ≤ 1, −1 ≤ ς ≤ 1,} and an associated “mapping” is possible so to “map” the standard hexahedral element into any “real” hexahedral element with curved faces (see Fig. 20.3) by using the blending function method.2 In this manner, each integral in equation (20.5) is evaluated over the standard element introducing the Jacobian of the mapping. For example:


Because the minimum potential energy formulation has been split into a sum over all elements, and furthermore, all integrations are performed over the standard element, it is only natural to define a basis function on the standard element. In each element, the displacements are represented by a set of basis functions—these are also called shape functions. Let uFE in each element be expressed in terms of elemental M basis functions, which are constructed by monomials, Ni(ζ, ŋ, ς) (spanning a finite-dimensional subspace):

where ai(l) are the amplitudes of the basis functions in element l, and for example N1=18(1−ζ)(1−η)(1−ς)N_1 = {1 \over 8}(1 – \zeta )(1 – \eta )(1 – \varsigma ). Seeking for uFE reduces to the determination of the unknowns ai(l). These are collected from all elements in the FE model and stored in a vector denoted a. The number of entries in the vector a represents the dimension of the space in which uFE is sought and is called the number of degrees of freedom (DOFs).
Substituting equation (20.7) in equation (20.6) and thereafter in equation (20.5), then collecting the contribution of all elements (a process named the assembly process), one obtains the set of algebraic equations, which may be stated as:
Find the vector a that minimizes

where [K] is denoted stiffness matrix and r is the load vector. The FE solution is obtained by inverting the stiffness matrix and multiplying it by the load vector. In most FE methods, the stiffness matrix is symmetric and sparse, therefore efficient numerical methods exist that invert it (e.g., a problem with a million DOFs can be solved nowadays on a personal computer within less than half an hour).
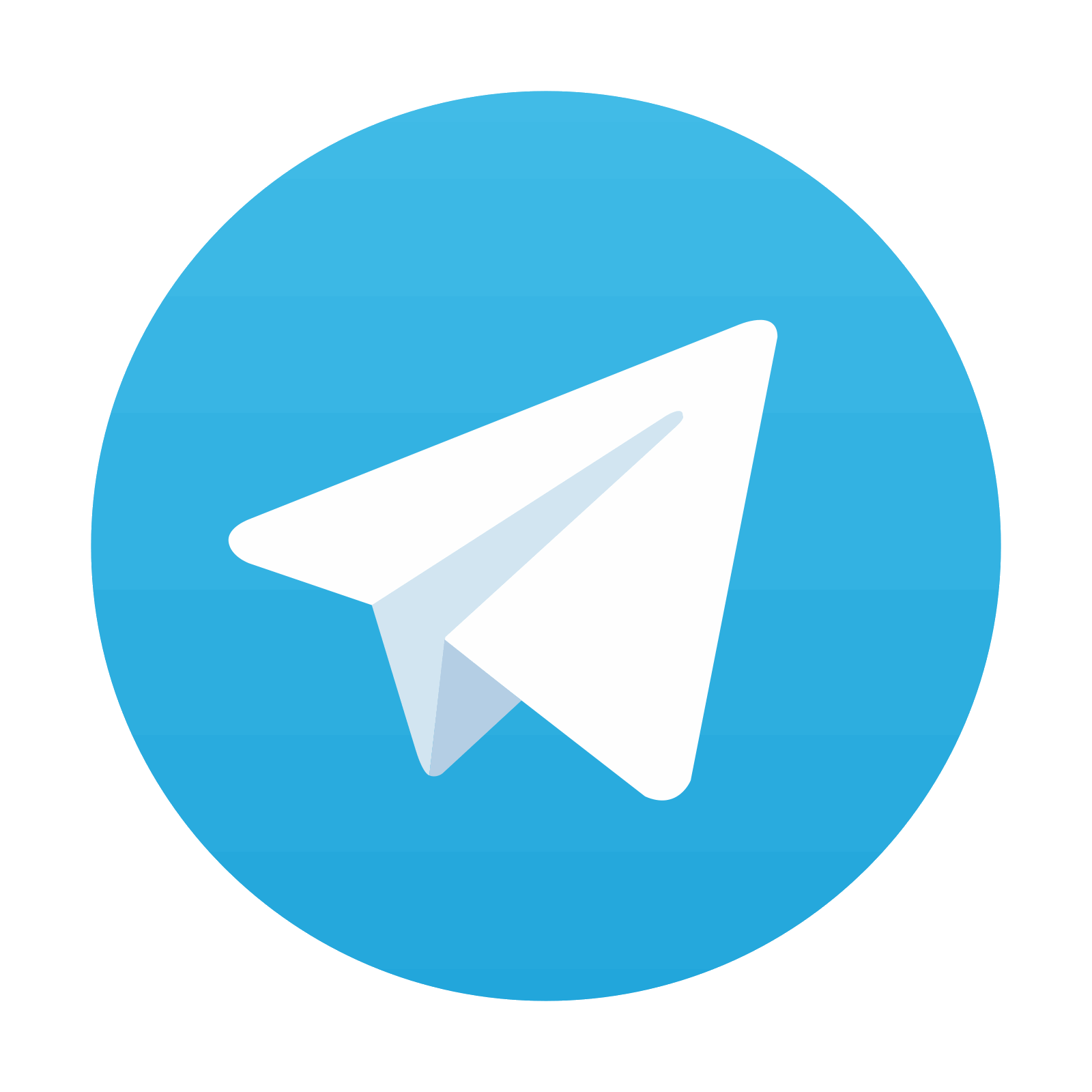
Stay updated, free articles. Join our Telegram channel
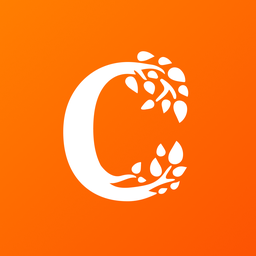
Full access? Get Clinical Tree
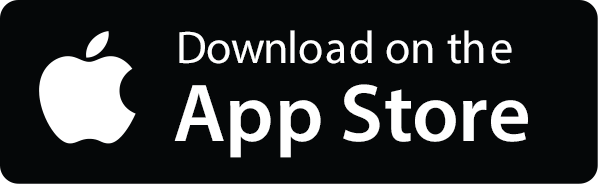
