Upper Limb Body-Powered Components
Annie Hess CP
Neither Annie Hess nor any immediate family member has received anything of value from or has stock or stock options held in a commercial company or institution related directly or indirectly to the subject of this chapter.
ABSTRACT
Body-powered prostheses remain the most commonly prescribed category of upper limb prosthesis. A range of terminal devices, including both hooks and hands, is commercially available, along with a number of different wrist, elbow, and shoulder joints. A comprehensive understanding of the various features, benefits, and limitations of these component options will allow the rehabilitation team to match their detailed prosthetic recommendations to the needs and preferences of the individual user.
Keywords:
body-powered components; cable-driven; conventional prosthesis; upper-limb prosthetic components
Introduction
Body-powered prostheses are the most commonly prescribed upper limb prostheses for individuals with amputations and limb differences. They have been used for centuries and remain popular among clinicians and users. In contrast to externally powered prostheses, which draw power from an external, nonanatomic source such as a battery to drive the motors of prosthetic components, body-powered prostheses use gross body movements to operate the prosthetic components. These motions increase the distance between two points on the body, and this linear increase is referred to as excursion. The excursion is captured with a harness and transmitted through a cable system to cause movement of the hand, hook, wrist, or elbow. For this reason, bodypowered prostheses are sometimes referred to as cable-driven prostheses. Different components require various amounts of excursion to open, close, or otherwise operate.
Body-powered designs have remained popular over the years because they offer many advantages over other systems. They are low cost, lightweight, and reliable. Many users prefer their mechanical simplicity and predictable response. Because the user can feel the cable tension and force during operation, body-powered systems offer a level of proprioception not generally available with externally powered prostheses. These benefits, combined with the fine prehension offered by hooks, result in an extremely functional device for everyday tasks. Body-powered systems also are suitable for heavy-duty activities and for use in dirty, wet, and corrosive environments.
However, body-powered prostheses also have many disadvantages. Some methods of operating cable-controlled systems require substantial force and effort. Some harnessing approaches used to anchor the control cable can compress the axilla on the contralateral side, which can be uncomfortable and may lead to nerve compression over time. Individuals with a proximal limb absence usually find it difficult to generate the excursion and power necessary to operate a body-powered hand and elbow. Similarly, shorter limbs have reduced lever arms and smaller areas over which forces can be distributed, potentially resulting in difficulty generating the necessary operating power or creating discomfort from the extreme forces on the limb.
Despite these challenges, and even in the presence of advancing externally powered technologies, body-powered designs maintain an important place in the prescription of upper limb prostheses. A recent survey of clinicians reported that those with the most experience in upper limb prosthetics were less likely to think that body-powered prostheses were outdated.1
Terminal Devices
The terminal device is the most distal component of an upper limb prosthesis and is designed to replace the functions of the human hand. Terminal devices are available in many shapes, sizes, and designs, each with its own benefits, drawbacks, and specific uses. Passive terminal devices are static, whereas active terminal devices have some type of grasping capability.
Passive Prostheses
The terms passive and cosmetic are often used interchangeably, but they do not have the same meaning. The term passive is a functional description that indicates the terminal device or prosthesis does not have an actively controlled grasping capability. Cosmetic is a visual and aesthetic description indicating the terminal device or prosthesis is visually
appealing or lifelike. A passive prosthesis may or may not be cosmetically appealing depending on its design and purpose. A prosthesis also may contain passive and active elements (eg, a body-powered terminal device with a passive elbow or shoulder).
appealing or lifelike. A passive prosthesis may or may not be cosmetically appealing depending on its design and purpose. A prosthesis also may contain passive and active elements (eg, a body-powered terminal device with a passive elbow or shoulder).
Passive terminal devices include hands, mitts, and devices designed specifically for sports, recreation, or vocation. Specially shaped devices that facilitate targeted activities, such as swimming, playing baseball, or holding a nail, are included in this category because they do not have an active, cable-controlled grasp. Passive terminal devices are lightweight and typically do not require a harness; however, a harness may be needed in high-level amputations for suspension and stability.
Passive hands are available in various sizes, shapes, and configurations (Figures 1, 2 and 3). Many passive hands have bendable or spring-loaded fingers that provide a static grasp when positioned appropriately by the contralateral hand. In some cases, the prosthetist can adjust the force required to open the hand to meet the needs of the patient. The natural appearance, lightweight design, and minimal (or no) harness are appealing to many patients. Most passive hands position the thumb and fingers in opposition, but other designs are available (Figure 3).
Despite lacking an active grasp, passive hands and other cosmetic prostheses can perform many important functions. Patients may use them to support and stabilize objects and to restore some bimanual activities. Utensils, tools, and grooming instruments can be wedged between the fingers and used effectively. The functional extension of the residual limb to anatomic length allows the patient to use the prosthesis to push, pull, carry, hold, and balance objects more easily. One study reported that, for nonmanipulative actions, passive prostheses were used functionally during everyday tasks as frequently as those with an active grasp.2
Active Prehensor Devices
The two primary characteristics to consider when choosing a terminal device with active prehension are the mode of operation and the shape of the device. Body-powered systems have a voluntary-opening (VO) or voluntary-closing (VC) mode of operation or control strategy. These designations refer to the resting state of the terminal device and whether it opens or closes when the user pulls on the control cable.
VO terminal devices are closed at rest, and pulling on the control cable opens the device. Grip strength is a product of the force generated by the rubber bands or springs holding the terminal device closed and remains constant unless the device is held open and modulated by the user. In contrast, VC
terminal devices are naturally open at rest and are pulled closed by the control cable. Grip strength is determined by the amount of tension the user exerts on the control cable, which allows continuously variable grip strength.
terminal devices are naturally open at rest and are pulled closed by the control cable. Grip strength is determined by the amount of tension the user exerts on the control cable, which allows continuously variable grip strength.
![]() FIGURE 4 Photograph of the Sure-Lok voluntary closing locking mechanism. (Courtesy of Fillauer TRS Inc., Boulder, CO.) |
Both strategies have advantages and disadvantages. The grip strength of VO terminal devices must be configured to provide the strongest grasp that the user needs and can repeatedly generate through the harness and control cable. This factor has important implications because every time users open the terminal device they must overcome the full grip strength of the device irrespective of the strength needed for a given task. In addition, when handling delicate objects, users must maintain appropriate tension on the cable to prevent crushing the object within its grasp. These related requirements can lead to fatigue, muscle strain, and compression of the contralateral axilla.
Higher pinch forces can be achieved in VC systems, because they are not limited by rubber bands or springs. The pinch force can be light or strong because it is determined by the user rather than the mechanical design. In addition, the graded prehension in proportion to applied effort may offer greater proprioception than other control mechanisms. Manipulation of delicate items often requires less overall work because the user needs only to maintain sufficient tension to hold an object and can relax the tension without fear of crushing it.
If the VC terminal device does not contain an associated locking mechanism, the user must apply continuous cable tension to maintain grasp. Although this process is normal physiologically, some patients find this requirement objectionable and prefer other terminal devices. This drawback can be addressed with a system such as the Sure-Lok Voluntary Closing Locking Mechanism (TRS). A small switch on the forearm of the unit clamps down on the cable and holds the terminal device in the desired prehensile position (Figure 4).
Although overall power requirements for VC systems may be lower, excursion requirements are greater because, whereas VO systems can be opened only part way with minimal excursion and still be useful for many activities, VC systems require full excursion to closely approximate the opposing grip surfaces in a similar manner. Therefore, care should be taken when prescribing VC systems for patients with more proximal amputations who desire active elbow control. The harness design also must conserve as much excursion as possible. Acceptance for VC terminal devices has been greatest in children and individuals with unilateral transradial amputation, particularly those with long residual limbs.
Members of the rehabilitation team should understand that the choice between a VO and a VC terminal device is not merely a selection of device characteristics. Rather, it will affect the entire mode of operation of the prosthesis across all of the user’s activities.
VO Hooks
The original split-hook design was created in 1912 by David W. Dorrance, an upper limb amputee, to provide active prehension as opposed to the then-traditional, passive C-shaped pirate hook. The split-hook design has two fingers or tines that meet side by side and hold objects between them.
VO hooks vary in construction materials, size, configuration, coating options, and tension mechanisms. An extensive variety of VO hook is available (Figure 5). Although VO hooks were originally made of stainless steel, aluminum hooks have become increasingly common because of their reduced weight and are sufficient for most users. For individuals who require a more durable material than aluminum but find steel too heavy, titanium constructs are available. As material technology and manufacturing improve, hooks are becoming available in composite materials that are lightweight and resistant to corrosion (Figure 6).
Hooks are available in a range of infant to adult sizes. The most common shape is the canted design, which allows users to roll objects into their grasp with good visibility, but this design is less suited to picking up very small objects such as pins (Figure 5, A). An alternative style has a symmetric, rounded interior with lyre-shaped fingers, which are better suited for grasping cylindric objects and picking up small items; however, it can partially obstruct the user’s ability to see what they are manipulating from some angles (Figure 5, B). Because most amputees find the canted approach satisfactory, the lyre shape tends to be more commonly prescribed for individuals with bilateral upper limb amputations for use on the nondominant side
to provide an alternative prehension pattern optimized for cylindric objects. The combination of one canted hook and one lyre-shaped hook offers the individual with bilateral upper limb loss the ability to grasp objects with different shapes.
to provide an alternative prehension pattern optimized for cylindric objects. The combination of one canted hook and one lyre-shaped hook offers the individual with bilateral upper limb loss the ability to grasp objects with different shapes.
A variation on the canted design is the farmer’s hook, characterized by a wider opening than other hooks to facilitate holding shovel handles and similar objects (Figure 7, A). This type of heavy-duty, stainless steel hook is commonly prescribed as a terminal device for adult men who perform manual labor. The specialized fingers have several subtle contours that facilitate holding, grasping, and carrying objects such as buckets, chisels, knives, and carpentry tools. This design is also available with a back-lock feature, which allows the hook to be opened only by a cable pull; the fingers cannot be pried apart. This feature prevents the hook from opening inadvertently when grasping or lifting a heavy load and ensures that the hook remains closed without additional effort from the user (Figure 7, B).
Variation also exists in the gripping surfaces of VO hooks. The most common is a replaceable nitrile coating that lines the inner surface of the hook to increase the tackiness and compressibility of the gripping area (Figure 5, A). Pediatric hooks can be coated with a polyvinyl chloride plastic or covered with removable rubber sheaths to protect the user and the environment from incidental abrasions that occur from rubbing against the hook (Figure 8). In some instances, users prefer uncoated hooks because the gripping surface is less prone to degradation over time (Figure 5, C).
The most common means of creating hook tension is with rubber bands (Figure 5, A through C), although some hooks use springs (Figure 5, D and Figure 6, B). It is generally accepted that one rubber band creates approximately 1.5 lb of grip force. The application of additional or replacement rubber bands is somewhat difficult and is facilitated by a specialty tool; many patients defer this procedure to their treating prosthetist. Tremendous variability exists in the amount of hook tension preferred by an individual user. The desire for increased grip strength must be balanced by the realization that, in VO designs, a patient must overcome the hook’s maximum
grip strength every time the hook is opened, regardless of the grip strength required for the task.
grip strength every time the hook is opened, regardless of the grip strength required for the task.
Alternatively, several variations of adjustable-tension VO hooks are commercially available. Two-load hooks allow the user to choose between two prehensile strengths by positioning a switch at the base of the hook (Figure 9). In a related strategy, the Retro Classic Hook (ToughWare Prosthetics) and the Vari-Pinch Prehensor (V2P; ToughWare Prosthetics; Figure 6) allow the user to choose among several prehensile strengths with knobs or sliders on the underside of the device. In addition to this mechanical adjustment, the Vari-Pinch Prehensor allows the user to exchange elastic bands to further modulate the available grip strength. As in two-load hook designs, these features allow users to maintain a low cable tension when a reduced pinch force is sufficient, with the ability to raise this force when necessary.
VC Hooks
The Grip 3 Prehensor and Adept series (TRS) of terminal devices are unique prehensors available for adults and children in aluminum, steel, and titanium versions with or without a urethane coating. They feature multiple cylindric gripping surfaces within the fingers for gross grasping. Fine prehension is provided by the fingertips (Figure 10). Patient acceptance has been highest among children and sports-minded adults whose primary concern is function.
The Army Prosthetic Research Laboratory (APRL) Hook (Fillauer) is a split hook with lyre-shaped, replaceable aluminum fingers (Figure 11). An internal locking mechanism automatically engages when closed around an object and cable tension is removed. To unlock the grasp and open the hook, the user must apply a pull force greater than was used to close it. The inherent problem with this design is that a user holding a delicate object or another person’s hand must close the hook slightly further to release the grasp. If the user already had a firm grip, it is possible to damage a delicate object or hurt the other person. The user can choose between two possible opening ranges of 0 to 1.375 inches (3.49 cm) or 0 to 3 inches (7.62 cm) by flipping a small switch on the base of the unit. A smaller range permits faster grasp and release and requires less excursion to fully close. Unfortunately, the mechanical complexity of this device makes it costly to manufacture and prone to breakdown.
![]() FIGURE 9 Photograph of the Sierra 2-Load Voluntary Opening Hook. (Courtesy of Fillauer, Chattanooga, TN.) |
![]() FIGURE 10 Photograph of the voluntary-closing Grip 5 Prehensor. (Courtesy of Fillauer TRS Inc., Boulder, CO.) |
![]() FIGURE 11 Photograph of the Army Prosthetic Research Laboratory (APRL) Voluntary Closing Hook. (Courtesy of Fillauer, Chattanooga, TN.) |
The Equilux hook (Toughware) can switch between VO and VC operation. Rotating a lever at the base of the device changes the line of cable pull, allowing the user to choose what strategy to use for each task (Figure 12).
Hands
Although several body-powered hands are available, few are used as active terminal devices. These hands have many drawbacks, including frictional loss of force, glove restriction of motion, limited pinch force, and contours that block visual inspection. These factors substantially limit their usefulness for tasks requiring grasp and release.
Many individuals with recent loss of an upper limb desire an interchangeable hand for social occasions in addition to a utility hook for general use; this request is the most common indication for prescribing a body-powered hand. Hooks require a longer cable length than hands because of their different attachment points, so a user intending to interchange the two must be provided with a hook-to-hand adapter cable that extends the control cable for hook use.
Body-powered hands are rarely appropriate for those with bilateral upper limb loss because of their functional limitations. Externally powered hands offer far greater pinch force and improved grasp-release function and are preferable when maximum prosthetic hand function is required.
Most cable-operated hands have the thumb and the first two fingers moving in a three-jaw chuck prehension pattern (Figure 13, A). Often, the metal structure of the three fingers is covered by a plastic hand shell (Figure 13, B). These first three fingers open and close the hand shell, and the fourth and fifth fingers move passively with the others. Some designs have a solid outer layer with three to five moving digits when the hand opens and closes (Figure 13, C).
Body-powered hands are heavier, less versatile for handling objects, and block the user from seeing the object during manipulation. They cannot fit into pockets or grasp buttons and zippers. The three-jaw chuck grip pattern positions the thumb to line up between the first two fingers, but is not directly opposed to either one. This makes it much more difficult to pick up small objects because the thumb and first finger do not meet to form a stable pinch surface.
Body-powered hands are less efficient than hooks because of frictional energy losses in the hand mechanism, so an equivalent amount of input force results in a lower output pinch force. As a result, both VO and VC hands require more power to operate than VO or VC hooks. A few studies have compared activation forces and efficiency and found that hooks outperform hands in most instances.3,4 Most VO hooks obtain a pinch force of more than 20 N, with the ability to generate a greater force with the addition of rubber bands. None of the hands achieved a grip force greater than 18 N, and most forces were less than 15 N. The gloves used to cover the hands further increase the effort required for operation.3 VC hands were also found to be inefficient, because the substantial frictional losses during hand operation require increased activation force and work by the user.4
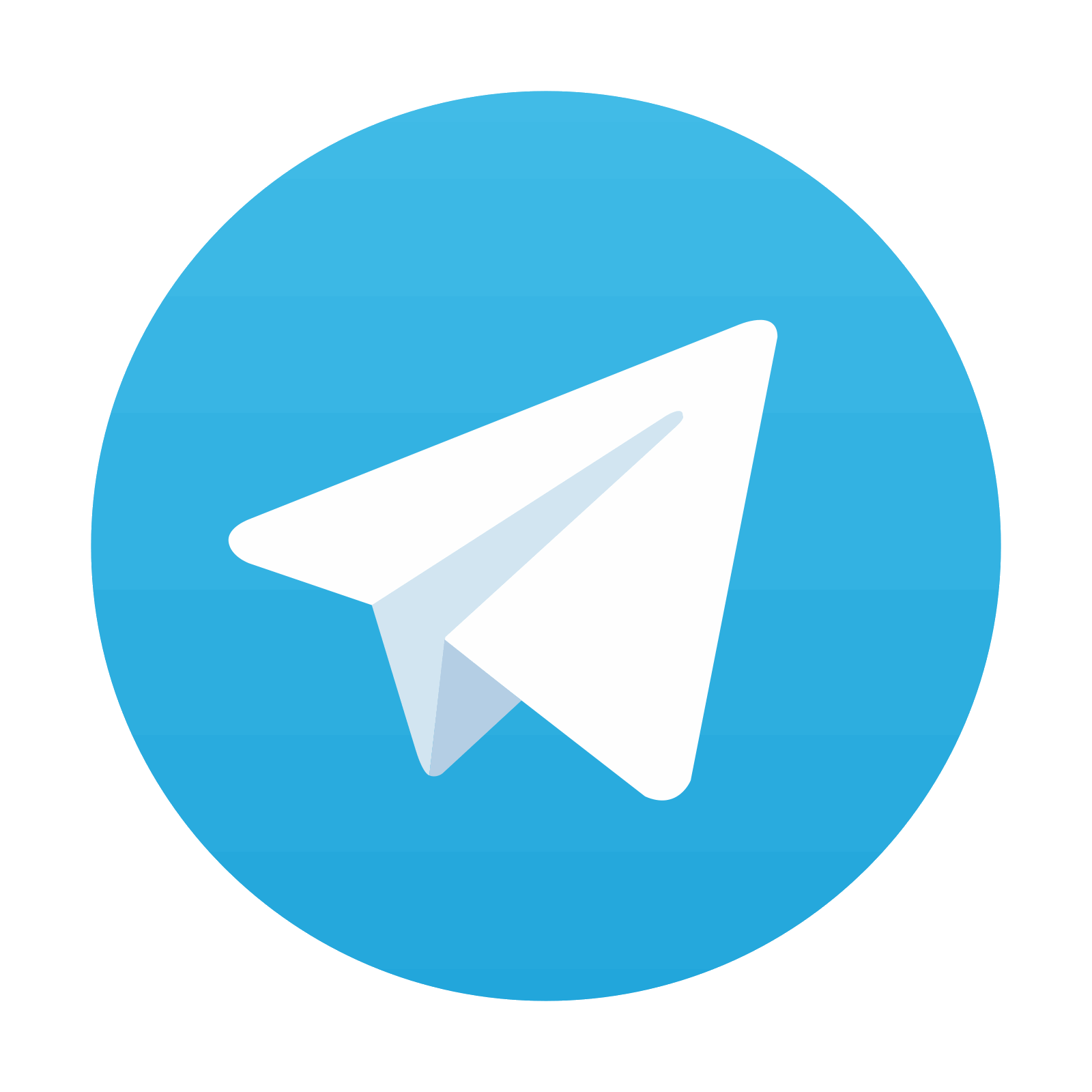
Stay updated, free articles. Join our Telegram channel
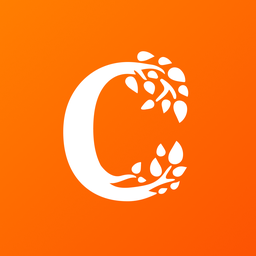
Full access? Get Clinical Tree
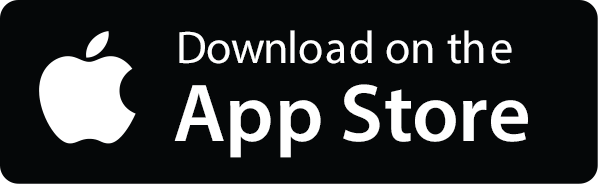
