Prosthetic Knee Mechanisms
Matthew J. Major PhD
Phillip M. Stevens MEd, CPO, FAAOP
Neither of the following authors nor any immediate family member has received anything of value from or has stock or stock options held in a commercial company or institution related directly or indirectly to the subject of this chapter: Dr. Major and Phillip M. Stevens.
ABSTRACT
The purpose of prosthetic knee mechanisms is to simulate the functions of the absent knee joint during standing, walking, and transfers. Safe, efficient ambulation is accomplished by facilitating stability when the limb is loaded and achieving adequate and timely ground clearance of the prosthesis during swing. For mechanically passive prosthetic knees, stance limb stability is accomplished through mechanical locks and geometric designs that aid in generating knee extension moments. For single-speed walkers, swing phase knee resistance is limited to simple friction-based mechanisms. For walkers capable of variable speed ambulation, the use of hydraulic resistance permits a range of knee resistance values that adapt to different walking speeds. Microprocessors regulate knee flexion resistance in both swing and stance, with resultant benefits of safety, stability, and reduced cognitive loads of ambulation. The field continues to explore the benefits and realization of powered prosthetic knees that generate knee extension and/or flexion through either automatic means or direct muscle control.
Keywords:
knee; lower limb prosthesis; microprocessor-controlled knee; stance control; swing control
Introduction
Modern prosthetic knee mechanisms are often characterized in terms of their joint configuration, their means of mechanical stability in stance, and their means of swing phase flexion/extension resistance. Joint configurations are characterized as either single axis or polycentric. Mechanical stance stability occurs through various locking mechanisms or geometrically favorable joint designs. This mechanical stability can be supplemented by yielding hydraulic resistance mechanisms. Swing phase flexion/extension resistance occurs through simple constrained frictional elements or more adaptive hydraulic resistance. Microprocessors are now able to govern knee resistance values in both stance and swing.
Knee selection is based on the needs of the user with respect to their ability to actively stabilize the knee in stance and their capacity to walk at variable speeds. Users with relatively short limb length, reduced hip extensor strength, or limited experience with prosthetic ambulation are more reliant on the mechanical stability afforded by certain mechanisms. Users capable of ambulation across a range of walking speeds benefit from the added cost and weight of knee designs with hydraulic cylinders, whereas those confined to a single walking speed in household environments may be well served by lighter, simpler knees. Microprocessors capable of adapting knee resistance values in both stance and swing are increasingly recognized for the added safety and stability they provide during prosthetic mobility.
Prosthetic Knee Concepts
The prosthetic knee mechanism serves to restore the lost functions of the anatomic knee joint and is responsible for facilitating safe and smooth ambulation for individuals with limb absence at or proximal to the knee. During standing, the knee mechanism is meant to provide adequate support and resist collapsing when loaded. Safety during walking is more involved as optimal knee flexion resistance values cycle with the cadence of ambulation. During stance, the knee must maintain limb stability to prevent buckling and, ideally, permit the initiation of knee flexion in preswing to prepare for the transition into the swing phase. During swing, knee flexion characteristics are designed to avoid collisions between the prosthetic foot and the ground to prevent stumbles and trips. Furthermore, knee resistance values must be low enough in terminal swing to permit full knee extension in preparation for the transition into the stance phase.
These goals are opposed with respect to optimizing the sagittal alignment of
the knee beneath the socket. In consideration of the demands placed on the user in controlling their prosthetic limb, a more posterior alignment facilitates stance stability but compromises the ease of initiating swing phase flexion. By contrast, a more anterior alignment facilitates an easier initiation of swing phase flexion but reduces stance phase knee stability. Thus, alignment decisions must balance the divergent needs of a given patient while considering the mechanical performance characteristics of a given knee mechanism.
the knee beneath the socket. In consideration of the demands placed on the user in controlling their prosthetic limb, a more posterior alignment facilitates stance stability but compromises the ease of initiating swing phase flexion. By contrast, a more anterior alignment facilitates an easier initiation of swing phase flexion but reduces stance phase knee stability. Thus, alignment decisions must balance the divergent needs of a given patient while considering the mechanical performance characteristics of a given knee mechanism.
To achieve the stance phase goal of stability, prosthetic knee users must manage the flexor-extensor moments of the knee mechanism. The knee moment is a function of the magnitude of the ground reaction force vector and its line of action relative to the prosthetic knee center of rotation in the sagittal plane (ie, lever arm).1,2 The optimal position of the prosthetic knee relative to the residual hip joint is defined by the design of the knee mechanism and optimized by a prosthetist during clinical fitting of the prosthetic knee-ankle-foot system.1 For knees with greater inherent stability, such as certain polycentric knees or microprocessor knees (MPKs), more dynamic alignments can be considered. In the absence of inherent prosthetic knee stability, safer alignments with the knee positioned more posteriorly beneath the socket must be considered. The biomechanical phenomenon of controlled knee flexion in early stance is pursued by some users of certain prosthetic knee joints that permit this feature and will be discussed later in the chapter.
During early stance, prosthetic knee users must prevent knee buckling and facilitate limb stability by maintaining a knee extension moment. This knee extension moment is achieved by positioning the ground reaction force vector anterior to the knee center of rotation.1,3,4,5 The user must then smoothly transition from an extension moment to a flexor moment to initiate knee flexion during preswing.2 Importantly, the position and orientation of the ground reaction force vector changes as the user advances over the prosthetic foot and is influenced by the foot’s mechanical properties, prosthesis alignment, and selected footwear.2
To achieve swing phase goals, prosthetic knee users must carefully control the swing mechanics of the prosthetic limb to manage its global position and timing through a smooth arc of motion. Specifically, the effective length of the prosthetic limb must be shortened to provide adequate foot clearance and avoid contact of the heel or toe with the ground, and then it should be lengthened during terminal swing into full extension to prepare the limb for ground collision at stance phase initial contact.6 The action of leg shortening is a function of the prosthetic knee joint design, the prosthetic ankle-foot mechanism and alignment, and volitional control of linear and angular position of the hip joint.6,7,8,9,10 Given its relatively large range of motion, knee joint flexion is the primary contributor to limb shortening and providing sufficient foot clearance through midswing.6,7 Thus, the prosthetic knee mechanism and its knee flexion/extension resistance values are critical to consistent swing phase clearance. These values will directly influence both angular positions and rates of change of the prosthetic shank at the knee, and hence the type and magnitude of compensatory dynamics employed by the user.
To accomplish these subtasks of stance and swing, a prosthetic knee user will directly modulate knee moments through compensation strategies. In stance these include their control of the trunk position and regulation of extensor and flexor moments of the residual hip joint.1,3,4,5,11 In swing this may entail some combination of prosthetic limb circumduction, contralateral limb vaulting, ipsilateral hip hiking, and residual hip control.9,10,12,13 Successful prosthetic knee control is therefore dependent on appropriately timed and sufficiently strong hip moments and would be affected by walking speed.4,11,14 Given these varied compensation strategies, evidence suggests that prosthetic knee users exhibit greater demands on the sound limb relative to persons with transtibial level limb loss,5,14,15 which could place them at greater risk of overuse injury and secondary musculoskeletal trauma of the sound limb.16
The amount of active control and compensation required by the user to ambulate with a prosthetic knee is highly dependent on their physical capacity for ambulation, their anticipated walking environments and activities, and the mechanical design of the knee mechanism itself.
Mechanically Passive Knee Joints
Knee Resistance Mechanisms: Friction Versus Fluid
Although variations in prosthetic knee options abound, the provision of resistance to knee motion is obtained through two common approaches. The simplest method of delivering resistance is constant friction. With constantfriction knees, the clinician can often easily adjust the friction resistance acting about the joint within the clinic. A limitation of constant-friction knees is that, once set by the clinician, the level of resistance is optimized for a single, generally slower gait speed. Walking faster will create excessive knee flexion in swing phase, prolonging this phase of gait because the user must wait for the knee to reach full extension in terminal stance. Walking slower will reduce the momentum of the knee into swing phase flexion and create quick, halting steps.17 Accordingly, constantfriction knees are generally reserved for limited walkers who ambulate at a single, relatively slow speed and who are not functionally constrained by the performance limitations of the knee unit.
In contrast, fluid-controlled knees are capable of providing variable resistance across a modest range of walking speeds. Fluid-controlled knees use pneumatic or hydraulic cylinder configurations to dampen knee motion. With over half a century of regular use in prosthetic rehabilitation, it is well established that fluid-controlled knees provide a smoother, more normal swing phase movement than knees with mechanical friction.17,18,19 Because of the nature of hydraulic resistance in which greater external forces are met
with greater resistance, fluid control will automatically adapt knee resistance levels according to changes in the user’s walking speeds. For that reason, they are indicated for those capable of walking at different speeds.
with greater resistance, fluid control will automatically adapt knee resistance levels according to changes in the user’s walking speeds. For that reason, they are indicated for those capable of walking at different speeds.
Choosing between pneumatic and hydraulic fluid control begins with an understanding of their compressibility. Gases are readily compressible, whereas liquids are not. The compressibility of the gases in a pneumatic knee requires a specific cylinder volume to provide adequate swing phase resistance through this medium. By contrast, the incompressibility of hydraulic fluids means that a smaller volume is needed to provide effective swing phase control. As a result, hydraulic knees can be both smaller and lighter than their pneumatic equivalents. In addition, their incompressibility allows hydraulic cylinders to accommodate a broader range of gait speeds.
Finally, pneumatic control is unable to deliver adequate knee flexion resistance to provide stance phase stability. Only the incompressibility of hydraulic fluid is capable of providing sufficient stance control to prevent limb collapse, typically in the form of a slowly yielding resistance to sudden knee flexion, as pioneered by Mauch in the 1950s,20 which can aid stumble recovery. That the Mauch knee concept is still widely used and copied in modern prosthetic rehabilitation supports the clinical effectiveness of fluid-controlled prosthetic knee mechanisms (Figure 1).
Single-Axis Constant-Friction Knee
Consistent with its name, the single-axis constant-friction knee represents a basic hinge design that allows the knee joint to bend during the swing phase of gait. Various design mechanisms provide an adjustable friction-based dampening of knee flexion, commonly through a turn screw. Because of their relative mechanical simplicity, such knees represent a lightweight, low-cost, durable knee option. However, as described previously, these joints are generally reserved for users who walk at a single, reduced, fixed cadence (Figure 2). Although the adjustable friction provides a measure of customizability to the swing characteristics of the knee, the shank of the prosthesis largely functions as a passive pendulum with a swing rate determined by its length.21 The slower walking speeds mandated by this knee can be frustrating to those users otherwise capable of faster, variable cadences. In addition, recent data have suggested that, although higher swing phase knee flexion resistance can generate earlier swing phase knee extension and improve swing time symmetry, it does so at the cost of smaller and earlier minimum toe clearance. Thus, improvements in swing symmetry are accompanied by an increased risk of insufficient toe clearance in swing.6 In the United States, Medicare recognizes the single-axis constant-friction knee as the most basic prosthetic knee option, suitable for individuals with limited walking abilities. Exceptions to this standard application may be found in settings where the knee is chosen because of extreme financial constraints, the knee is preferred because of its simple durability, or in limited pediatric applications when size restrictions preclude the use of alternatives.
![]() FIGURE 1 Photograph of a single-axis knee where both stance and swing knee resistance values are regulated by a hydraulic cylinder. (Courtesy of Össur.) |
Importantly, although constant friction provides a measure of resistance to swing phase knee flexion, it provides no restriction to stance phase knee flexion. In the absence of any inherent knee stability as found in most alternative knee mechanisms, every step must be carefully controlled through the user’s active hip extension. Although contradictory to their indication for more limited ambulators, management of these knees may be unrealistic for prosthesis users who lack the necessary strength and control of their hip extensors, such as frail walkers. Applying a relatively posterior alignment of this knee joint beneath the socket will provide a measure of knee stability through encouraging an external knee extension moment, but it increases the hip flexion demand to initiate knee flexion in late stance to transition into prosthetic swing phase.
Weight-Activated Stance Control
One solution to the lack of inherent knee stability attributed to single-axis constant-friction knees has been engineered in the form of weight-activated stance control (WASC). In such systems, a friction brake mechanism is applied to the prosthesis during stance to augment knee stability (Figure 3). When engaged, this adjustable supplemental friction prevents knee flexion and eliminates the risk of knee buckling during standing and walking. This knee mechanism is sometimes considered for use in the initial prosthesis of a patient with limited ambulatory potential.
However, the typical weight-activated friction brake is associated with an important biomechanical limitation. Specifically, the knee does not release to allow flexion until the prosthesis is fully unloaded. This condition is problematic because it precludes the normal knee flexion that should occur during the preswing phase of gait and appears to reduce walking speed relative to other alternatives.22 This limitation also renders the traditional WASC knee unusable in bilateral applications because the user is unable to fully offload both knee units to flex the knees and obtain a seated posture. As a result, this component is largely reserved for users of unilateral transfemoral prostheses with a slow, shuffling gait.
More recently, limited variants of the traditional WASC knee have been designed to release their friction braking mechanism under weight-bearing loads when the knee reaches full extension. The automatic stance phase lock knee joint represents another alternative of comparative simplicity, cost, and durability. Unlike traditional WASC knee units, the automatic stance phase lock is unlocked by the loading of the forefoot in terminal stance, allowing earlier knee break to prepare for transitioning into swinging the limb forward.23,24
Polycentric Knees
Polycentric knees are readily differentiated from simpler single-axis knees by their multiple points of articulation. Among these, the four-bar design is most common, characterized by four articulations connected by four linkage bars (Figure 4). Polycentric knees offer several biomechanical advantages over both single-axis constant-friction and WASC knees, and as a result, they have become increasingly popular. In contrast to the friction breaking mechanisms of the WASC knee, the inherent stability of polycentric knees is found in the geometry of their variable instantaneous center of rotation (ICOR). The ICOR represents the functional center of rotation of the knee at a given knee flexion angle. Unlike the single-axis knee, where the center of rotation can only be positioned at the knee axis, in polycentric configurations the ICOR is often located outside the knee mechanism itself. Specifically, when the polycentric joint is straight or nearly straight, the ICOR is positioned proximal and posterior to the joint itself (Figure 5).
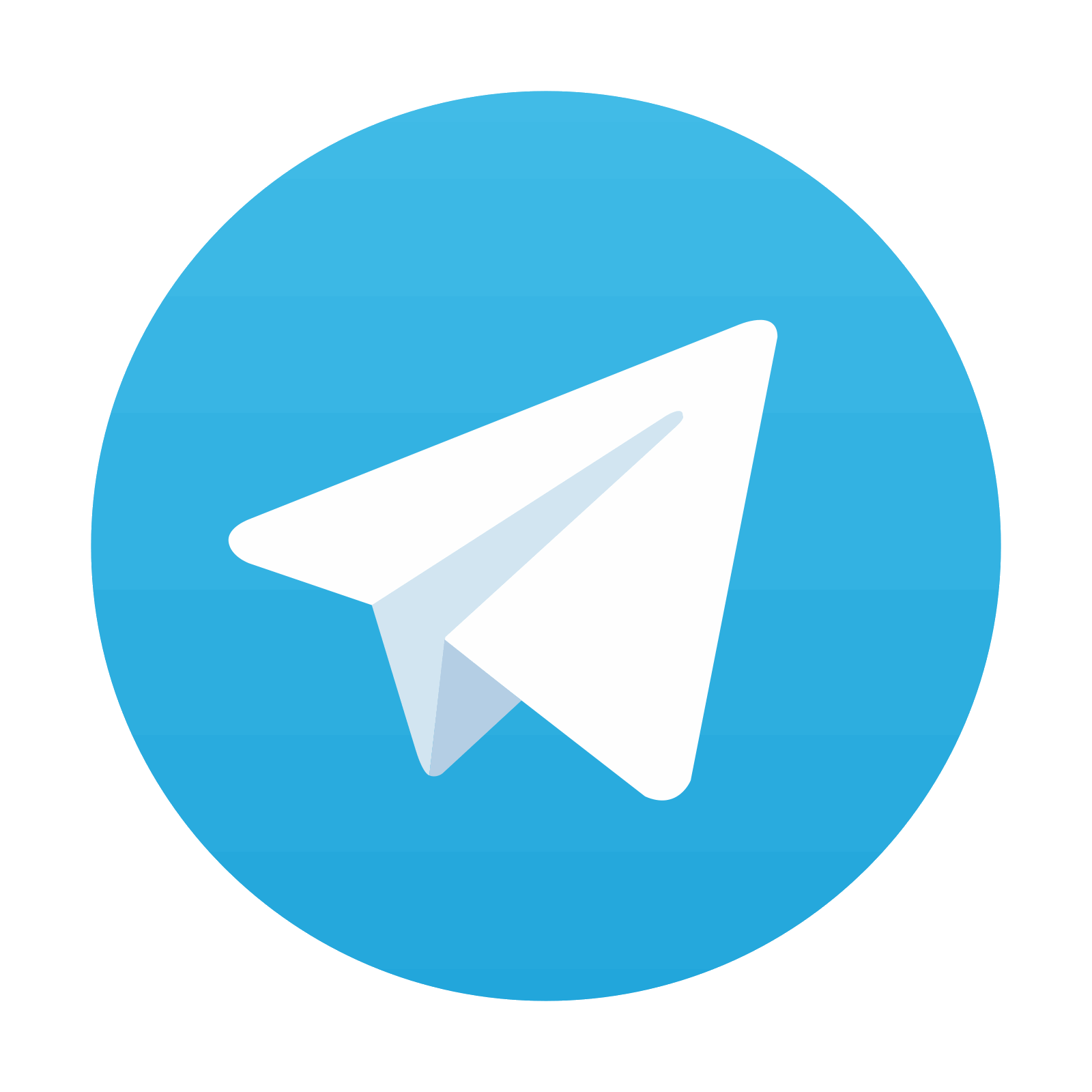
Stay updated, free articles. Join our Telegram channel
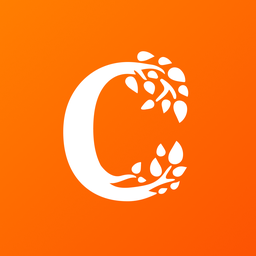
Full access? Get Clinical Tree
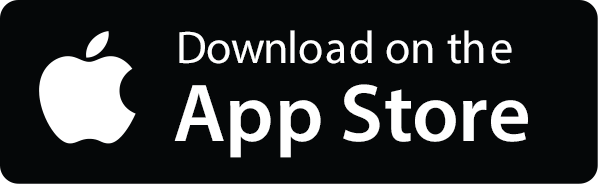
