Prosthetic Foot and Ankle Mechanisms
Matthew J. Major PhD
Phillip M. Stevens MEd, CPO, FAAOP
Neither of the following authors nor any immediate family member has received anything of value from or has stock or stock options held in a commercial company or institution related directly or indirectly to the subject of this chapter: Dr. Major and Phillip M. Stevens.
ABSTRACT
The purpose of prosthetic foot and ankle mechanisms is to simulate the functions of the absent foot and ankle during standing, walking, and transfers while modulating the impacts of ground reaction forces at the interface of the residual limb and the prosthesis. For passive-elastic prosthetic feet, this is accomplished through the consideration and manipulation of mechanical stiffness, dampening characteristics, and energy efficiency. Localized movement can be facilitated through mechanical joints with the extent of that movement modulated by elastomeric bumpers or fluid resistance. Fluid resistance can be regulated in real time in microprocessor-controlled feet. The field continues to explore the benefits and realization of powered propulsion in prosthetic foot and ankle mechanisms.
Keywords:
dynamic response; foot; hydraulic ankle-foot; lower limb prosthesis; microprocessor foot
Introduction
Modern prosthetic foot mechanisms are often characterized in terms of their mechanical stiffness. The level of prosthetic foot stiffness will affect the user’s walking experience and their mobility outcomes, as stiffer feet will deform less under the same load. In general, compliant materials are used in prosthetic feet designed for more reserved walkers, whereas stiffer materials with greater energy storage potential are preferred by more dynamic walkers. Localized movement can be facilitated at mechanical ankle joints and can be modulated by compressible elements or fluid resistance. In the case of the latter, onboard sensors can inform a centralized microprocessor of the need to modulate ankle joint stiffness in real time according to environmental cues. Externally powered ankle mechanisms are now commercially available with ongoing efforts to identify ideal programming parameters, means of actuation, and patient candidates.
Passive-Elastic Prosthetic Foot Concepts
In the effort to restore the lost function provided by the anatomic foot and ankle, the primary role of a prosthetic foot-ankle mechanism (referred to as simply foot through the balance of this chapter) is to support a patient user during weight-bearing activities such as standing, walking, and transitioning. For standing, the prosthesis must adequately support some or all of a user’s body weight while providing an adequate base of support to accommodate fluctuations in the plantar center-of-pressure position during postural sway. For walking, the principal objectives of the prosthesis are to (1) accommodate energy absorption during load acceptance in early stance, (2) adapt to the ground surface by achieving a stable foot position following initial contact, (3) provide close-to-normal shank kinematics during center-of-pressure progression by replicating the loaded rollover geometry of the anatomic ankle-foot complex, and (4) contribute to late stance push-off and facilitating limb transition into the swing phase.1 As required during transitions from standing to walking or seated to standing and vice versa, the prosthetic foot provides a structural element to transfer ground forces to the proximal components. Consequently, the user experience and mobility outcomes will be intimately linked to the inherent mechanical function of a prosthetic foot.1,2
For a passive-elastic prosthetic foot, the function is dictated by its mechanical properties, namely stiffness and damping.3 The amount of deformation that a prosthesis experiences under load is a function of its stiffness, which for modern feet will vary throughout the structure and is typically nonlinear.1 Therefore, the deformation of the prosthetic foot is dependent on the region (eg, heel, keel) being loaded, and the orientation and magnitude of the applied force. By association, because of their passive-elastic nature, the same factors will also determine the amount of both the energy stored and the energy dissipated by a prosthetic foot. Importantly, as with any passive-elastic
spring, the amount of energy return will not exceed the energy stored and is ultimately dependent on the unloading of the prosthesis. Consequently, although a prosthetic foot may possess excellent energy efficiency, meaning it returns a relatively high percentage of the energy stored, that energy return may not be provided in full or at the right moment in the gait cycle because of a user’s unique gait dynamics or the design of the foot. Advancements in materials science have played a pivotal role in the evolution of prosthetic feet, in which passive-elastic materials can range from foams to carbon fiber-reinforced plastics and fiberglass composites. These materials offer tremendous flexibility to prosthesis design and their corresponding mechanical properties, thereby accommodating a wide range of users with different activity levels and lifestyles.
spring, the amount of energy return will not exceed the energy stored and is ultimately dependent on the unloading of the prosthesis. Consequently, although a prosthetic foot may possess excellent energy efficiency, meaning it returns a relatively high percentage of the energy stored, that energy return may not be provided in full or at the right moment in the gait cycle because of a user’s unique gait dynamics or the design of the foot. Advancements in materials science have played a pivotal role in the evolution of prosthetic feet, in which passive-elastic materials can range from foams to carbon fiber-reinforced plastics and fiberglass composites. These materials offer tremendous flexibility to prosthesis design and their corresponding mechanical properties, thereby accommodating a wide range of users with different activity levels and lifestyles.
Regarding design, the passive-elastic structures in prosthetic feet can assume different shapes. Although heels and keels of prosthetic feet can often be considered cantilever springs, integrated (Figure 1) or modular pylons (Figures 2 and 3) are akin to linear or rotational springs. Their mechanical properties and hence loaded behavior are then a function of structural design details, including geometry, attachment, and preloading. The decision to incorporate passive-elastic structures as opposed to rigid, noncompliant materials within a design will dictate where the prosthesis deforms and by how much. One way to increase localized degree-of-freedom range of motion is to incorporate articulations or prosthetic joints such as an ankle pivot (Figure 4). Ankle joints can serve to increase sagittal and/or coronal plane range of motion, whereas certain pylon adaptors can increase axial absorption and transverse plane torsional range of motion. Although these articulated prostheses may seem distinct from their nonarticulated counterparts, it is important to acknowledge that the mechanical behavior of articulations is still dependent on passive-elastic principles. Normally these articulations are not simply free hinges, but their range of motion is often controlled through viscoelastic elements, such as bumpers (Figure 4). Loaded deformation in any anatomic plane can be achieved through either articulations or continuous structures of solid composite materials. Strategic cutouts in continuous structures can further increase range of motion (Figure 1). Therefore, based on structural design, prostheses that incorporate articulations can behave similarly to those without such articulations. Thus, their user-independent mechanical function is more relevant to a patient’s experience than their inherent design details. For instance, keel or heel deformation, whether through compression of a solid composite or articulation, can simulate dorsiflexion and plantar flexion, respectively.
![]() FIGURE 1 Photograph of a carbon fiber dynamic elastic response foot with an integrated carbon pylon. The split keel enables multiaxial compliance. (Courtesy of Fillauer, Chattanooga, TN.) |
Nonarticulated Dynamic Response Prosthetic Feet
The design and function of nonarticulated prosthetic feet have benefitted greatly from advancements in material
science. The Solid Ankle Cushion Heel (SACH) foot is the earliest version of these types of feet and perhaps the most well known given its history and the widespread use of its design concepts. As the name implies, the SACH foot is designed with a compliant heel that deforms with load at initial contact to store and dissipate energy (Figure 5). The heel typically occupies a third of the plantar surface and is often made from an open-cell foam. The user transitions from the heel as they advance over the prosthetic limb onto a rigid keel and eventually a compliant toe section to facilitate late stance rollover. These types of feet remain relevant in resource-limited environments because of their simple design, low cost, and durability. However, these features also make this design applicable as a basic prosthesis for individuals with limited mobility. The compressible heel can facilitate load acceptance following limb collision, and the relatively rigid keel4 can act to limit prosthesis keel deformation to aid in stability during standing and walking. Because there is a rapidly expanding selection of prosthetic feet, modern prostheses tend not to incorporate this type of foot and so their use is becoming more limited.
science. The Solid Ankle Cushion Heel (SACH) foot is the earliest version of these types of feet and perhaps the most well known given its history and the widespread use of its design concepts. As the name implies, the SACH foot is designed with a compliant heel that deforms with load at initial contact to store and dissipate energy (Figure 5). The heel typically occupies a third of the plantar surface and is often made from an open-cell foam. The user transitions from the heel as they advance over the prosthetic limb onto a rigid keel and eventually a compliant toe section to facilitate late stance rollover. These types of feet remain relevant in resource-limited environments because of their simple design, low cost, and durability. However, these features also make this design applicable as a basic prosthesis for individuals with limited mobility. The compressible heel can facilitate load acceptance following limb collision, and the relatively rigid keel4 can act to limit prosthesis keel deformation to aid in stability during standing and walking. Because there is a rapidly expanding selection of prosthetic feet, modern prostheses tend not to incorporate this type of foot and so their use is becoming more limited.
A now more common nonarticulated, passive-elastic prosthetic foot of which there are many different designs is the dynamic (elastic) response foot, also known as flexible keel (Figure 6) or energy storage and return feet (Figures 1 and 7). A caveat here is that all passive-elastic prosthetic feet, even including the SACH foot, will store and return some amounts of energy given the viscoelastic properties of the materials used to construct these prostheses and their constituent parts.4 The combined elastic and viscous characteristics dictate the amount of energy stored and returned when loaded and unloaded at a given rate, thereby generating the characteristic hysteresis curve of instantaneous force versus displacement that describes features of stiffness and energy efficiency (Figure 8).
![]() FIGURE 5 Photograph showing a cross-section view of a Solid Ankle Cushion Heel foot with its compressible foam heel and rigid wooden keel. |
Although the design specifics, including structural elements, materials, and geometry, might vary across dynamic response feet, they are typically composed of keel and heel cantilever elements (blades) of a material with relatively high levels of strength and energy efficiency (eg, carbon fiber-reinforced plastics and fiberglass composites) (Figures 1 and 7). One primary advantage of using these
materials is that the prosthesis can store and return greater amounts of energy upon unloading, which would theoretically be advantageous for assisting with prosthetic limb push-off. However, again, this push-off assistance would be dependent on returning energy at the correct time. The material flexibility and structural design, and hence mechanical properties, of such blades allow these feet to accommodate a wide range of users according to their stature, weight, and activity level. Regarding the structural design of keel blades, they can either be of a solid element (Figure 7) or split toe (Figure 1) to increase coronal plane compliance and hence range of motion to accommodate movement in that plane. Furthermore, although traditional dynamic response feet have only one keel blade, embodiments exist that have included multiple stacked blades that engage after some load threshold to increase stiffness (Figure 9).
materials is that the prosthesis can store and return greater amounts of energy upon unloading, which would theoretically be advantageous for assisting with prosthetic limb push-off. However, again, this push-off assistance would be dependent on returning energy at the correct time. The material flexibility and structural design, and hence mechanical properties, of such blades allow these feet to accommodate a wide range of users according to their stature, weight, and activity level. Regarding the structural design of keel blades, they can either be of a solid element (Figure 7) or split toe (Figure 1) to increase coronal plane compliance and hence range of motion to accommodate movement in that plane. Furthermore, although traditional dynamic response feet have only one keel blade, embodiments exist that have included multiple stacked blades that engage after some load threshold to increase stiffness (Figure 9).
Physical principles dictate that given the opportunity for greater deformation the energy storage capacity of a keel shares a positive relationship with its length. In other words, a longer keel with greater build-height can potentially store more energy than a low-profile design of the same material. The first generation of energy-storing feet was characterized by shorter build-heights (referred to by some as flex-walk systems) and continue to find application where special constraints preclude the use of taller feet5 (Figure 7). Second-generation energy-storing feet elongated their build-heights with longer springs that acted as integrated pylons to enable additional deformation and associated energy storage (referred to by some as flex foot systems) (Figure 1). In subsequent development efforts, the integrated pylon segments of such feet have been engineered to allow vertical deflection (referred to by some as a shank foot system with vertical loading pylon) (Figure 10). In response to external policy influences, vertical deflection has been increasingly localized to discrete shock-absorption mechanisms (Figure 11).
Given the flexibility in design afforded with dynamic response feet, the crossover foot is a relatively new type of foot meant to accommodate both walking and running for higher activity users (Figure 12). This particular foot type incorporates design elements of running-specific feet, including a carbon fiber keel blade that extends to the socket, and elements of dynamic response feet for walking, including a heel element for initial contact of the limb. These combined features enhance utility of these feet by offering energy storage and return for running through their keel design while providing a heel to support heel-to-toe rollover during walking and a stable base of support for standing. Consequently, this design can offer users access to a single foot for engaging in a range of ambulatory activities without the cost and burden of swapping between feet.
Evidence suggests that these feet are preferred over traditional dynamic response feet by moderate to active ambulators, who also demonstrated improvements in mobility, balance confidence, and satisfaction with these designs.6
Evidence suggests that these feet are preferred over traditional dynamic response feet by moderate to active ambulators, who also demonstrated improvements in mobility, balance confidence, and satisfaction with these designs.6
![]() FIGURE 10 Photograph of a carbon fiber dynamic elastic response foot engineered with multiaxial compliance and vertical shock absorption. (Courtesy of Ottobock.) |
![]() FIGURE 11 Photograph of a carbon fiber dynamic elastic response foot with a discrete mechanism engineered for axial torsion and vertical shock absorption. (Courtesy of Ottobock.) |
Evidence from classic comparative studies has suggested improved clinical outcomes when walking with dynamic response feet compared to the SACH foot design. These outcomes include increased walking velocity,7,8 increased stride/step length,8,9,10 increased step length symmetry,10 improved rollover and shank progression control,11,12 lower sound limb loading,8,9 and increased push-off power at faster walking speeds.10,13,14 Notably, there has been inconclusive evidence regarding differences in metabolic energy demands during self-selected walking on level ground, but some suggest that dynamic response feet display improved outcomes at higher walking speeds and gradients.7,12,15 More recently, there has been some limited evidence to suggest that users may demonstrate greater walking speed, stride/step length, prosthesis power generation, and prosthesis-related quality of life when using a fiberglass dynamic response foot compared with carbon fiber.16 Given these superior outcomes, improved designs, and now vast selection of dynamic response feet to accommodate a range of users, SACH foot designs are less commonly used in modern prostheses.
Articulated Dynamic Response Prosthetic Feet and Shock-Absorbing Pylons
Although dynamic response prosthetic feet with continuous structures can be cleverly designed to provide varying levels of range of motion when under load, the incorporation of articulations is a common design technique to strategically increase regional motion. The single-axis prosthetic foot design includes an ankle joint articulation to provide additional sagittal plane rotation, or effectively plantar flexion and dorsiflexion (Figure 4). In commercial single-axis feet, the motion provided by the ankle joint is typically regulated through viscoelastic bumpers that act as springs to resist rotation. One primary function of this joint is that it allows the entire foot structure distal to the articulation to rotate into plantar flexion at initial contact to achieve foot flat akin to anatomic function. Nonarticulated feet will still achieve some level of foot flat because of heel compression and/or the shank deformation, but the single-axis foot will in most cases display quick rotation of the foot at initial contact17 to allow the forefoot structure to meet with the ground.18 In this way, the ground reaction force vector, and hence center of pressure, quickly progresses anteriorly from initial contact as opposed to stalling at the posterior end in nonarticulated feet because of heel deformation. As tibial progression continues, the ankle can enter into dorsiflexion that is limited by another bumper element to further advance the ground reaction force vector toward the keel end, thereby sustaining an increasing knee extension moment. Overall, these features may be advantageous for users who lack sufficient stance stability and could benefit from early foot flat and knee control. However, a noted disadvantage of this design is that although the center of pressure is able to advance quickly following initial contact, it may stall near the ankle joint until the tibia advances to allow for dorsiflexion. The seemingly less constrained ankle motion and unique progression of the center of pressure during stance could work to disrupt a user’s forward advancement.18
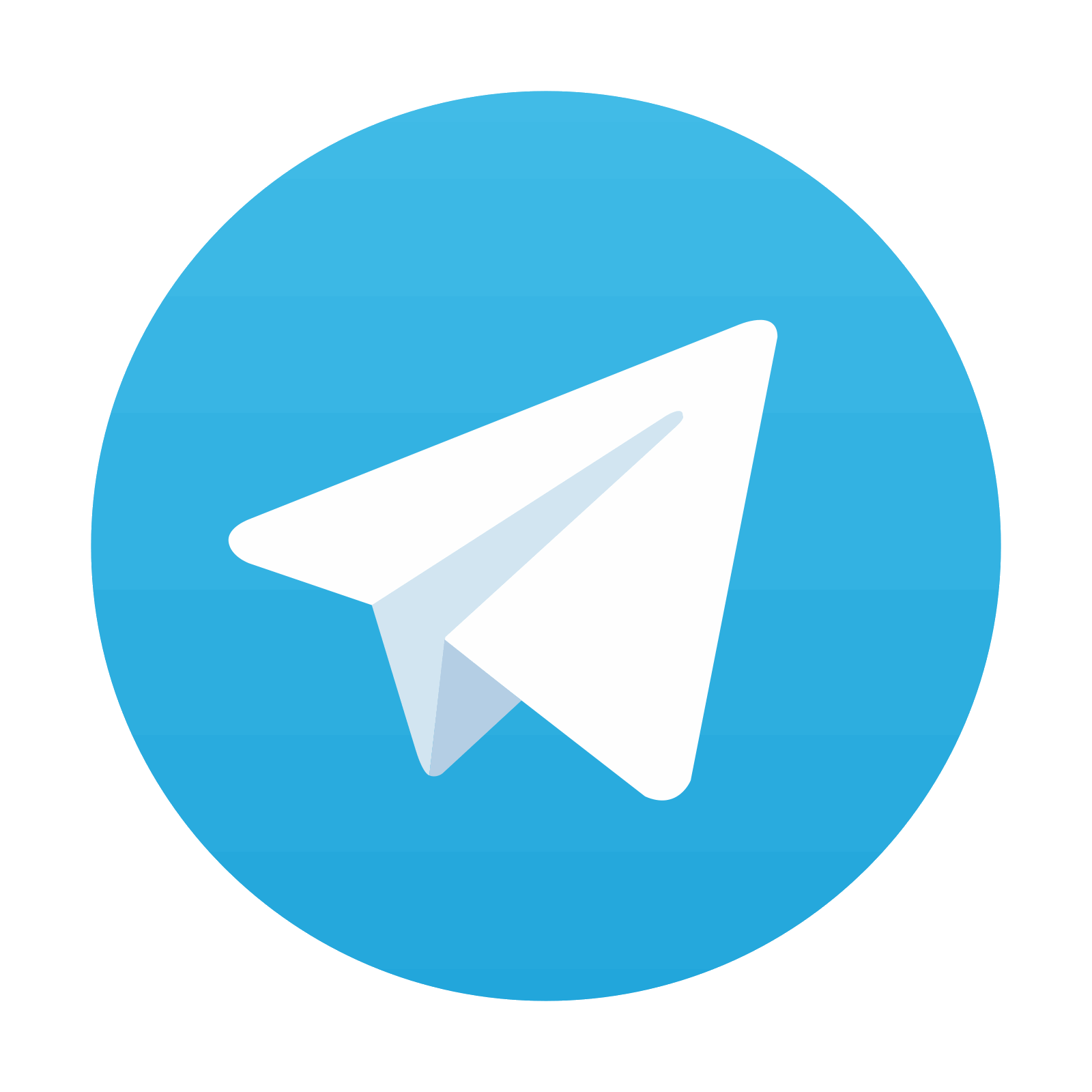
Stay updated, free articles. Join our Telegram channel
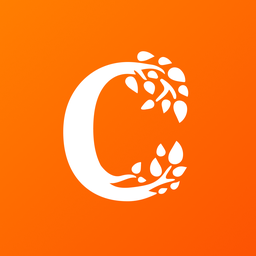
Full access? Get Clinical Tree
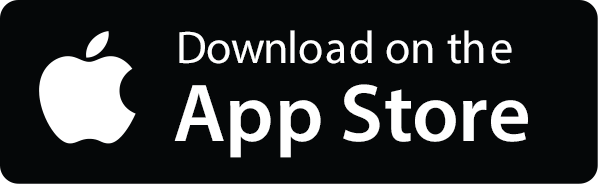
