Harnessing and Controls for Upper Limb Body-Powered Prostheses
David B. Rotter CPO
David B. Rotter or an immediate family member serves as a board member, owner, officer, or committee member of the Association of Children’s Prosthetic and Orthotic Clinics.
ABSTRACT
Body-powered prosthetic devices are an effective method of controlling upper limb prostheses. Body-powered prostheses use body movements, which are captured with control straps and cables, to generate volitional movement. For those with bilateral involvement, body power is generally the preferred method of control because of the improved proprioception and reliability offered.
Keywords:
figure-of-8 harness; force and excursion; prosthesis; transradial prosthesis
Introduction
Body-powered prostheses for the upper limb are controlled by harnessing, capturing movements from the patient’s intact body segments. These movements, or control motions, become transferrable forces that actuate bodypowered components, including prosthetic elbows and terminal devices. This is most often accomplished by a transmission of movement through a series of harness straps and cables that are circumferentially anchored at a fixed point on the body and create a reaction at targeted body-powered components.1
Despite exciting developments in externally powered prosthetic options, body-powered prosthetic devices continue to be relevant as a viable and effective means of controlling upper limb prostheses. For many patients with bilateral involvement, body power is the preferred method of control because of the improved proprioception and reliability offered.2,3
Body-powered prostheses have stood the test of time for a variety of reasons. They involve relatively lightweight, durable components that create consistent, dependable reactions every time they are used. Because there is no need for an external power source, the dependency on a source of electricity for recharging is eliminated. An important and often overlooked advantage is the sensory feedback provided to users of body-powered devices. The users can feel how much tension they are exerting through the socket and harness and can feel how much movement is taking place at the terminal device. This one-to-one relationship of movement to sensory feedback allows the user to know where the prosthesis is in space.4
From the earliest concepts to current practice, novel approaches of capturing body movements to control upper limb prostheses have been developed, refined, and subsequently taught to future generations of prosthetists. This chapter reviews basic harnessing and body power theory, discusses body-powered options at each major level of upper limb amputation, and describes the available movements used to actuate body-powered components. Alternative harnessing strategies designed to address more specific needs along with their clinical relevance are also discussed.
Finger Prostheses
The past decade has seen the development of many body-powered choices for patients with a partial hand amputation, with commercially available options for those missing single or multiple fingers. Five body-powered systems, the PIP Driver, MCP Driver, and Thumb Driver (Naked Prosthetics), the Partial M-Finger (Liberating Technologies), and the X-Finger (Didrick Medical), use forward flexion of the remnant finger to drive flexion of distal prosthetic segments. The durability and grip strength offered by these systems vary with the different mechanical systems (Figures 1, 2 and 3).
PIP Driver
The PIP Driver is intended for finger amputations distal to the proximal interphalangeal joint, where sufficient length and flexion mobility of the residual middle phalanx remains. A proximal frame surrounds the proximal phalanx with a second frame surrounding the middle phalanx. Flexion and extension between these two frames are captured by a linkage joint that transmits flexion force and movement to a prosthetic distal interphalangeal joint, moving a prosthetic distal phalanx.
MCP Driver
The MCP Driver is intended for finger amputations approximating the PIP
joint. Flexion of the metacarpophalangeal (MCP) joints is transmitted to distal prosthetic interphalangeal joints through a metal linkage system (Figure 1). Current manufacturing constraints are such that the optimal amputation length for such systems is just proximal to the PIP joint as this provides an optimal functional lever arm for the body segment driving the system, while leaving enough length distal to the amputation to fit the necessary length of the prostheses. Given its robust stainless steel construction, the MCP Driver is currently the most heavy-duty prosthetic solution at this amputation level.
joint. Flexion of the metacarpophalangeal (MCP) joints is transmitted to distal prosthetic interphalangeal joints through a metal linkage system (Figure 1). Current manufacturing constraints are such that the optimal amputation length for such systems is just proximal to the PIP joint as this provides an optimal functional lever arm for the body segment driving the system, while leaving enough length distal to the amputation to fit the necessary length of the prostheses. Given its robust stainless steel construction, the MCP Driver is currently the most heavy-duty prosthetic solution at this amputation level.
Thumb Driver
Similar in some respects to the MCP Driver, the Thumb Driver is intended for amputations just distal to the MCP joint of the thumb. Driven primarily by movement at the carpometacarpal joint, and secondarily at the MCP joint of thumb, the Thumb Driver provides active flexion of a prosthetic interphalangeal (IP) joint and dynamic opposition against the remaining digits of the hand.
X-Fingers
The X-Finger system is intended for finger amputations distal to the metacarpophalangeal joint. It is anchored at the wrist joint with a linkage mechanism spanning the dorsum of the hand. As with the MCP Driver, flexion of the remnant fingers drives polycentric linkage mechanisms to flex the prosthetic fingertip. Variants for amputations both proximal and distal to the DIP joint are commercially available (Figure 2). The design of the X-finger is not as robust as that of the MCP Driver and it appears better suited to lighter duty applications.
Partial M-Fingers
The Partial M-Finger is also intended for finger amputation distal to the MCP. Similar in some respects to the MCP Driver, the M-Finger uses a cable system rather than a rigid linkage system, that is mounted on the dorsal surface of the hand. The mounting acts as the anchor, and metacarpophalangeal flexion creates cable tension that causes the partial finger element to flex volarly (Figure 3). Internal springs extend the interphalangeal joint in the absence of cable tension.
Partial Hand Prostheses
M-Fingers
M-Fingers use the movement of wrist flexion as the prime mover. As the user flexes the wrist, cables, which are anchored on a frame mounted proximal to the dorsal aspect of the forearm, are pulled. The frame acts as the anchor, and the action of wrist flexion acts to close the fingers about an object. The available force and excursion are both limited, making this type of prosthesis better suited for lighter duty applications (Figure 4).
Minnesota Split-Hand Prosthesis
The Minnesota split-hand device is an example of a prosthesis that uses wrist flexion and extension to activate a hinged, split hand. The hand is split at its base, making the thumb a stationary component, while the top section of the hand is activated with wrist flexion. Force and excursion are moderate to good with this type of device. It is appropriate for use in an individual with a congenital limb deficiency at the transcarpal level or a traumatic partial hand amputation (Figures 5 and 6).
Traditional Harnessing
Another option is the use of traditional body-powered terminal devices and a figure-of-8 harness for a partial hand amputee (Figure 7). This option can support carrying heavier loads as the durable construction of the terminal device can transmit considerable force through the broad surface area of the
harness. At this distal amputation level, the harness also allows the anatomic motions of wrist flexion and extension with full pronation and supination, which allows the user many options to position and then activate the prosthesis in space.
harness. At this distal amputation level, the harness also allows the anatomic motions of wrist flexion and extension with full pronation and supination, which allows the user many options to position and then activate the prosthesis in space.
![]() FIGURE 4 Photograph of Partial Hand M-Fingers. Wrist flexion causes the cable to become taught, closing the fingers. (Courtesy of Partial Hand Solutions, Southington, CT.) |
Transradial Applications
History
Artifacts and drawings have documented historical attempts at producing functional upper limb prosthetic devices. As early as the 16th century and continuing through the US Civil War, hook-like shapes were often fashioned as useful prosthetic implements for stabilizing, pulling, and carrying objects5 (Figures 8 and 9). Patent filings in the 19th century document the use of body-powered control through a harness, such as William Selpho’s 1857 patent for a body-powered prosthetic arm6,7 (Figure 10).
The primary body-powered system still currently in use can be attributed to Dorrance’s 1912 patent8 of the split hook. The original hook design (Figure 11) was refined into multiple models and shapes and is currently sold by the Fillauer Corporation.9 Both the Selpho and Dorrance designs demonstrate the use of a harness to both suspend and activate a cable that is pulled to open a terminal device.
Building on these original concepts, methods to efficiently transmit force through a harnessing system have been developed and refined. To better understand these concepts, it is useful to review force transmission and goals of efficiently harnessing a body-powered system.
Basic Concepts of Force Transmission
The goal when setting up body-powered prostheses is to create a transmission of force in the most efficient manner possible. To achieve this,
the following criteria must exist. (1) The prosthesis must be securely suspended or anchored to the individual’s body. (2) There must be a harness and cabling system designed to transmit body movements to efficiently activate a terminal device. (3) There must be an available power source in the form of movement generated by an intact body segment that can activate a body-powered component. (4) The body movement must be able to travel a sufficient distance to complete the action with adequate force to achieve the desired outcome.
the following criteria must exist. (1) The prosthesis must be securely suspended or anchored to the individual’s body. (2) There must be a harness and cabling system designed to transmit body movements to efficiently activate a terminal device. (3) There must be an available power source in the form of movement generated by an intact body segment that can activate a body-powered component. (4) The body movement must be able to travel a sufficient distance to complete the action with adequate force to achieve the desired outcome.
![]() FIGURE 8 Photograph of Götz’s artificial arm, 16th century, Weimar, Germany. (Courtesy of Peter Finer.) |
Figure-of-8 Harness System
The figure-of-8 harness system has several key component parts (Figure 12).
Axilla Loop
The foundation of the figure-of-8 harness is the axilla loop, which is also known as the anchor because this portion of the harness acts to both suspend the prosthesis and provide a stable anchor for the user to generate power to activate the terminal device. The axilla loop is located through the contralateral deltopectoral groove.
Suspension
The portion of the harness that is responsible for immediate vertical suspension is called the anterior suspensor
strap. It starts at the anchor, which is located at the contralateral shoulder, and ascends superiorly and laterally until it reaches the ipsilateral deltopectoral groove. The strap descends and is attached to the inverted Y strap, which connects the harness to the proximal aspect of the triceps cuff.
strap. It starts at the anchor, which is located at the contralateral shoulder, and ascends superiorly and laterally until it reaches the ipsilateral deltopectoral groove. The strap descends and is attached to the inverted Y strap, which connects the harness to the proximal aspect of the triceps cuff.
Control Strap
The control strap travels from the proximal axilla loop across the inferior aspect of the ipsilateral scapula. This portion of the harness connects to the cabling system that ultimately activates the terminal device. The orientation of the strap is an approximate 45° angle that travels over the distal portion of the ipsilateral scapula. This strap is referred to as the control attachment strap.
Harness Center Point
There are two common methods for creating the center point of the harness—a static sewn point and a stainless steel ring juncture (Figure 13). The ring style is designed to offer more range and flexibility of movement. The optimum location of the center juncture point is at the midline and distal to the C7 vertebra.
Juncture Between the Harness and the Cable System
Attached to the end of the control attachment strap is the proximal end of a cable. The cable travels through a metal housing that acts to create a smooth and continuous fulcrum. To ensure the housing maintains its shape, it is anchored at two reaction points in the system. The reaction points consist of a proximal cross bar attached to the triceps cuff and a distal baseplate and retainer on the forearm of the prosthesis (Figure 14). This continuous cable approach is termed a Bowden housing cable system.
A key feature of the Bowden cable system is that it has a fixed length of cable housing. This ensures that the captured force and excursion at the harness are efficiently transferred to the terminal device. The two reaction points ensure that the housing maintains the same curvature as the prosthesis is being activated, functioning as a smooth and continuous fulcrum for the cable as it travels through it. With an appropriate amount of curvature, there is an optimal distribution of the friction caused by the cable traveling through the housing.10
Power Generation
The body movements available to activate a body-powered component are dependent on the level of amputation. As a general rule, the more distal the amputation, the more options remain available for body activation. At the transradial level, the two key movements in body-powered activation are glenohumeral flexion of the ipsilateral shoulder and biscapular abduction. In the former, as the upper arm translates forward with the harness anchored to the contralateral shoulder, the cable is pulled and the terminal device opens. Relaxing this movement allows the rubber bands on the voluntary-opening terminal device to close. This movement generates excellent force and is a key prime mover in body-powered activation (Figure 15).
With biscapular abduction, the user moves both scapulae in opposing directions. This widens the back and thereby creates tension on the cable that opens the terminal device. This movement is very useful when operating close to the body and when the user desires to open the terminal device while keeping it in a stationary position (Figure 16).
The movements of glenohumeral flexion and biscapular abduction can be used discreetly or simultaneously in combination. The activation movement chosen depends largely on the location in space at which the user would like to activate the terminal device.
The Relationship Between Force and Excursion
The power the body must generate to activate a terminal device is referred to as the activation force needed for activation. The distance the intact segment of the body must travel is known as the activation excursion needed for activation. These concepts are illustrated in the two previously described examples of body activation. Glenohumeral flexion produces both substantial force and excursion. The ipsilateral shoulder muscles generate excellent force and can travel a substantial distance.
In contrast, biscapular abduction generates good force but more limited excursion because the two scapulae can travel only for a short distance when generating the movement.11
In contrast, biscapular abduction generates good force but more limited excursion because the two scapulae can travel only for a short distance when generating the movement.11
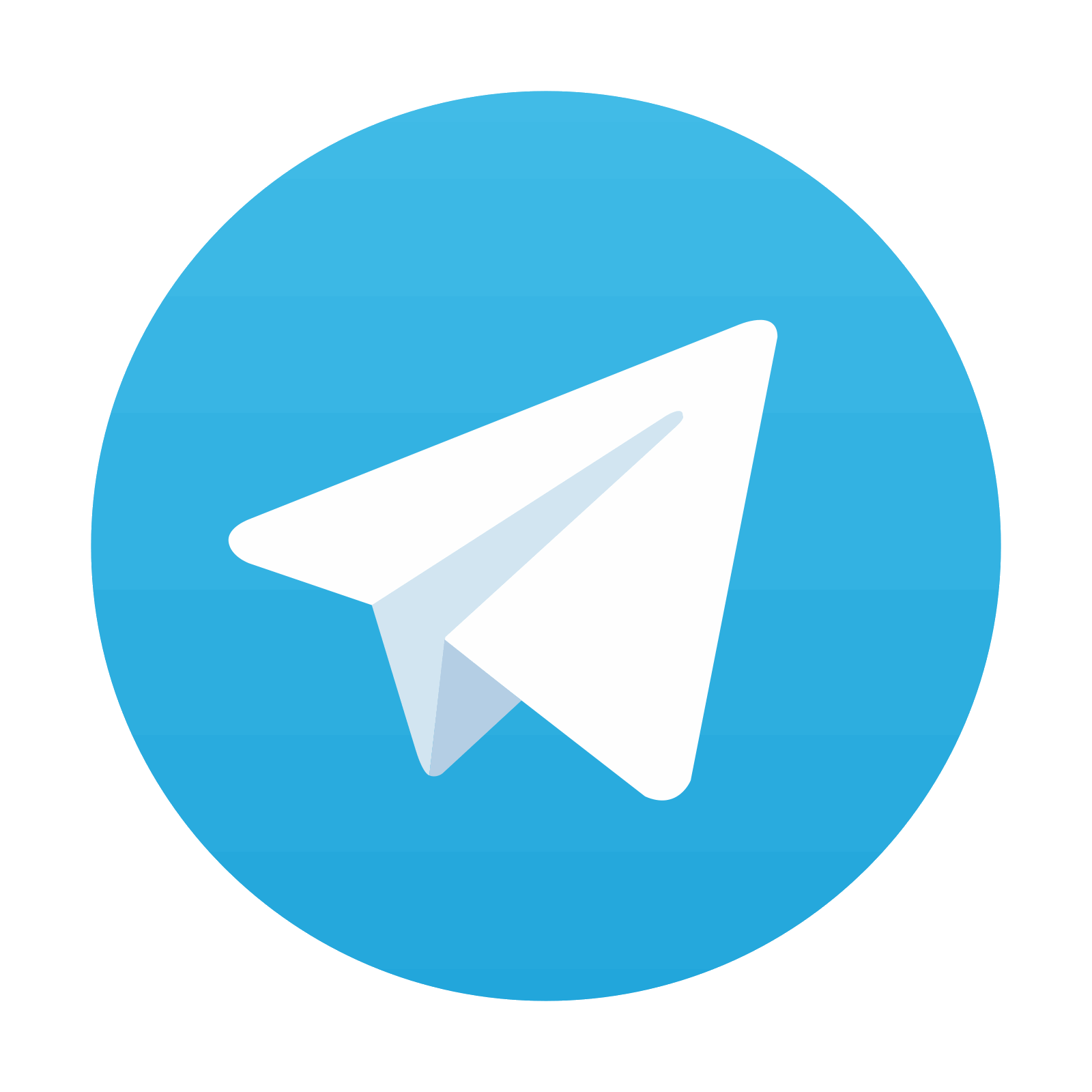
Stay updated, free articles. Join our Telegram channel
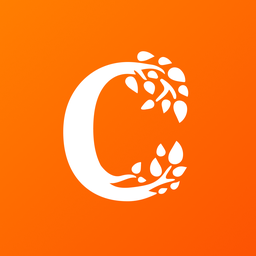
Full access? Get Clinical Tree
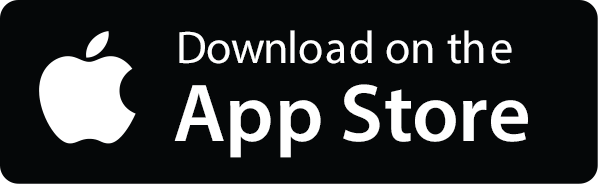
