Abstract
The stress–strain curve is a triple A-list subject. It always seems to be asked in viva examinations and is a definite top 10 core basic science question. In recent years this topic has been reinvented as it was becoming too predictable. We make no apologies for including the question in all of its various guises.
Introduction
The stress–strain curve is a triple A-list subject. It always seems to be asked in viva examinations and is a definite top 10 core basic science question. In recent years this topic has been reinvented as it was becoming too predictable. We make no apologies for including the question in all of its various guises.
Structured oral examination question 1
Stress–strain curve
EXAMINER: Can you draw the stress–strain curve for stainless steel?
COMMENT: Drawing is a vital component of the FRCS (Tr & Orth) Exam. A candidate is expected to illustrate to examiners what they are describing to aid discussion and inform techniques. Drawing also helps a candidate deal with the competency-level questions efficiently and accurately, gaining extra time to deal with the higher-order thinking questions, leading to higher scores.
CANDIDATE: The stress–strain curve demonstrates how a material subjected to an increasing tensile load deforms until failure (Figure 26.1).
Stress is force over area and has units of Newton per square metre.
Strain is change in length over original length; it has no units. It is usually expressed as a ratio or percentage.
COMMENT: Get this in about strain having no units first. Don’t wait to be asked ‘what are the units of stress?’ by the examiners. Most candidates know it’s a fairly blunt question.1
EXAMINER: How does force change the cross-sectional dimensions of the area it is acting on?
CANDIDATE: An object under stress experiences strain in the transverse direction as well as the horizontal direction.
Transverse strain is usually opposite to longitudinal strain, i.e. as an object gets longer, it gets thinner. As such, force can change the size of the cross-section it is acting upon. However, stress and strain are generally based on the original dimensions of the object.
COMMENT: An initial, slightly off-the-wall question can derail a nervous candidate before they have time to settle and has to be handled with skill. These less-obvious basic science questions are an attempt to move away from conventional book knowledge and force a candidate to apply first principles to problem-solving.
CANDIDATE: The initial section corresponds to elastic deformation. Strain is directly proportional to stress.
This is known as Hooke’s law.
EXAMINER: What happens to the molecular bonds when in this region of the graph?
CANDIDATE: The molecular bonds are stretched but not broken.
The gradient, i.e. steepness, of the straight line correlates to the material’s resistance to deformation. This is called Young’s modulus of elasticity.
The higher the Young’s modulus of elasticity, the smaller the deformation produced for a given load.
This here is the yield point, which is the maximum stress up to which a material undergoes elastic deformation. The yield point is the point on the stress strain curve that indicates the limit of elastic behaviour and the beginning of plastic deformation.
The non-linear section of the stress–strain curve corresponds to plastic deformation. The deformation is permanent and if the stress is removed, strain is not completely recovered and the material does not return to its original state.
EXAMINER: What happens to the bonds?
CANDIDATE: Molecular bonds are broken, and the molecules move too far apart to return to their original positions.
The ultimate tensile strength is the maximum stress that the material can sustain before fracture.
The fracture point is where the material eventually fails.
Stress at the fracture point can be slightly less than the ultimate tensile strength because the latter can cause the material to neck, which reduces its cross-sectional area and therefore the force required to fracture.
The area under the stress–strain curve represents the energy absorbed per unit volume of the material. It therefore indicates the energy absorbed by the material to failure. This is called toughness. A tough material takes a lot of energy to break it.
Comparing two forces acting on two surfaces can be misleading because this does not take into account the size of the cross-section. Stress indicates the intensity of force acting on a section. As such, it is a fairer comparison of loads acting on different surfaces.
EXAMINER: You seem to be changing around and mixing up stiffness and strength. What exactly do you mean by these terms?
CANDIDATE: Stiffness is stress–strain while strength is the load required to break a material and depends on plastic deformation.
COMMENT: Imprecise answer.
Stiffness and strength are terms often used interchangeably, but they are distinct mechanical properties.
Stiffness is defined as the slope of a force versus displacement graph.
Strength is an imprecise term and represents the degree of resistance to deformation of a material. A material is strong if it has a high ultimate tensile strength.
EXAMINER: Are you sure?
CANDIDATE: The steeper a stress–strain curve, the stiffer the material. The less steep the curve, the more flexible the material.
COMMENT: The slope of the stress–strain curve is the elastic (Young’s) modulus of the material.
Mechanical testing measures force on a construct that could consist of bone, ligament and possibly fixation device (plate) and the data obtained relates to properties of the construct as a whole. This is what engineers test in real life. Force and displacement are normalized for an individual material into stress and strain.
Force and displacement data will vary if the specimen dimension changes, even if it is from the same material. That is why we normalize force with its cross-section and displacement with its gauge length to arrive at stress and strain.
Try to understand rather than rote learn your biomechanical definitions otherwise with imprecise terminology you can get drawn into semantics and end up losing marks.
CANDIDATE: Hardness describes a material’s resistance to localized surface plastic deformation, e.g. scratch or dent. Hardness is not a basic mechanical property, but instead derived from a combination of other material properties, e.g. stiffness and strength. Hardness determines the wear resistance of a material. Under the same loading conditions, a harder material has a greater wear resistance than a softer material.
Toughness is a material’s ability to absorb energy up to a fracture. Toughness is derived from both strength and ductility of a material.
EXAMINER: So why is hardness important?
COMMENT: Basic science applied to clinical relevance.
Structured oral examination question 2
Stress–strain curve
EXAMINER: Stress–strain curve – label all the points, axis and nomenclature and describe what the areas underneath signify.
What is hardness?
CANDIDATE: The x-axis represents strain, which is change in length over original length. It has no units.
The y-axis is stress, which is force per unit area applied and has the units Newton per square metre (N/m2).
The area under the stress–strain curve up to the elastic limit depicts the modulus of resilience (MR), which signifies the ability of material to store or absorb energy without permanent deformation.
The whole area under the complete stress–strain curve represents the energy absorbed by the material to failure. This is known as the modulus of toughness, which shows the ability of a material to absorb energy up to fracture.
The Young’s modulus can be determined from the gradient of the line in the elastic portion of the stress–strain graph.
Hardness is a surface property of a material. It is the ability of a material to resist scratching and indentation on its surface. It has no association with the stress–strain curve.
COMMENT: Differentiating between isotropic and anisotropic materials is factual and rote-learned. The examiner has linked mechanical properties to Young’s modulus of elasticity to test whether a candidate is able to demonstrate a more advanced level of understanding.
CANDIDATE: An isotropic material behaves identically, irrespective of the direction of applied force. Examples include most orthopaedic metals, polymers and woven bone. The Young’s modulus of elasticity will be constant in all directions the force is applied to the material. With an anisotropic material the Young’s modulus varies depending on the direction of loading. Examples include cortical bone, ligaments.
We have the yield point here, which is the start of plastic deformation, and the ultimate stress, which is the maximum stress the material can withstand.
EXAMINER: Hold on; there are lots of different points on the graph that you haven’t mentioned (Figure 26.2a).
Figure 26.2a Stress–strain curve. Various points on graph include: 1, proportional limit; 2, elastic limit; 3, yield point; 4, ultimate tensile strength and 5, failure.
CANDIDATE: The point separating the elastic region and the plastic region is often difficult to identify in the curve. The usual convention is to define the yield strength, which is the intersection of the curve with a straight line parallel to the elastic deformation of 0.2% on the strain axis.
EXAMINER: There are three points on the graph that in some materials are very close to each other and often difficult to differentiate. These are2:
2. Elastic limit
If the stress slightly exceeds the proportional limit, the stress–strain curve is no longer linear but the material may still respond elastically. The curve tends to bend and flatten out. This continues until the stress reaches the elastic limit.
The elastic limit is the stress at which permanent deformation is seen and beyond this point the deformity will not completely recover if the force is removed.
3. Yield point
The point in the stress–strain curve at which the curve levels off and plastic deformation begins to occur.
EXAMINER: What is the yield point and how does it differ from the elastic limit?
CANDIDATE: Some textbooks describe the yield point as very fractionally later in the curve than the elastic limit. So the elastic limit is the point at which deformation stops being entirely reversible and the yield point is the point at which the material will have an appreciable elongation or yielding without any increase in load. However, the two values are virtually inseparable for most materials.
EXAMINER: What is the difference between (offset) yield stress and yield point3?
CANDIDATE: The yield point is that point at which the material starts to undergo plastic deformation.
As it is often difficult to pinpoint the exact stress at which plastic deformation begins in some materials, the (offset) yield stress is taken to be the stress needed to induce a specified amount of permanent strain, typically 0.2%. To confuse the issue some engineering textbooks define the yield point as the (offset) yield stress.
EXAMINER: What do we mean by the upper and lower yield point (Figure 26.2b)?
CANDIDATE: For certain materials, especially low-carbon steel alloys, the stress–strain curve produces both an upper yield point and a lower yield point. A distinctive ripple pattern following the upper yield point is seen and associated with non-homogeneous deformation.
The upper yield point is the maximum stress at which deformation starts. A fairly dramatic drop is then observed in the stress to the lower yield point, although the strain continues to increase. Eventually the material is strengthened by this deformation and the stress is increased with further straining (strain hardening).
The phenomenon is thought to occur due to dislocations occurring in the material.
Materials lacking this mobility, for instance by having internal microstructures that block dislocation motion, are usually brittle and don’t have separate upper and lower yield points.
Figure 26.2b Upper and lower yield points on stress–strain curve.
EXAMINER: What is happening at the yielding, strain hardening and necking stage of plastic deformation?
CANDIDATE: I am not completely sure.
COMMENT: This is not well explained in most revision FRCS (Tr & Orth) textbooks.
For score 8 candidates
The plastic region consists of different parts that are (1) yielding, (2) strain hardening and (3) necking.
Once the elastic limit (yield point) is passed, the material will undergo considerable elongation (yielding) with little or no increase in stress. This is indicated by the flatness of the stress–strain graph region in the plastic region. When the material is in this state it is often referred to as being perfectly plastic.
Strain hardening is where the plastic deformation increases a material’s resistance to further deformation. It occurs due to the material undergoing changes in its atomic and crystalline structure. Lattice defects occurring in the material become too much in number and they restrict each other’s movement. Essentially traffic jams have been created that obstruct movement of lattice defects.
An example is cold working of metal alloys. Strain hardening increases the yield point at the expense of lower ductility and toughness. Thus, a material that has received prior deformation will be stronger than an undeformed material.
In the region after the ultimate strength point, stretching occurs with an actual reduction in the stress. This is a result of necking or waisting in the material, whereby the cross-sectional area is reduced.
COMMENT: Although the stress the material can withstand is reduced after the ultimate strength point, this is not due to any loss of material strength but due to the reduction in cross-sectional area of the bar. If the cross-sectional area of the narrowest part of the neck is used to calculate the stress, then the true stress-strain curve is obtained.
Structured oral examination question 3
Stress–strain curve
EXAMINER: Draw me the stress–strain curves for materials used in THA (Figure 26.3a).
What is the stress–strain curve for ceramic, UHMWPE and stainless steel?
COMMENT: Sharp intakes of breath if you haven’t read up beforehand, but relatively easy if you have worked through a pre-exam answer.
CANDIDATE: Ceramic is a very brittle material while UHMWPE is plastic. Stainless steel is ductile.
Ductility is a measure of the ability of a material to be drawn out that is plastically deformed, before failure.
Stainless steel 316 is moderately strong, tough and a highly ductile material (this allows bending before catastrophic failure).
Figure 26.3a Stress–strain curve for materials used in THA.
EXAMINER: What is happening with this graph (Figure 26.3b). Can you interpret it for me?
Figure 26.3b Strain hardening of a material.
COMMENT: This is demonstrating strain hardening of a material.
When loaded, the strain increases with stress and the curve reaches the point A in the plastic range.
If at this stage, the specimen is unloaded, the strain does not recover along the original path AO, but moves along AB.
If the specimen is reloaded immediately, the strain increases with stress from B to A but via another path (the slope of stress–strain line is steeper indicating that the material has got stiffer than before) and reaches the point C, after which it will follow the curvature if loading is continued.
If the specimen would not have been unloaded, after point A, the stress–strain curve would have followed the dotted path AD′.
Comparison of paths ACD and ACD′ shows that due to cold working (plastic deformation), the yield strength and ultimate strength have increased. Ultimate strength increased from S1 to S2. Since the ductility has decreased the work to failure on reloading also decreases. Thus strain hardening reduces toughness.
CANDIDATE: UHMWPE has low friction and high impact strength, excellent toughness and low density, ease of fabrication, biocompatibility and biostability. Its major drawback is wear.
There have been changes in the way PE is manufactured in recent years. Gamma irradiation in air is bad due to generation of free radicals which can become oxidized and …
EXAMINER: That’s fine, we don’t need to go there.
Structured oral examination question 4
Stress–strain curve
EXAMINER: Stress–strain curve of different materials (ceramic, SS, plastic, bone, ligament), how are they different (Figure 26.4)?
Figure 26.4 Stress–strain curves of different materials.
COMMENT: Essentially this is describing and interpreting the stress–strain curve for brittle (ceramic), ductile (CoCr) and plastic (elastic) materials. Bone (mostly brittle but with a little plastic deformation before failure) doesn’t neatly fit into one of the above categories. Leading on from bone the examiners may choose to throw into the discussion isotropic versus anisotropic material properties. Be careful with bone as the stress–strain curve is different for cortical and cancellous bone.
EXAMINER: Describe how each material behaves when loaded.
COMMENT: Candidates should be able to discuss the elastic and plastic regions of the graph and how they differ between the various materials. This question is a different way of essentially testing the factual knowledge of the stress–strain curve.4
CANDIDATE:
Materials fracture by a process of crack initiation and propagation.
All materials are rough and contain defects and cracks at the microscopic level.
Crack progression in a brittle fracture is associated with little plastic deformation whereas ductile fracture involves significant plastic deformation.
A brittle material fails suddenly, soon after the yield point.
The appearance of a brittle fracture is characterized by a clearly defined fracture surface generated across the material.
With a ductile fracture there is considerable deformation after the yield point that results in a characteristic ‘drawn out’ appearance.
Structured oral examination question 5
Stress–strain curve
EXAMINER: Can you draw out the stress-strain curve – label all the points, axis and areas of interest (Figure 26.5a)?
What happens at the yielding, strain hardening and necking regions of the graph (see above)?
Stress–strain curve of materials with three different moduli of elasticity. Pick three items from a display in front of me that match those stress–strain curves. Describe their material properties (ceramic/bone/ligament) (Figure 26.5b).
Figure 26.5a Stress–strain curve diagram for ductile material (stainless steel).
Figure 26.5b Stress–strain curve, different materials.
CANDIDATE: A brittle material is one that exhibits a linear stress–strain relationship up to the point of failure. It undergoes elastic deformation only with little to no plastic deformation. Characterized by the fact rupture occurs without any noticeable prior change in the rate of elongation. The classic example to mention is ceramic. Other examples would include PMMA and glass (Figure 26.5c).
Although cortical bone exhibits some plastic deformation it behaves more like a brittle material than a ductile material. It deforms slightly before failure or fracture. Cortical bone displays anisotropic behaviour with its elastic modulus depending on the direction of loading. It is also viscoelastic, with the stress–strain curve varying depending on the rate of loading.
Ligament is also viscoelastic. The toe region of the stress–strain curve is seen predominantly in ligaments and tendons. It denotes a non-linear elastic phase. Initially, a large distance (strain) is travelled under minimal stress as the crimped fibres straighten out. The characteristic shape is produced by the increase in the number of collagen fibrils resisting the strain as the slack fibrils are straightened and stretched, reducing the crimp pattern. Once all the collagen fibrils are straightened and stretched the slope is more or less constant (linear region).
Figure 26.5c Stress–strain curve for PMMA. Essentially brittle with little plastic deformation before failure.
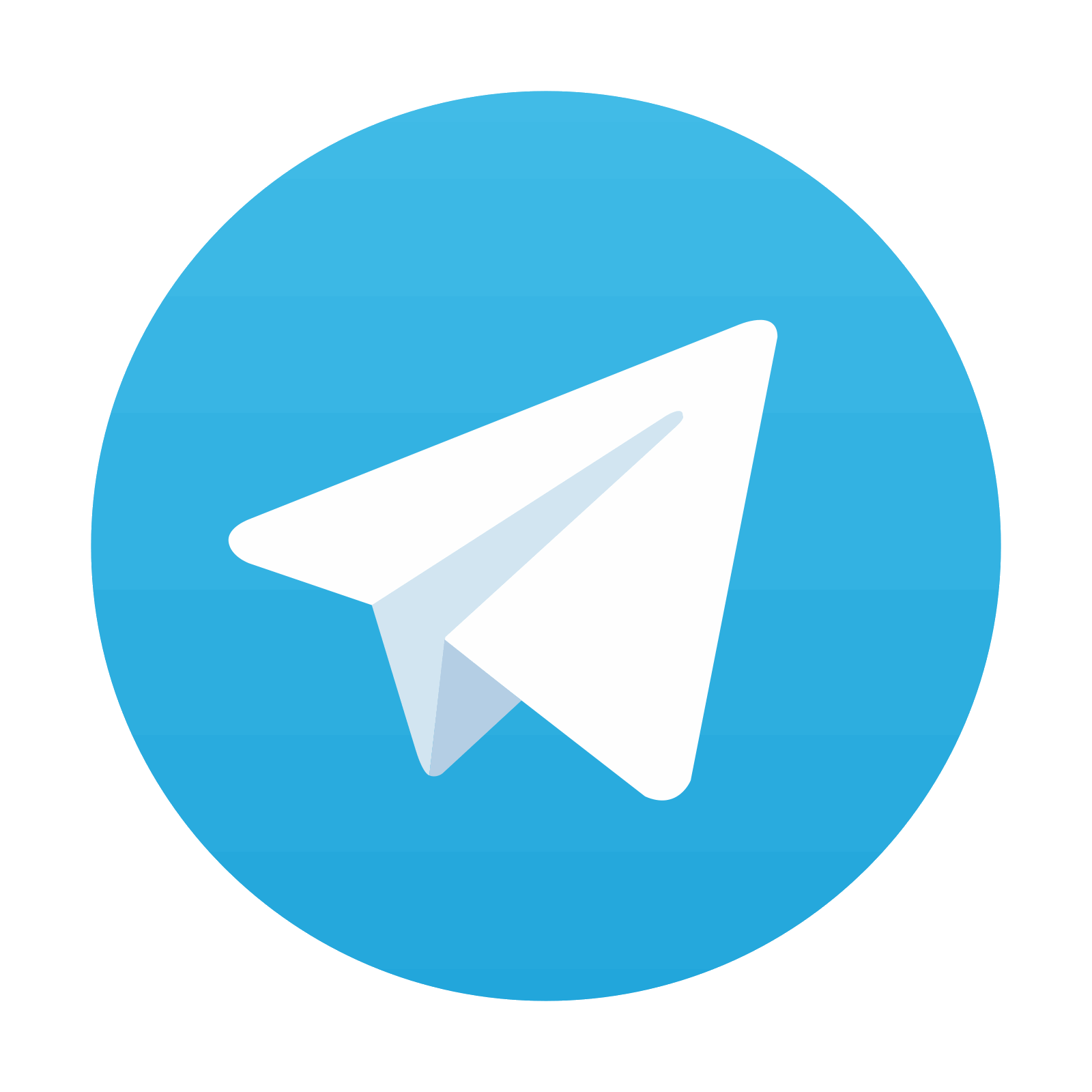
Stay updated, free articles. Join our Telegram channel
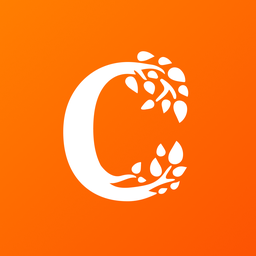
Full access? Get Clinical Tree
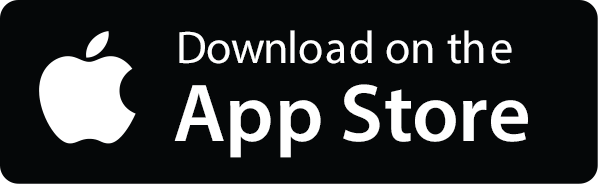

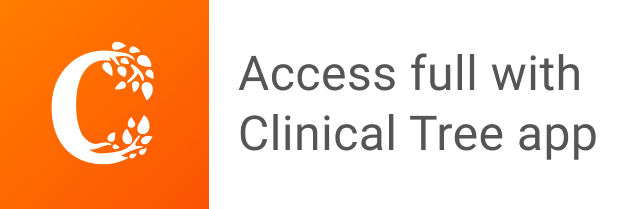